Ask any warehouse manager, and they'll tell you — an inefficient putaway process can cripple operations. Recent studies show that 45% of warehouse managers acknowledge significant inefficiencies in their putaway workflows. And it’s no surprise: poor putaway practices lead to stockouts, backorders, damaged goods, and unsafe working environments.
In a warehouse, movement never stops. From the moment products hit the receiving dock to the second they ship out, each process must flow seamlessly — and putaway sits at the heart of it all. Done right, it improves pick, pack, and ship times, boosts inventory visibility, and maximizes storage space. Done wrong, and the whole operation slows down.
An efficient, accurate putaway process isn’t just a nice-to-have — it’s a competitive advantage in today's fast-moving supply chain landscape.
What is the Putaway Process in Warehouse?
The putaway process is the critical step of moving goods from the receiving dock to their proper storage locations. After a shipment arrives, products must be inspected, sorted, and placed in designated areas - whether that’s shelves, bins, pallets, or containers - ready for easy retrieval during order fulfillment.
Putaway starts earlier than many realize. In the warehouse processes, It begins the moment a purchase order is placed with a vendor. Once goods arrive, how they’re stored can make or break the picking efficiency later. Smart putaway reduces unnecessary travel time for workers, optimizes warehouse space, and helps maintain real-time inventory visibility.
The ultimate goal? To ensure every item is stored in the right spot - fast, error-free, and with minimal handling - so that the picking process becomes quicker, safer, and more accurate. This can effectively make warehouse operations more efficient, and also helps in getting the most out of the warehouse space.
Benefits of Optimized Warehouse Putaway Process
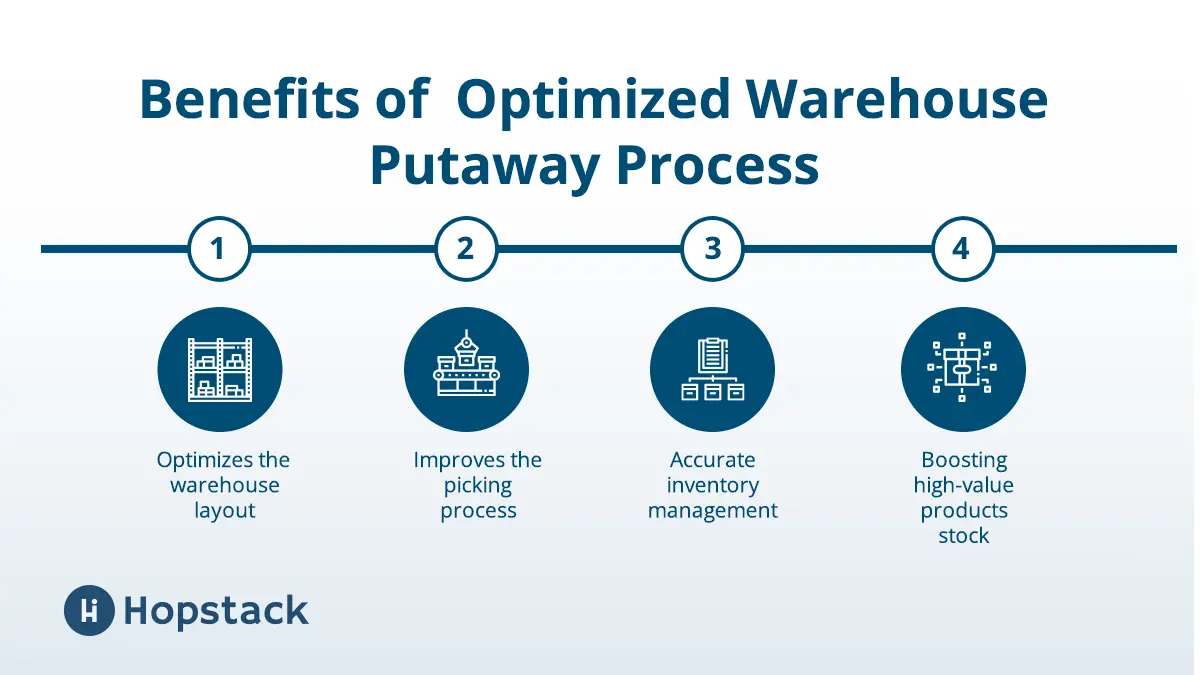
Having an efficient warehouse putaway process in place can translate into cost-saving and quicker outbound operations as explained earlier. Here are some of the key benefits a warehouse can experience by implementing a structured and effective putaway process:
Optimize the Warehouse Layout
With a carefully planned putaway process warehouse workflow, you can get the most out of your existing warehouse layout space. By combining products of the same shape and size in one location and segregating them on several different criteria, it becomes easier to store the products in their respective places. This way, you can prevent disorderly inventory management that can restrict warehouse associates from free movement and timely picking and warehouse packing.
