Introduction to Warehouse Challenges
Warehouses are an intricate ecosystem with several different processes working in tandem to serve customers effectively. Warehouse management challenges act as a major roadblock in the efficiency and productivity of the warehouses and can cause serious damage to the complete warehouse workflow.
Recent events have warranted warehouses to change their business dynamics and stay profitable while fulfilling customer orders as well and the best way of ensuring sustainability and longevity for your warehouse is to overcome some of the common warehouse management challenges.
Managing laborers efficiently, making the most use of available warehouse space, and adapting to seasonal demands and other issues require warehouse managers to stay on top of their game at all times and get ahead of warehousing challenges.
Let's explore some of the key challenges in warehouse management.
Top Warehouse Management Challenges (2025)
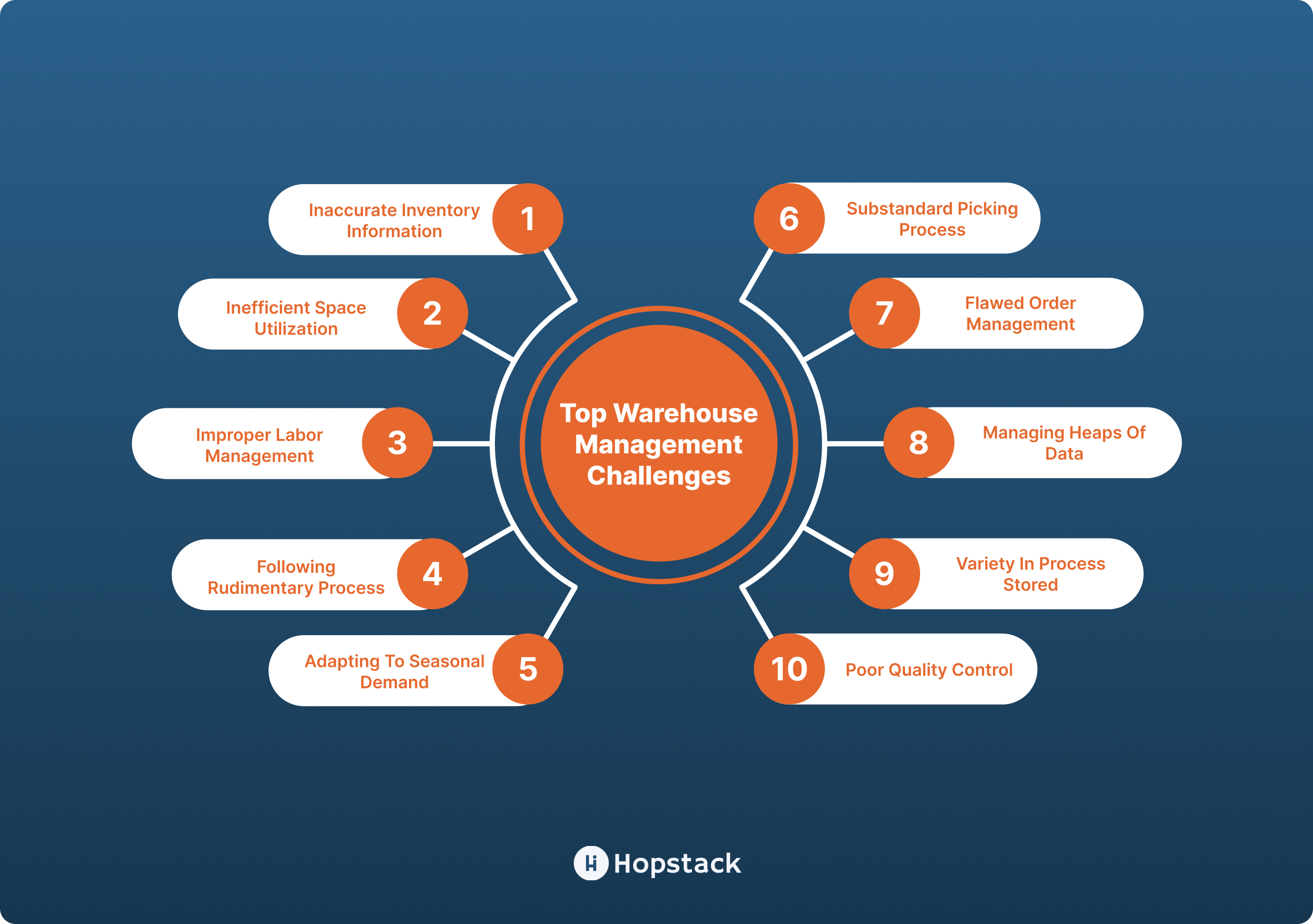
This article will highlight 10 of the most common warehouse management challenges and how they affect your business.
1. Inventory Shrinkage Due to Theft and Damage
Challenge: Inventory shrinkage, particularly due to theft and damage, can erode profit margins significantly. This often occurs in high-value items or during periods of increased warehouse activity, such as peak seasons.
Example: A warehouse storing electronics might face inventory shrinkage due to internal theft, where employees conceal items in waste containers to be retrieved later.
