Order fulfillment is the word of the market for e-commerce enterprises. One of the most critical variables in a warehouse’s long-term performance is speed and accuracy. If a brand wants to be successful, it must properly store and organize its inventory levels so that it can choose, pack, and transport it efficiently, quickly, and accurately.
Here is where it becomes critical to have proper warehouse optimization and layout.
Warehouse layout optimization is a technique firm should not undertake without due consideration. It requires a solid awareness of what a brand is dealing with and the limits before it can take action to enhance its warehousing architecture and procedure. Once the gaps and areas of unmet demand are identified, optimizing the new warehouse plan can be started in detail.
A good warehouse layout design can help to optimize the Warehouse processes and reduce shipment times. However, if a brand isn’t maximizing the warehouse space available- it can have a detrimental impact on the supply chain, workflow, and shipment delays.
Whether a firm is starting a new warehouse or already has one, it will need to optimize warehouse layout to improve productivity. Although there is no one-size-fits-all solution for warehouse layout design, there are several guidelines that can be followed to maximize the warehouse's productivity and income.
Types of Warehouse Layouts/ Warehouse layout examples
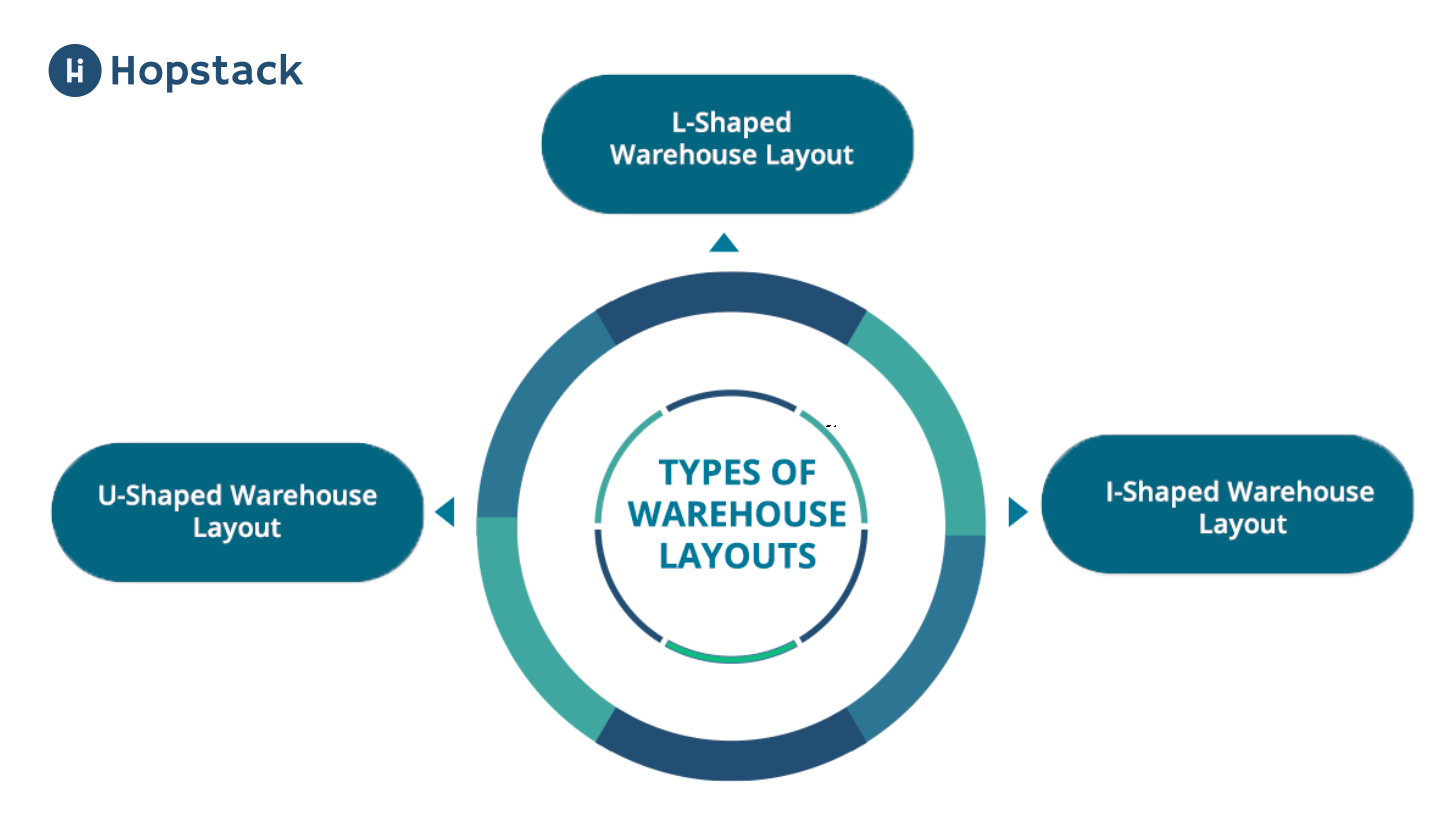
The different kinds of warehouse layouts include:
U-Shaped Warehouse Layout
