The warehouse receiving process is the first step of the customer fulfillment journey, and as such, has a significant impact on overall inbound activity and warehouse operations. An efficient receiving process directly sets the foundation for efficient inventory management, optimal storage space utilization, and seamless order fulfillment. Suboptimal warehouse receiving can lead to stock control issues, strained supplier relationships, and higher operating expenses, especially for SMEs looking to extract maximum value from their order fulfillment processes.
Hardware integration with WMS automation can enhance the receiving process by streamlining workflows, improving accuracy, and increasing efficiency. Real-time data access and improved visibility into warehouse performance can deliver the insights necessary to build an efficient and robust receiving process that supports overall operational excellence.
In this article, we will explain how hardware integration with a WMS can maximize productivity and efficiency in the receiving process.
How Does Hardware Integration With WMS Improve the Receiving Process?
In essence, hardware integration involves connecting the warehouse management system (WMS) to the warehouse devices and hardware available like barcode scanners, RFID readers, mobile computers, and IoT sensors. A streamlined flow of data to and from the hardware devices and WMS allows them to work together to optimize the receiving process, reduce receiving errors, improve dock-to-stock time, and boost receiving efficiency.
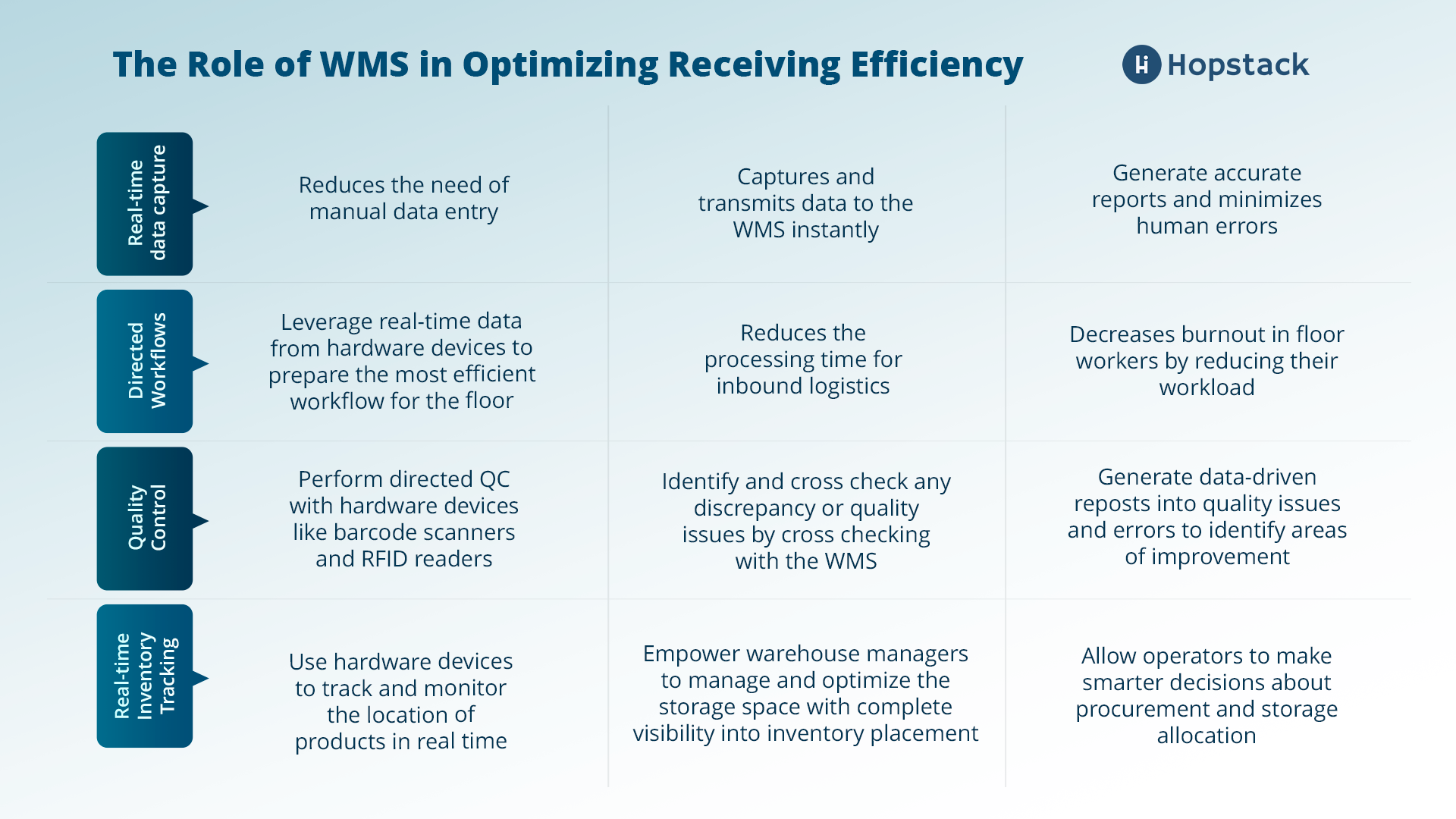
Warehouse automation does not work in a vacuum; hardware devices and WMS have to be in sync to deliver the best business outcomes for your organization. Integration does not just unify the hardware with the software, it integrates inbound and outbound processes and business strategies for optimal time to market.