Solution: Implement advanced surveillance systems coupled with AI-powered analytics to detect unusual patterns of employee behavior. Conduct regular audits and introduce secure areas for high-value items, along with stringent access controls. Train staff on loss prevention techniques and establish a clear, enforced policy on theft.
2. Inconsistent Order Fulfillment Accuracy
Challenge: Mistakes in picking, packing, and shipping orders can lead to high return rates, customer dissatisfaction, and lost sales. These inaccuracies often occur when pickers rely on manual processes or when SKU counts are high and complex.
Example: In a high-volume e-commerce warehouse, an order might be shipped with the wrong size or color due to the picker grabbing the incorrect item from a poorly organized shelf.
Solution: Adopt pick-to-light or voice-directed picking systems that guide workers to the exact location and quantity of items. Regularly train staff on new SKUs and update bin locations in the warehouse management system (WMS) to reflect the most efficient warehouse layout.
3. Bottlenecks in Receiving and Putaway Processes
Challenge: Delays in receiving and putaway processes can create bottlenecks, leading to congestion at docks, delayed order processing, and increased labor costs. This is often due to a lack of coordination between receiving and storage teams.The average warehouse capacity utilization is only 68% proving that warehouse spaces are not being utilized efficiently
Example: A warehouse might receive a large shipment that sits idle for hours because the receiving team is not synchronized with the putaway staff, causing dock congestion.
Solution: Integrate your WMS with advanced scheduling software that coordinates warehouse receiving with available storage locations in real-time. Implement cross-docking where possible to minimize handling and speed up the putaway process. Employ dynamic slotting strategies that allocate space based on current demand and inventory levels.
4. Inflexibility in Handling Seasonal Fluctuations
Challenge: Warehouses often struggle with scaling operations during peak seasons, resulting in backorders, delayed shipments, and overwhelmed staff. Rigid systems and processes exacerbate this issue.
Example: A fashion retailer’s warehouse might struggle to cope with a surge in online orders during a holiday sale, leading to delayed shipments and customer complaints.
Solution: Adopt flexible automation solutions such as automated warehouse management systems or mobile robots that can be scaled up or down based on demand. Implement a temporary workforce strategy with pre-trained seasonal workers ready to be onboarded quickly. Use predictive analytics to better forecast seasonal demand and plan inventory levels accordingly.
5. Complexity in Managing Multiple Channels (Omnichannel)
Challenge: Managing inventory across multiple sales channels (e.g., online, in-store, third-party marketplaces) adds complexity to inventory tracking, order fulfillment, and returns management. Each channel may have different requirements and customer expectations.
Example: A retailer might oversell a product online because inventory was not updated in real-time when items were sold in physical stores.
Solution: Use a centralized inventory management system that provides real-time visibility across all channels. Implement distributed order management (DOM) software that automatically routes orders to the most appropriate fulfillment location. Regularly synchronize inventory data across all channels to prevent overselling and stockouts.
6. Labor Shortages and High Turnover
Challenge: Labor shortages, particularly in regions with low unemployment rates, make it difficult to hire and retain skilled warehouse workers. Labor costs can comprise nearly 65% of the total warehouse budget. High turnover exacerbates training costs and decreases productivity.
Example: A warehouse may experience delays in order processing because it is unable to maintain a full staff during busy periods, leading to reliance on inexperienced temporary workers.
Solution: Invest in automation to reduce dependency on manual labor, such as autonomous mobile robots (AMRs) for material handling. Offer competitive wages, benefits, and career development opportunities to retain skilled workers. Develop an employee referral program and partnerships with local vocational schools to maintain a pipeline of qualified candidates.
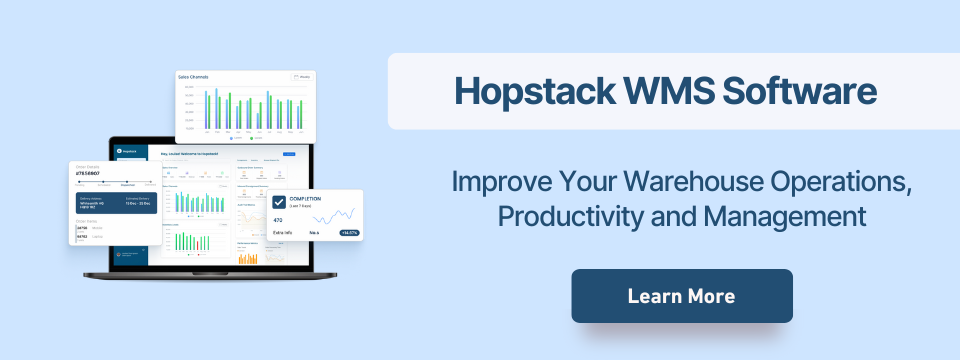
7. Inefficient Returns Processing (Reverse Logistics)
Challenge: Handling returned goods efficiently is a significant challenge, as it requires additional processing steps, such as inspection, repackaging, and restocking. Slow returns processing can lead to inventory imbalances and dissatisfied customers.