Improve the Picking Process
Pickers spend more than half of their normal working time just wandering around the warehouse searching for the products in their order. In fact, travel can make for 50% of the total picking time and half of the overall labor cost as well. With a robust putaway process in place, they can drastically reduce the amount of time it takes to search for products and fulfill an order. An efficient automated picking process is absolutely important.
Faster Picking and Fulfillment
Strategic putaway - where high-velocity items are stored closer to picking zones - can reduce picker travel time by up to 30%, according to a Zebra Technologies warehouse study. This directly accelerates order turnaround and helps maintain SLAs, especially during peak periods like Black Friday or seasonal surges.
Accurate Inventory Management
Inaccurate inventory management and human-induced errors can prove costly to the business. The average picking error rate in the warehouse industry is somewhere between 1% and 3%. This relates to anywhere between $50 to $300 average cost per error with up to 13% drain on profitability. With a putaway process in place, you can keep accurate track of where each product is, what’s its quantity, and a lot more. It also reduces the chances of losing or misplacing an item.
Boost High-Value Products Stock
Keeping high-volume products at a place where they are easy to pick and keep a track of, helps in boosting the stock of that product. It also prevents pickers from searching the warehouse every time for a particular product and hence delaying the order fulfillment. If the stock is decreasing, you’ll know instantly.
Enhanced Warehouse Safety
Properly categorized and ergonomically stored inventory reduces clutter and risk-prone areas like overstacked pallets or blocked aisles. OSHA reports that many warehouse injuries stem from poor storage practices - an optimized putaway process helps proactively mitigate these risks.
Scalable Operations for Peak Demand
With system-driven putaway rules, it's easier to onboard temp workers or ramp up volumes during peak seasons without chaos. Barcode scanning, location-based putaway rules, and dynamic slotting make it easier to absorb volume spikes without overwhelming the floor team.