There are several advantages to integrating warehouse hardware devices and WMS:
- Improved inventory management and data capture: Real-time data capture with RFID readers and barcode scanners ensures the right products are recorded and accounted for in the inventory records. A high-performing receiving process empowers warehouse managers to optimize inventory planning and management, resulting in fewer instances of overstocking or stockouts.
Automated data capture and interchange also allow for stricter quality control, ensuring the quality and accuracy of incoming products. According to a survey by Wakefield, wrong product packaging and delivery errors are the primary cause of 17% of inventory mistakes, leading to lost customers. - Timely order fulfillment: An efficient warehouse receiving process positively impacts other downstream operations, resulting in an overall robust and consistent order fulfillment procedure. Faster order processing means healthier timelines for picking, packing, and shipping, leading to fewer mistakes and rapid order fulfillment. Faster, consistent, and accurate deliveries are key to satisfying customer promises.
- Data-driven decision-making: Warehouse hardware is a wealth of data, and integration with WMS provides the insights necessary to make data-driven business decisions. Through real-time data capture and transmission, warehouse managers can monitor KPIs, such as error rates, labor productivity, processing times, and more.
A WMS can also analyze available data to forecast demand and evaluate vendor performance based on timely deliveries, product packaging, and the percentage of damaged products. - Reduced manual labor and human errors: With continuous access to streaming data from the hardware devices, a WMS can automate several manual tasks like scanning items, data validation, printing labels, and data entry. Following standardized processes and automation can reduce human errors to a large extent, resulting in a smoother warehouse receiving process.
A WMS can also leverage the data captured to prepare intelligent workflows for the floor workers, leading to smarter and faster warehousing tasks. With directed input on stocking, storing, and receiving decisions, the margin for errors is much higher. - Accelerated movement of products: A warehouse management system greatly reduces the time it takes to process and move inbound products across the warehouse receiving process. It improves the dock-to-stock time by using automation and workflows to accelerate the movement of products from the warehouse dock to the designated storage locations. Enhanced visibility allows users to track storage space and automatically trigger put-away tasks while directed put-away workflows ensure that the products are stocked as quickly as possible.
Depending on the level of integration, warehouse managers can even access cross-docking strategies where inbound products are directly moved to the packing area for outbound fulfillment without needing to be stored at all.
Tailoring Your Receiving Strategies for Different Verticals and Types of Shipments
The Logistics Management reports that 85% of warehouse operations use WMS. However, it’s important to remember that while warehouse management systems are equipped to deal with all kinds of products and inventory, you need to fine-tune your integration based on the unique requirements, regulations, and product types of your particular vertical for the best business outcome.
There are several factors you have to consider while optimizing your receiving process based on the industry type:
- Understand your product well: Based on your industry, the products will have different characteristics and will require the appropriate handling methods, equipment, and storage solutions. Even the physical dimensions, weight, fragility, or date restrictions will determine what kind of pallets, boxes, or cases to use and how to transport and store them for maximum efficiency.
- Ensure you have the right equipment: Leading from our previous point, receiving and storing specialized products requires the right equipment and tools for the job. For example, perishable goods like frozen foods, fresh meat, or fruits and vegetables will require appropriate refrigeration and temperature control while hazardous materials like dry ice or lithium batteries might require specialized containment and handling.
- Develop specialized quality control processes: Every vertical has different quality standards, regulations, and QC requirements. Familiarize yourself with the safety guidelines, standard quality parameters, and inspection and testing procedures to ensure there are no gaps within your receiving process that can negatively impact product quality and customer expectations.
Warehouse hardware integration with WMS can help develop sampling plans based on supplier performance, historical errors, product characteristics, or inherent risk. - Train and empower your warehouse workers: At the end of the day, your warehouse workers will be the ones interacting with the WMS in real time to execute the receiving process. They need to be trained in industry-specific compliance requirements, handling standards, and quality control. Trained and empowered workers who know how to handle specialized equipment and unique products significantly streamline the receiving process by smoothly executing directed workflows and instructions.
As you can see, most of the workflow is the same for the three industries, except for QC criteria, sorting and segregation practices, and stakeholder engagement.