This arrangement is ideal for any size warehouse. The loading/unloading areas are on the same side of the structure. However, anyone can separate them by this layout design.
L-Shaped Warehouse Layout
On one side of the building is the goods reception zone, while the dispatch area is opposite. The rest of the facility's capacity can be dedicated to product storage and order fulfillment.
I-Shaped Warehouse Layout
Here goods are received and dispatched on opposing sides of the warehouse, with storage in the middle.
Depending on the business needs, brands must make an informed decision on the types of warehouse layout.
Let’s look at some tips covering the significant aspects of logistics and warehouse functions.
Top Strategies For Warehouse Layout Optimization
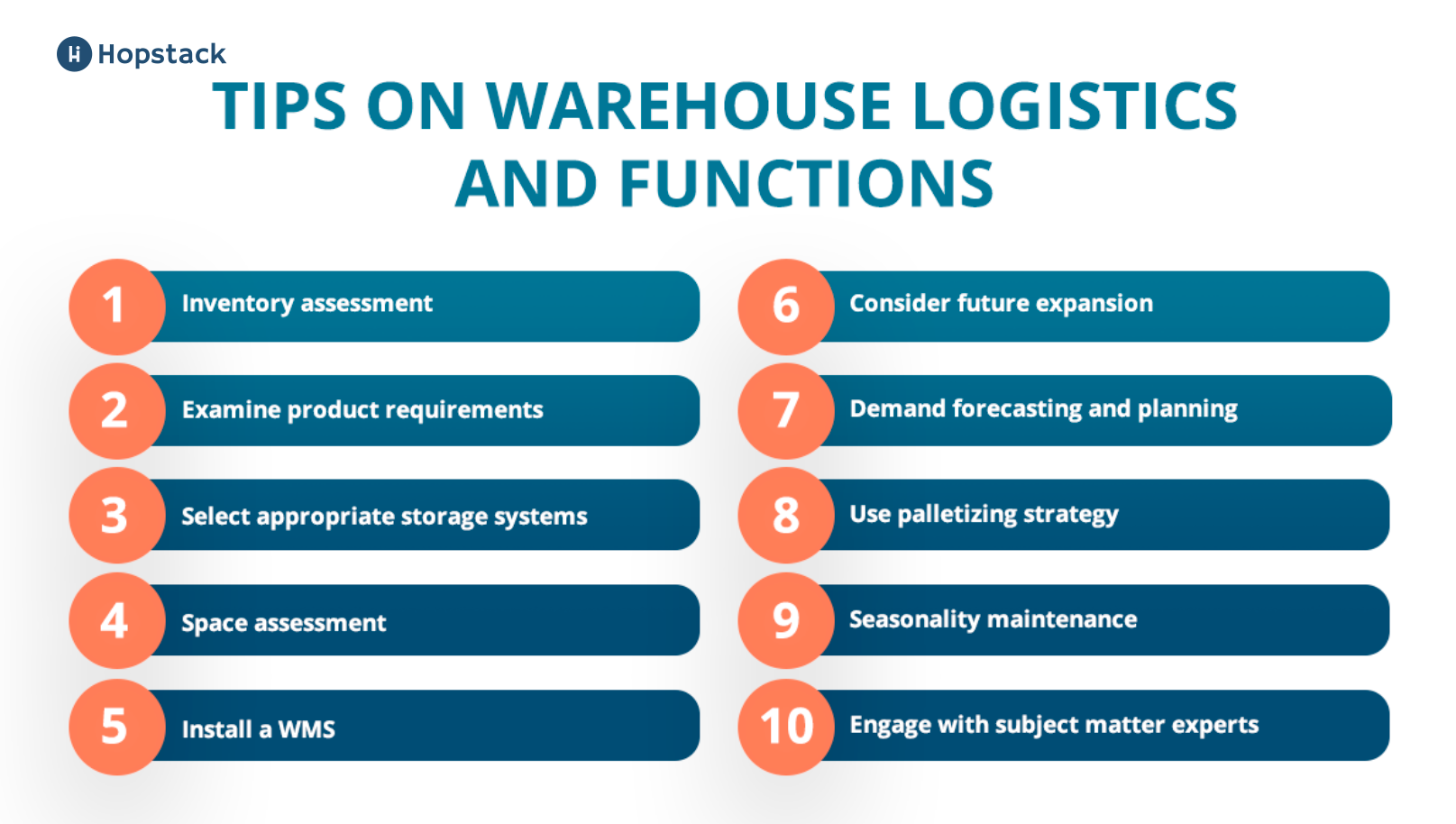
Tip 1: Examine the current throughput of the warehouse or inventory assessment
Identifying and assessing difficulties in the logistics facility is the first stage in warehouse layout improvement. Knowing what warehouse inefficiencies need attention is critical for determining improvement opportunities, Inventory management planning, and making wise decisions.
Advanced warehouse automation platforms help with inventory assessment and optimization.
Tip 2: Examine the requirements for the product
After assessing the facility's condition, an evaluation of the sort of product held and the company's needs can be focused on. This method bears much weight for warehouse layout optimization because certain businesses require a dedicated location for a specific task. Value-added service (VAS) stations, for example, convert items and meet unique consumer needs (e.g., screen-printing a T-shirt with a personalized message).
Tip 3: Select appropriate storage systems
It's critical to choose the correct storage system to maximize the productivity of your logistics operations while saving Vertical space in the warehouse. The organization should consider whether it should automate or continue handling its warehouse activities manually.
When determining whether to use an automatic or manual storage system many considerations come into play. Although there is no specific formula for choosing the best solution, automating is an active option to increase productivity, maximize warehouse storage space, and improve the operators, merchandise, and storage systems' safety.
Tip 4: Space assessment
The next step in warehouse layout optimization is to plan space distribution and space utilization. The five areas of a warehouse include goods receipt, storage, order processing, packaging in warehouse ( A good packing warehouse process ), and returns control, each dedicated to a specific task.
To guarantee an optimal flow of motions, each of these regions should have its own space (for example, the warehouse storage and picking areas should be close to one another so that there is never a shortage of goods to pick and effective warehouse picking optimization. Other aspects of Warehouse Designs, such as offices, changing rooms, and production lines, must also be considered. New-age automated warehouse software platform offers space optimization controls and AI-powered facility layout suggestions that help warehouses save labor costs and fulfill orders more effectively.
