While a warehouse is generally considered the 'middleman' between manufacturers and customers, it holds greater relevance than most people think if the warehouse workflow efficiency can be improved.
With increased e-commerce platforms and customer demands for prompt product delivery, warehouses are proving effective at fulfilling those demands.
Warehouse IoT operations consist of many moving parts and functions working in tandem to ensure the correct product is received from the manufacturer, stored in the prescribed manner, and then delivered to the customer as per their requirements.
Every warehouse workflow must work smoothly to identify bottlenecks and improve productivity.
6 Primary Warehouse Processes
The six key warehouse processes are receiving, putaway, storage, picking, packaging, and shipping. You Warehouse managers can streamline these warehouse processes, lower costs, and mistakes, and increase the percentage of perfect orders by optimizing these six processes.
1. Receiving
The first and most essential warehouse workflow operation is receiving. The warehouse must confirm that it has received the right product in the proper amount, in the appropriate state, and at the correct time to properly carry out the warehouse receiving process. Failure to do so will have adverse effects on all procedures that follow.
Transferring ownership of the products to the warehouse is another aspect of receiving. As a result, the warehouse is responsible for keeping the goods in excellent condition until they are shipped. Warehouse associates can filter out damaged products and escape responsibility by properly receiving cargo.
2. Putaway
The second warehouse workflow procedure, putaway warehouse, involves moving merchandise from the receiving dock to the best warehouse storage location. The productivity of a warehouse business can be hampered by failing to place goods in their most advantageous location. There are several advantages to correctly storing goods, including:
- Faster and more effective cargo storage
- Less time is spent traveling.
- Product and staff safety is guaranteed
- The use of the warehouse area is maximized
- Finding, tracking, and retrieving cargo is more straightforward and quicker.
3. Storage
In a warehouse, storage is the procedure by which items are put in the best storage location for them. When carried out correctly, the storage procedure completely utilizes the available space in the warehouse and improves labor productivity.
4. Picking
To fill customer orders, picking is the warehouse workflow procedure that gathers products in a warehouse. As the most expensive process in the warehouse, accounting for up to 55% of all running costs, optimizing this process will significantly lower costs and boost warehouse productivity.
Since errors can negatively affect your customers' happiness, streamlining this process should also concentrate on achieving higher accuracy.
5. Packing