Enhancing Receiving Metrics With Hardware and WMS Integration
There are five primary receiving warehouse metrics that can be significantly improved with WMS and hardware integration.
1. Dock-to-stock time
Real-time data capture and electronic data interchange using hardware devices like RFID readers and barcode scanners can greatly reduce the time between the arrival of any particular shipment in the dock and its safe storage in the designated warehouse area. In addition, a WMS uses streaming data to design efficient routes for warehouse workers and develop smart put-away workflows to streamline the picking process. One of Hopstack’s 3PL customers implemented barcode/RFID scanners and WMS and hardware integration to improve the dock-to-stock time by a staggering 71%.
2. Inventory accuracy
WMS integration with hardware devices automates various manual tasks like data entry, labeling, printing, scanning, and more. It can automatically check and validate inventory records based on data collected from barcode scanners and RFID readers.
In 2017, Honeywell Logistics Solutions integrated their WMS with Datahub to enable Traditional Chinese Medicines (TCM) to scale with increased demand. The increased visibility into the client’s distribution center network increased inventory accuracy by 99.9%.
3. Labor efficiency
Apart from reducing worker burnout and workload using automation, real-time guidance, and smart workflows, hardware integration with WMS also uses the captured data to optimize task prioritization decisions and resource utilization.
For example, Skechers built a new distribution center availing system integration between a WMS and an automated materials handling system with the intention to optimize the receiving and shipping processes. As a result, they were able to scale up their receiving process to handle 17,000 pairs of shoes per hour compared to the previous range of 7,000 shoes per hour.
4. Space utilization
Warehouse hardware integration with WMS is essential to optimize the available storage space inside any particular warehouse. It considerably improves the storage space utilization rate by recommending storage locations based on product dimensions, weight, and storage requirements. More efficient use of three-dimensional space within storage areas allows for better cube utilization and yield per warehouse square foot. According to a study by Zebra, 59% of respondents anticipate capacity utilization to become a top challenge going forward.
With WMS integration, warehouse managers can track the reception, movement, and storage of inventory in real time. This increased visibility into available storage space can then be used to optimize storage decisions and improve put-away efficiency, allowing the workers to smartly manage both space and orders for higher inventory turnover rates.
5. Dwell time
With real-time data capture, it’s possible to cut down on the dwell time between when a shipment arrives at the warehouse and when it’s processed. With emerging technologies like Automated Storage and Retrieval Systems (AS/RS) and Automated Guided Vehicles (AGVs), it’s possible to automate significant portions of the receiving and put-away processes, leading to lower dwell time overall. According to ARC Research, approximately 60% of respondents expect to invest in automated storage and retrieval systems like conveyors in the coming years.
Best Practices To Integrate WMS and Hardware Devices in the Receiving Process
There are a few best practices that are applicable across industries when you’re looking to integrate WMS and hardware devices for a high-performing receiving process.
1. Always keep your business requirements in mind
Integrating a WMS with hardware devices is already an extensive task, especially for organizations operating multiple warehouses. Make a list of operational challenges, low-performing areas, and pain points within the receiving process to guide your integration decisions. Your choice of a system integrator or WMS should be able to scale along with your business’s growth in the future.
2. Train your staff when introducing new technology
Sometimes, there’s a lot of initial pushback from the warehouse workers when introducing new technology into the warehouse. It’s important to communicate that the integration of WMS with hardware devices is to empower the staff and not replace them at any point; it’s a means to make warehousing operations leaner and smarter in the long run. An overwhelming 73% of respondents of the Zebra Warehousing Vision study believe human interaction to be essential to balance in warehousing operations.
Provide hands-on training to the warehouse managers and workers with a combination of training materials like user manuals, videos, online resources, and 1:1 sessions to address everyone’s needs. Employ a feedback loop to improve the training process and design refresher courses.
3. Cultivate a proactive approach to identifying and remedying challenges
Like with any integration project, there’s a lot that can go wrong when integrating warehouse hardware with a WMS. Perform a thorough risk assessment to identify potential compatibility issues, compliance failures, hardware malfunctions, or regulatory requirements that can disrupt the integration process. Create contingency plans and prepare backups to prevent disrupting the receiving process. Continuously review and improve your technology stack and processes to ensure alignment with business goals.
Next Steps
Integrating hardware devices with a warehouse management system is not an easy task, but if implemented correctly can give massive dividends towards improving warehouse receiving efficiency. Greater visibility in receiving processes improves the entire order fulfillment pipeline in general, leading to a much more robust and productive warehousing operation.
Having a WMS and hardware devices work in isolation is no longer enough to meet today’s growing consumer demands. However, when unified, they have the potential to supercharge your receiving process in a significant way.
We hope our guide will help you understand the advantages of integrating a WMS with hardware devices while allowing you to circumvent any possible pitfalls you might face along the way.