Tip 5: Install a WMS
The usage of a warehouse management system to digitize the warehouse facility is perfect for optimizing the layout. The WMS uses rules and algorithms to distribute products in the warehouse. It reduces the number of product movements, whether handled by automated or manual equipment. For eg. Hopstack’s proprietary AI provides businesses with inventory forecasting and demand planning.
Read The Detailed Guide on Complete Warehouse Optimization
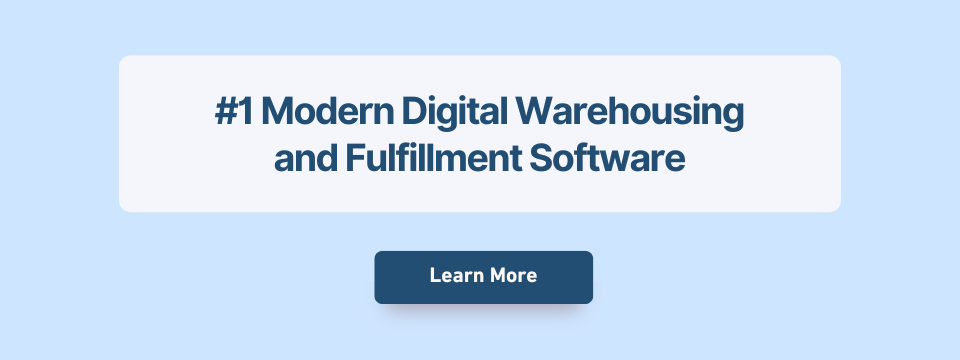
Tip 6: Make room for future expansion
It's critical to consider its prospects while redesigning a logistics facility. It's pointless to rearrange the warehouse if it needs to be done again as the number of SKUs or demands grows.
Tip 7: Demand forecasting and planning
To accommodate high-demand periods, use forecasting and demand planning tools to add extra storage capacity to the warehouse plan. Also supplier lead times, stock-out charges, and inventory, carrying expenses should be considered in the storage estimates. Thus warehouse estimations can be optimized to save money and keep lead times in line with demand.
Tip 8: Use palletizing strategy
In a warehouse, grouping boxes with pallets should be done. Palletizing stock overflow is another low-cost, low-commitment option to deal with seasonal demand spikes. Placing excess goods on pallets and storing these pallets in a designated overflow area instead of adding extra shelf storage into the warehousing plan to account for substantial demand cycles. Pallet racks make the racking system efficient. Palletized inventory can be moved to shelves and bins when space becomes available.
Tip 9: Seasonality maintenance
For big, seasonal swings in your business' demand cycles, on-demand warehousing may be the ideal option. During high-volume periods, outsourcing warehouse requirements allows for maintaining of in-house personnel consistently; while addressing excessive order fulfillment variances.
Tip 10: Engage with subject matter experts
To begin, the strategy for optimizing your warehouse for seasonal demand should include suggestions from subject matter experts in each of the warehouse's critical areas. These professionals should've worked through many seasonality cycles in your warehouse, business, and sector.
They'll have seen the bottlenecks, stock-outs, and overflow caused by seasonality in your warehouse. Such subject matter experts will guide in implementing AI and ML-based solutions to face seasonality and demand fluctuations using historical data.
Contact our subject matter expert for more help.
How do cloud-first and AI-powered warehouse management systems help optimize the warehouse layout?
- Analyze space and floor plans to determine and provide warehouse layout optimization opportunities.
- Maintain optimum stock rotation to enable a cost-effective use of space.
- Helps make effective decisions to choose the right space location, the basis of the movement of materials.
- Improve physical movement of workers and materials from inbound to outbound logistics.
- AI-powered WMS indirectly impacts the overall warehouse operating cost by saving excessive time spent on the placement and retrieval of goods.
- Time, effort, and money saved with an optimized warehouse layout directly results in happy associates, satisfied customers, and an increase in revenue.
Follow warehouse layout best practices and warehousing design principles to reap maximum benefit. To know more about optimizing warehouse layout using a warehouse management or inventory management software, schedule a call with us.