Different Types of Putaway Processes in Warehouse
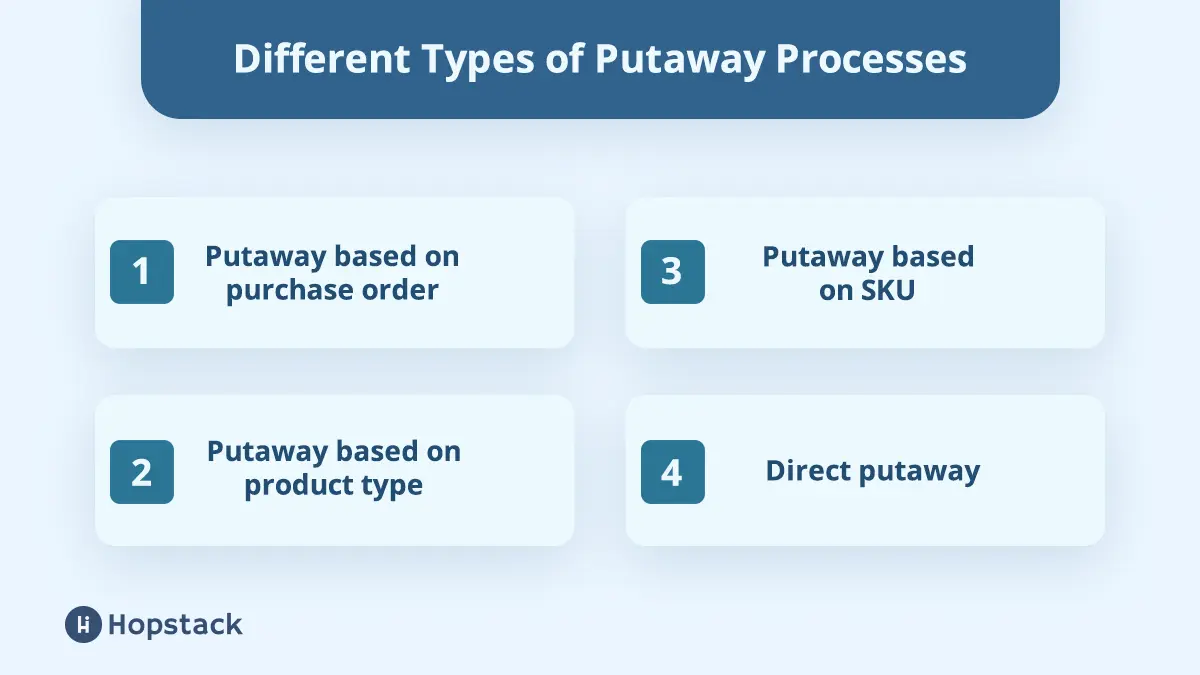
There are several different kinds of putaway processes based on the product, purchase order, SKU of the product, and more.
Putaway Based on Purchase Order
In this putaway process, similar items from different vendors are grouped together and put away in one trip. This makes it easier to pick that particular product as every stock is stored in the same place no matter where it came from. It is also helpful in weeding out any mistakes or damages as you’ll inspect every item to group them.
Putaway Based on Product Type
Putting away products based on what they are, helps in maximizing warehouse storage space utilization. This technique saves a lot of time as items of the same type can be grouped together, making it easier for pickers as they can go to where products of similar types are kept even if they don’t know where the exact product might be kept.
Putaway Based on SKU
For warehouses that store large quantities of products having the same SKU, putting them away based on their SKUs can be an efficient option. Storing products based on their manufacturer, brand, size, color, and other characteristics make them easier to find.
Direct Putaway
Direct putaway requires the least amount of handling of products. Instead of sorting through each item, in direct putaway, you can store the entire batch in a specified location. For instance, if the order is for one single customer, putting it away as it makes more sense than segregating each individual product and storing them in their designated areas.
How to Optimize the Putaway Process in a Warehouse
Every warehouse follows a putaway process in its own sense but without proper optimization, they won’t be able to achieve the best results. Incorporating a Warehouse Management System can help them in optimizing their warehouse putaway process and get the most out of it. Here is how WMS can optimize the putaway process for maximum operational efficiency.
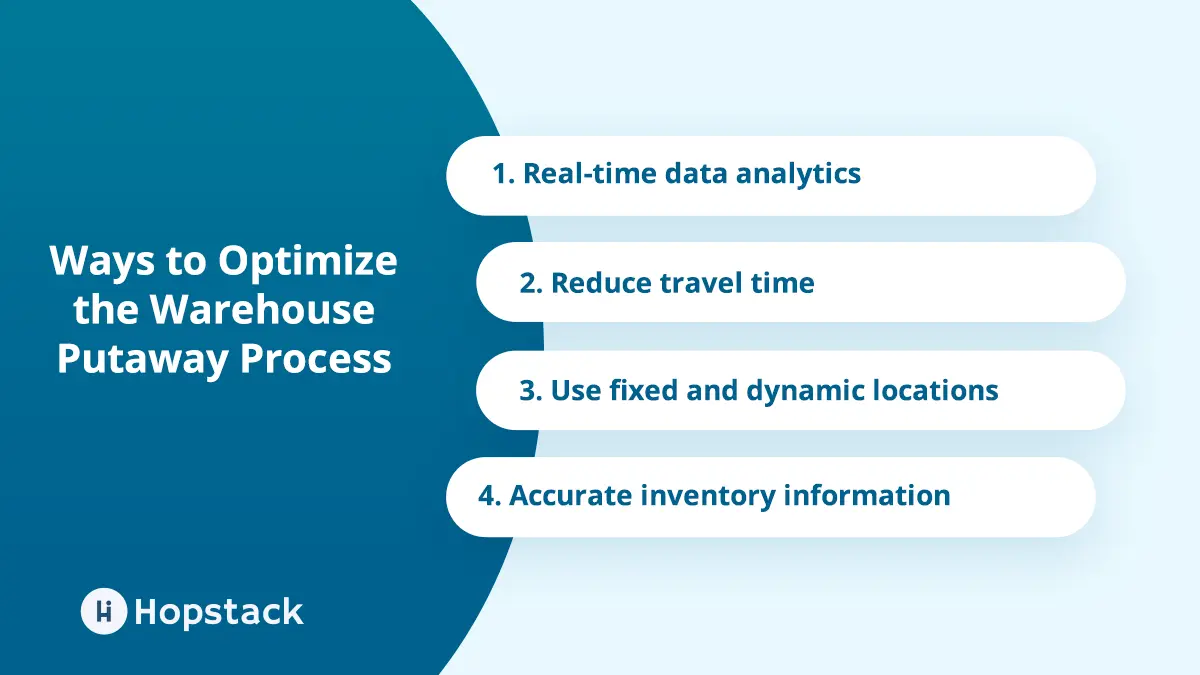
Real-Time Data Analytics