Example: An online retailer might face backlogs in returns processing after a major sales event, leading to delays in issuing refunds and restocking items.
Solution: Create a dedicated returns processing area within the warehouse equipped with the necessary tools and staff to handle returns efficiently. Use returns management software that integrates with your WMS to track returned items and automate the inspection and restocking processes. Implement a standardized return policy that clearly outlines the steps and timeline for processing returns.
8. Environmental and Sustainability Challenges
Challenge: Increasing pressure to reduce environmental impact is challenging for warehouses, particularly in areas like energy consumption, waste management, and packaging. Meeting sustainability goals while maintaining efficiency requires significant changes in operations.
Example: A warehouse using outdated lighting and heating systems might have high energy costs and a large carbon footprint, contradicting corporate sustainability goals.
Solution: Invest in energy-efficient lighting, such as LED systems with motion sensors, and upgrade HVAC systems to reduce energy consumption. Implement a recycling program for packaging materials and explore the use of biodegradable packaging. Use data analytics to monitor and optimize energy usage across the facility.
9. Adapting to Technological Advancements
Challenge: Rapid advancements in warehouse technology, such as AI, robotics, and IoT, present opportunities but also challenges in terms of adoption, integration, and training. Lagging behind in technology can lead to competitive disadvantages.
Example: A warehouse that relies on outdated manual tracking systems might struggle to compete with more technologically advanced competitors that use AI for demand forecasting and robotic picking systems.50% of a picker's time is spent in movement and not picking items.
Solution: Regularly evaluate emerging technologies to determine their potential ROI and applicability to your operations. Start with pilot programs to assess the impact of new technology before full-scale implementation. Provide ongoing training for staff to ensure they are comfortable and proficient with new systems.
10. Challenges in Managing Hazardous Materials
Challenge: Warehouses dealing with hazardous materials face unique challenges related to safety, compliance, and storage requirements. Improper handling can lead to accidents, regulatory fines, and environmental harm.
Example: A chemical warehouse might face fines if it fails to properly label hazardous materials or store them in accordance with legal requirements, leading to potential leaks or spills.
Solution: Implement a robust Hazardous Materials Management System (HMMS) that ensures compliance with all relevant regulations, including proper labeling, storage, and handling procedures. Train employees on the specific safety protocols for hazardous materials, and conduct regular drills to prepare for emergencies. Utilize specialized storage solutions, such as flame-resistant cabinets or containment pallets, to safely store hazardous substances.
Conclusion
Intelligent warehouse management and execution systems like Hopstack help in digitizing different warehouse processes to make it easier for managers to keep an eye on every operational detail and help you overcome challenges in warehouse management.
Our team of experts collaborates with warehouses to understand their issues and warehouse challenges and offer solutions to help them in the long run.
Robust inventory management and optimization, paperless automated picking in warehouse, multi-channel order management, and seamless integration with devices increase warehouse efficiency which, in turn, enables them to serve more customers and grow revenue.
FAQs
How can warehouse managers deal with labor shortages during peak seasons?
To manage seasonal labor shortages, many warehouses now rely on flexible staffing models, cross-training, and labor forecasting tools. Others invest in automation — like pick-to-light systems or AMRs — to reduce reliance on temporary workers. Having SOPs and task-specific training materials ready also helps new workers become productive faster during high-volume periods.
What role does poor warehouse layout play in productivity bottlenecks?
How can fragmented tech stacks create operational challenges in warehouses?
When WMS, ERP, order management, and shipping tools aren’t properly integrated, it leads to delayed inventory updates, missed orders, and inconsistent reporting. These silos increase manual work and reduce visibility. Using APIs, middleware, or centralized platforms helps unify data flows, enabling real-time tracking and process automation across the warehouse.
What’s the impact of poor demand forecasting on warehouse performance?
Inaccurate forecasting causes overstocking (leading to storage constraints and waste) or stockouts (which delay fulfillment and damage customer trust). It also affects labor planning and replenishment cycles. To mitigate this, warehouses should align with demand planning teams, review historical data trends, and build flexible inventory buffers for high-variability SKUs.
How can a WMS implementation fail if not properly managed?
WMS projects often fail due to a lack of process alignment, inadequate user training, or skipping key steps like UAT (user acceptance testing). Teams may customize too early or implement workflows that don’t reflect actual operations. Without change management and ongoing support, even the most advanced WMS will underperform.
Why is reverse logistics a growing warehouse challenge?
Returns processing has become more complex with rising ecommerce volume. Warehouses must sort, inspect, restock, or dispose of returned goods — often under tight timelines. Without dedicated zones or workflows for returns, they can clog receiving docks and disrupt inbound operations. A structured reverse logistics process improves efficiency and salvage rates.
How can warehouses maintain flexibility while scaling across multiple locations?
Scalable operations require standardized processes, centralized inventory visibility, and flexible technology. A cloud-based WMS can help maintain consistency across sites while allowing for warehouse-specific rules. Scalable labor practices, such as mobile task assignments or centralized training modules, also support multi-site growth without performance dips.