The warehouse process known as packing gathers selected items into a sales order and gets them ready to send to the customer. Ensuring that there is as minor damage as possible before the things depart the warehouse is one of the main tasks of packing. Additionally, packaging in warehouse needs to be minimal and light enough to control expenses while preventing the goods from becoming heavier.
6. Shipping
Shipping is the first step in moving goods from the warehouse to the consumer. Shipping is deemed effective only when the proper order is sorted and loaded, sent to the appropriate recipient, transported via the right means of transportation, and delivered promptly and safely.
Need for Improving Warehouse Efficiency
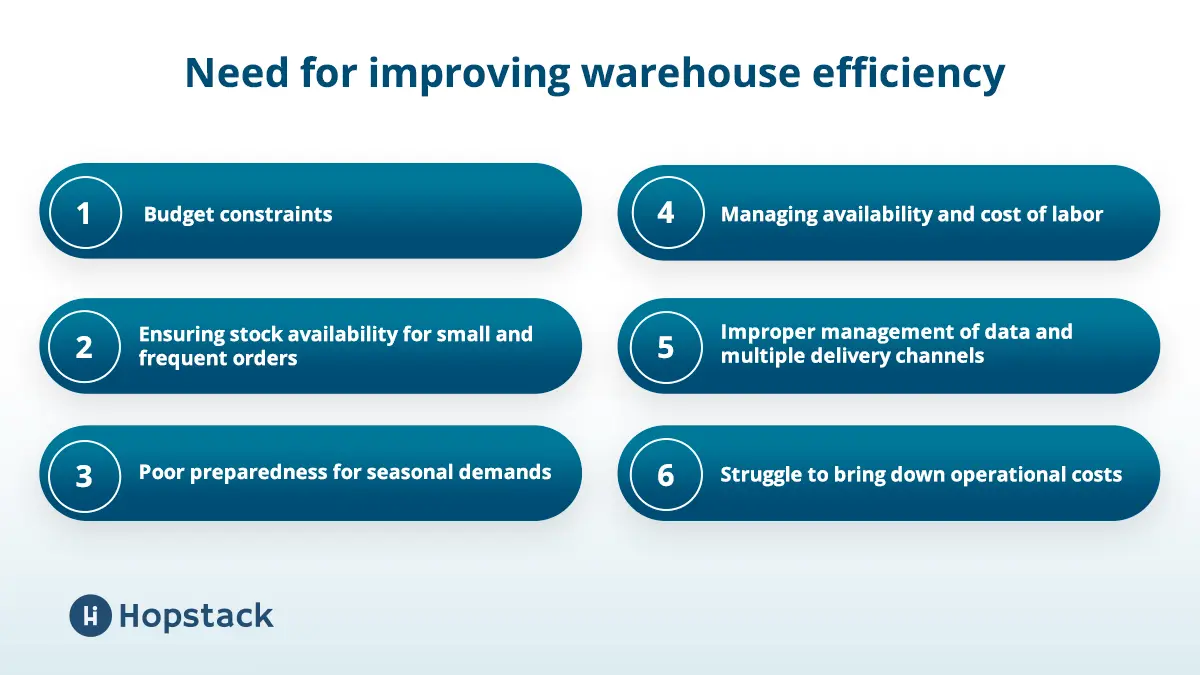
Managing a warehouse can be a demanding job. Small- and medium-sized warehouse managers face many challenges in optimizing warehouse workflow efficiency and increasing revenue. They constantly grapple with the following warehouse challenges:
Budget constraints
Small and medium business owners don't have the luxury of a vast budget and must constantly stay within budget constraints to increase warehouse workflow efficiency.
Ensuring stock availability for small and frequent orders
E-commerce is proliferating, and warehouses must quickly adapt to fulfill smaller multi-line orders at a higher frequency. Lead times also need to be shortened to speed up the delivery of products to the customer.
Poor preparedness for seasonal demands
Demand during the holiday season can skyrocket, requiring warehouses to stay prepared early for enhanced warehouse workflow efficiency. An increase in pressure can lead to errors and misplacement of products which also need to be checked.
Managing availability and cost of labor
Availability of labor is a very fluctuating issue. The ongoing pandemic has added to the challenges in workforce availability. Managers need to be prepared for labor strikes, illness or injury to people in the workforce, hiring new candidates, cost of labor, and much more to improve warehouse workflow efficiency.
Improper management of data and multiple delivery channels
Managing data about every single inventory movement can be challenging if done manually. It gives rise to erroneous records, lost data, or inaccurate inventory statistics across multiple delivery channels that hamper warehouse workflow efficiency.
Struggle to bring down operational costs
Warehouse managers have to devise ways to cut operational spending and not break the bank. While complying with monetary restrictions, managers must also focus on improving warehouse workflow efficiency and customer satisfaction.
How To Improve Warehouse Workflow Efficiency?
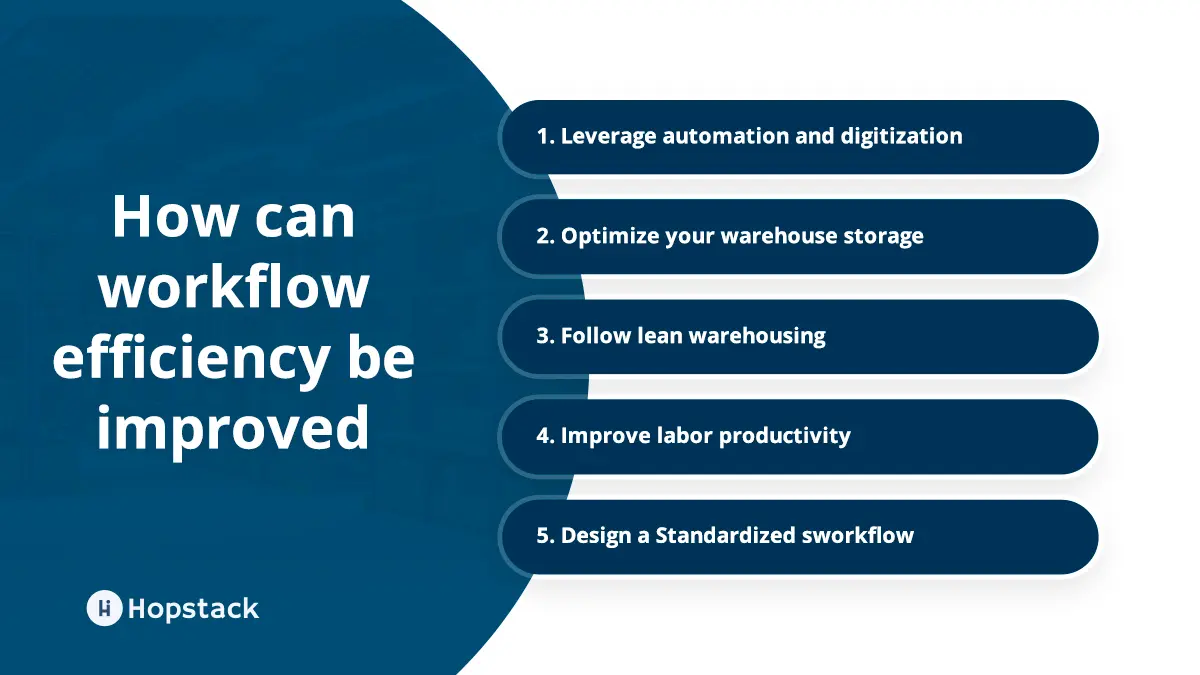
Leverage Automation and digitization
Warehouse operations still involve a lot of manual processes that are liable to delays and errors. Employees spend most of their time locating, picking up items, and moving back and forth to the entire warehouse to improve warehouse efficiency.