Over 70% of warehouse managers have expressed their concern for not having enough data at the right time. Data about shipping frequency, cargo size, cargo type, order volume, storage availability, and more help in implementing an optimal warehouse putaway process. A WMS system can automate data collection and analyze it to suggest the best place to store a product based on different criteria.
Reduce Travel Time
The more time a picker spends searching for products, the fewer orders it can fulfill every day. In fact, estimates reveal that warehouse associates spend about 75% of their time traveling and searching for different products. With the help of an integrated WMS system, the traveling time taken to fulfill an order can be reduced. The warehouse layout can be optimized to place fast-moving products together allowing pickers to pick the items in the shortest time possible.
Use Fixed and Dynamic Locations
Using a mixture of fixed and dynamic storage can improve warehouse productivity. Employees will start remembering the location of products in fixed storage while a WMS system can help make the storage a bit versatile by placing items in the first available, temporary location. Dynamic locations could serve as a competitive advantage during peak seasons when the buying activity for certain products is high and order lead times are expected to be minimal.
Accurate Inventory Information
A WMS system provides real-time visibility on the number of stock available for a product and where it is stored. This information comes in very handy when you have to order a new batch of products and want to see the stock levels of existing products. It is also beneficial when you are receiving a new batch of products and don’t know where similar products are stored.
Implement zone putaway
Divide the warehouse into distinct zones and assign specialized teams for putaway tasks within each zone. This targeted approach enhances efficiency as teams become experts in their designated areas.
Intelligent slotting
Intelligent slotting, a fundamental warehouse management component, involves strategically placing items to optimize the putaway process. Businesses can enhance efficiency by analyzing product characteristics and demand patterns by ensuring that high-demand products are easily accessible. This proactive approach streamlines the workflow and minimizes the risk of back-orders and stockouts, improving overall customer satisfaction.
Factors Affecting the Warehouse Putaway Process
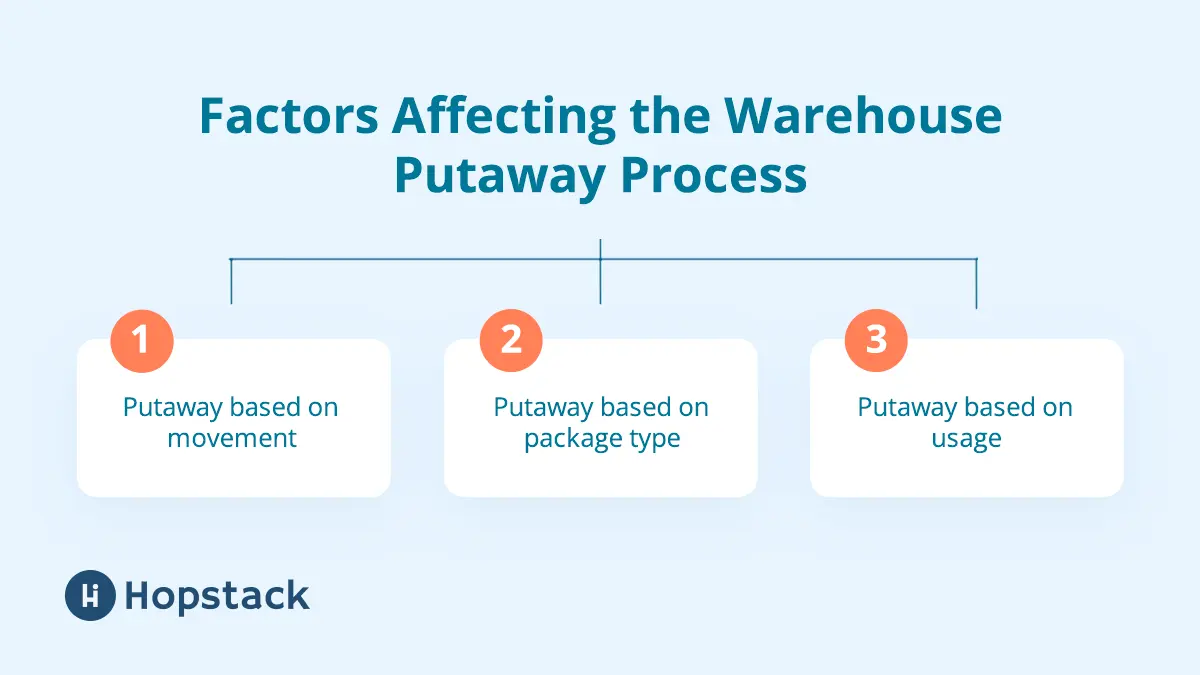
Three major factors to consider while choosing a putaway method:
Putaway Based on Movement
Using ABC analysis to store products based on their movement can reduce order fulfillment times drastically. Fast-moving products are termed as “A” category and are advised to be kept near the staging area and at a suitable height so that they can be picked and ready to ship in an instant. Similarly, slow-moving products can be termed as the “C” category and placed at the back of the warehouse.
Putaway Based on Package Type
In this method, products can be stored on their package type. For instance, individual products and pallets can be stored in different locations no matter what product they are. Similarly, packages can be distinguished based on their weight, shipment type, storage requirements, and more.
Putaway Based on Usage
There are products that are often brought together like gas stoves and utensils. Storing these products together based on their usage and why it’s being moved also helps employees in simplifying the putaway process.
.png)
Warehouse putaway KPIs & Their Importance
Putaway Accuracy Rate
The putaway accuracy rate is a crucial KPI that measures the precision of placing items in their designated storage locations. This percentage is derived from the ratio of accurate putaways to the total number of putaways, providing insights into the effectiveness of the warehouse organization. Maintaining a high accuracy rate ensures that products are stored in the right places, minimizing picking errors and enhancing the overall accuracy of order fulfillment processes.
Putaway Cycle Time
Putaway cycle time evaluates the efficiency of the putaway process by measuring the time it takes from receiving a product to placing it in its designated storage location. This KPI helps warehouse managers identify bottlenecks and streamline operations for faster throughput. A shorter putaway cycle time improves overall warehouse efficiency and contributes to quicker product availability for customer orders.
Utilization of Storage Space
The utilization of storage space assesses how effectively the available storage space is being used. By calculating the percentage of occupied storage space relative to the total available space, this KPI aids in optimizing the layout and organization of the warehouse.
Putaway cost per Unit
Putaway cost per unit evaluates the cost efficiency of the putaway process. Calculated by dividing the total putaway costs by the number of units put away, this metric provides insights into the economic aspects of the warehouse operation. Monitoring and reducing the cost per unit can lead to cost savings and improved profitability, making the warehouse operation more financially sustainable.