Intense manual efforts can lead to miscalculations, wrong pickup, inaccurate inventory count, and sub-optimal picking rates.
Implementing advanced Warehouse management workflow and orchestration software can establish a standard workflow for employees to follow throughout the order fulfillment cycle and improve warehouse efficiency.
It can capture product data in real time, creating an optimized path for pickers to follow and complete the order in the shortest time possible.
Solutions (like Hopstack) combine advanced analytics and Order picking automation to improve efficiency They provide accurate insight on picking, packing, shipping, and inventory count for streamlining goods and parcel movement, significantly reducing errors arising from manual processes.
Read Also - Digital Transformation of the Warehouse
Optimize your Warehouse Storage
How a warehouse stores its inventory and manages the available storage space is crucial to improve warehouse efficiency.
Disorganized shelves, cluttered employee workstations, and improper use of vertical space can cause picking delays, misplace items or provide an inaccurate inventory count.
Optimizing warehouse storage lets you store more inventory without expanding the square footage.
Labeling packages properly, segregating stocks based on different parameters, using taller storage systems, additional shelves for other sized materials, standardized bins for keeping shelves tidy, color-coding pallets, analyzing material usage patterns, and more can make product picking as seamless and error-free as possible that will improve warehouse efficiency.
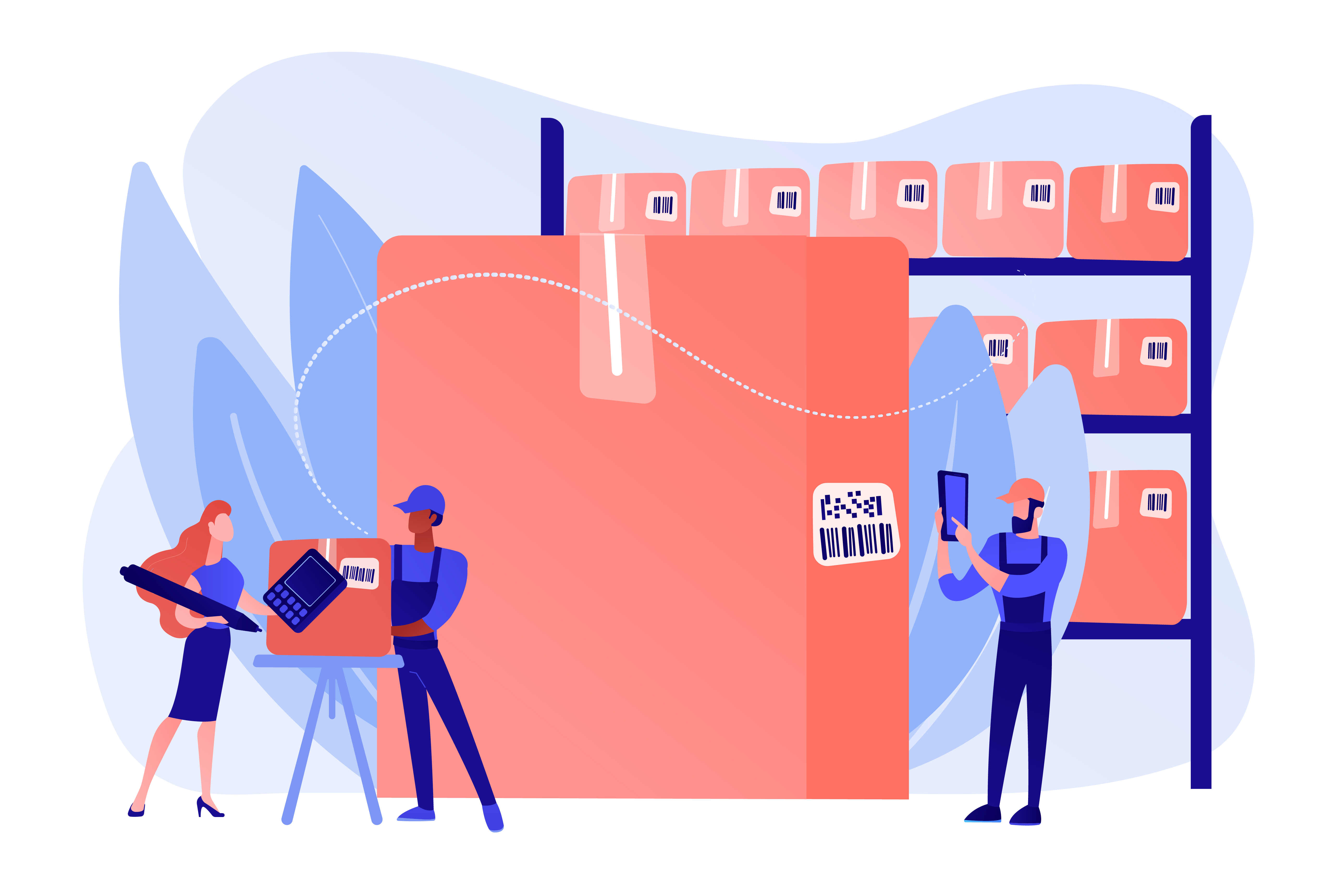
Follow Lean Warehousing
While stock-piling something that is in huge demand can be profitable in the short run, customer needs and preferences keep on changing. Warehouses should practice the idea of "lean" inventory to prevent stocks from expiring or going to waste to improve warehouse efficiency.
Lean inventory suggests warehouses use only what they require and nothing more. Adopting this method prevents warehouses from ordering more inventory than needed and helps improve warehouse efficiency and eliminate waste as small quantities are dispatched from the supplier at frequent intervals rather than sending multiple shipments once.
Through lean principles, warehouse operators focus on continuous process improvement to improve workflow efficiency, prevent stock-piling, better utilize storage space and streamline processes to help customers get products faster.
As a result, customers should opt for software that can leverage AI to help them with inventory optimization by dynamically maintaining safety stock levels, reordering thresholds, and demand forecasts that improve warehouse efficiency.
Improve Labor Productivity
Although technology is used extensively in the modern warehouse, labor still makes up for the largest share of warehouse operating costs. Improving labor productivity is fundamental to improving the workflow efficiency of a warehouse.
A robust warehouse operating system makes labor management easier for warehouse operators. They can set up training routines for new joiners or create a cross-training plan for workers to learn different tasks beyond their domains.
Not only does this improve the competency of workers, but it can come in handy when a specialized worker cannot come to work.
Encouraging workers to share what they think can reduce costs in a warehouse and work on their pain points can also prove constructive, as they are responsible for most warehouse processes.
Design a Standardized Workflow
Without a standard automated workflow in place, employees end up working at their own pace and comfort. Different working habits can create gaps in warehouse processes, making it difficult to measure individual performance against set benchmarks.
Establishing a standardized workflow ensures that every employee works within the same guidelines and that there is transparency about package movement, order fulfillment, and other processes.
Following a streamlined and well-defined process helps identify issues and bottlenecks hampering the warehouse's efficient automated workflow.
Conclusion
Implementing the best approaches to ensure smooth and efficient warehouse operations is fundamental to cutting down on costs, enhancing the productivity of the warehouse, and increasing ROI.
Leveraging smart warehouse execution and warehouse optimization software can help improve the efficiency of automated workflows and get the most out of your warehouse.
Interested in learning more about how to improve the workflow efficiency of your warehouse?
Explore Hopstack's AI-powered warehouse execution software that easily integrates with your existing hardware infrastructure, ERP, and WMS systems to automate and optimize various operations inside the warehouse facility.