Putaway Productivity
Putaway productivity measures the efficiency of the workforce during the putaway process. It is calculated by determining the number of units put away per hour or per labor hour. This KPI helps in workforce planning, resource allocation, and performance management. Improving putaway productivity contributes to overall operational efficiency, ensuring that goods are placed in storage swiftly and accurately.
Inventory Accuracy
Inventory accuracy assesses the alignment between physical inventory and recorded inventory. By calculating the percentage of accurate inventory counts, this metric ensures that the warehouse maintains reliable and precise inventory records. High inventory accuracy is essential for preventing discrepancies, avoiding stockouts, and enhancing the overall reliability of the supply chain.
Putaway Turnover
Putaway turnover reflects the frequency at which items are put away and retrieved from storage. Calculated by considering the number of items put away and retrieved relative to the total number of items in storage, this KPI provides insights into the dynamism of the warehouse operation. A higher putaway turnover indicates efficient storage practices and helps optimize inventory management strategies.
Backorder Rate
The backorder rate measures the percentage of items that cannot be put away immediately due to various constraints, such as space limitations. By calculating the ratio of back-ordered items to the total number of items to be put away, this metric provides insights into the efficiency of the putaway process and potential challenges in space management. Minimizing the backorder rate is crucial for maintaining smooth operations and ensuring the timely availability of products for customer orders.
Takeaway
While Picking, Packing, and Shipping are important aspects of the warehouse, the putaway process is crucial as well. However, it is still one of the most overlooked aspects of the warehouse. Companies that don’t follow an optimized warehouse putaway process can experience diminished productivity, product losses, inefficient inventory management, and more.
In today’s fast-paced and ever-changing consumption landscape, warehouses and fulfillment centers cannot afford to be complacent in their approach and let process inefficiencies hamper productivity and thus the customer experience. There is an increased need for continuous visibility and data-driven business recommendations to make all fulfillment processes error-free.
Learn more about how Hopstack’s digital warehouse platform helps in improving the putaway process by analyzing historical data on demand patterns, inventory turnover, replenishment, product characteristics, and providing recommendations for SKU location before the shipment arrives to make the process seamless.
FAQs
How can I design a putaway strategy that handles both case and each-pick inventory?
To handle mixed units, you need slotting rules that separate full cases from each-pick items based on volume, order frequency, and zone type. A good WMS should assign high-velocity each-picks near pick/pack stations and store bulk items in reserve or pallet zones. This split ensures faster access and efficient space usage.
Which KPIs should I track to measure putaway performance?
Key metrics include putaway accuracy rate, cycle time per item, cost per line, productivity (units or lines per hour), and labor & equipment utilization. Monitoring these helps pinpoint inefficiencies
What are best practices for reducing putaway errors and costs?
Best practices include using directed/dynamic putaway via WMS, zone-based storage, staged/direct pick flows, serial/bin-level tracking, real-time alerts, and periodic audits to maintain accuracy & control costs
How do dynamic and directed putaway strategies work, and which is best?
Dynamic (or random) putaway uses your WMS to assign the next available slot, maximizing flexibility and space utilization. Directed putaway leverages rules—based on item velocity, weight, or category—to place goods in optimal, predetermined zones. Many warehouses use a hybrid approach: dynamic for overflow and directed for high-demand SKUs
What technologies help improve putaway accuracy and capacity tracking?
Tools like barcode scanners, RFID systems, integrated scales/dimensioners, and advanced WMS tracking enable automated data capture and real-time slot monitoring. RFID, in particular, reduces human error by automatically recording putaway actions and bin usage
What’s the best way to manage putaway during seasonal inventory surges?
During peak seasons, implement temporary buffer zones near receiving docks and prioritize putaway by SKU velocity. Use system-directed putaway to avoid congestion and configure overflow rules to maximize vertical storage. Forecasting inbound volume also helps you pre-allocate labor and space effectively.
How do putaway rules change for cold storage or multi-temperature warehouses?
Putaway in temperature-controlled environments must follow strict zone assignments based on product sensitivity. Your WMS should support item-level attributes like temperature range and expiry date, and route items accordingly. Delays or misplacement in these zones can lead to compliance or spoilage issues.