Warehouses aren’t what they used to be—and that’s a good thing. The days of clipboards, guesswork, and endless manual picking are quickly fading. In their place? Smart warehouses that can sense, think, and respond in real time.
This isn’t just about throwing robots on the floor or installing some sensors. A smart warehouse uses AI, robotics, and IoT to tie everything together—from inventory movement to labor allocation—to run operations faster, leaner, and with fewer mistakes to improve productivity and warehouse efficiency.
What makes this shift powerful isn’t just the tech itself, but what it unlocks:
- Teams can spend less time chasing errors and more time solving real problems.
- Returns drop. Shipments go out faster. Customers stay happier.
- And your operation gains visibility where it matters most—in the flow of goods, data, and decisions.
In this guide, we’ll break down how smart warehouses actually work, what tech stacks are worth your attention, and how leading teams are using automation to do more with less.
What is a Smart Warehouse?
A smart warehouse is one that leverages automated systems and digital technologies to streamline operations from end to end. This includes both advanced software and physical warehouse automation tools such as robotics, conveyors, and autonomous vehicles. Unlike traditional warehouses, smart warehouses are designed to optimize efficiency at every stage—powered by real-time data, machine learning, and intelligent decision-making.
Sensors and tracking technologies play a crucial role in these environments. They provide constant visibility into inventory movement, reducing the need for manual checks and minimizing errors. Warehouse management software complements this by optimizing layouts, improving task allocation, and accelerating order processing. The result is less time wasted on routine tasks and fewer mistakes that slow down fulfillment.
As businesses look for ways to reduce operating costs and scale faster, smart warehouses are quickly becoming the new standard. From automated conveyor systems to AI-driven robots, these technologies allow facilities to run warehouse operations around the clock with minimal human intervention. And with growing pressure in the eCommerce space to deliver faster and more accurately, smart warehousing is no longer a nice-to-have—it’s a strategic advantage for companies aiming to future-proof their operations.
Top 6 Smart Warehouse Technologies & Their Implementation
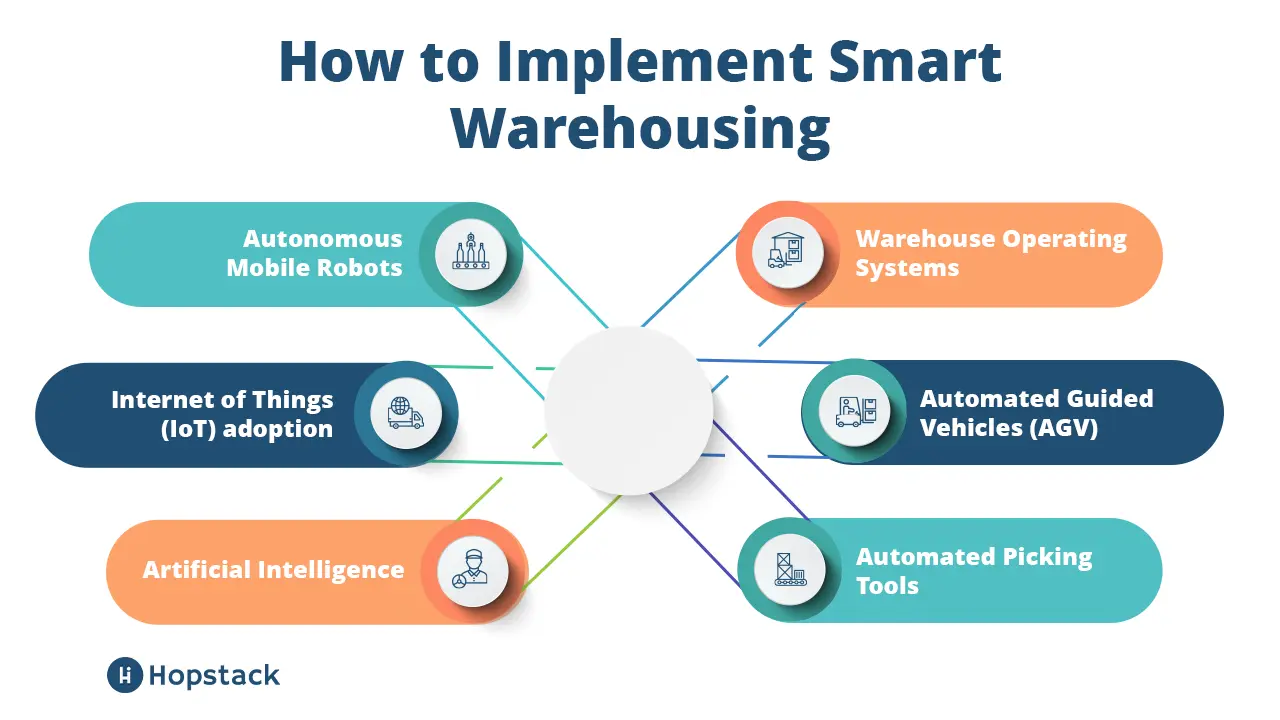
Smart warehouses rely heavily on the latest smart warehouse technologies that make smart warehouse operations optimized and smarter. Smart warehousing entails a broad spectrum, from enabling paper-free operations to installing autonomous robots.
Below is the list of 6 must-have smart warehouse technologies that have a huge impact on warehouse automation and also how you can implement them on in your warehouse.
1. Autonomous Mobile Robots
These advanced machines can execute several tasks ranging from automated picking in warehouse and storage to packaging, inventory distribution, and more.
They are intended to work in tandem with the floor associates to ensure a seamless, optimal, and error-free goods movement flow. Also, the most current robotic systems in smart warehouse technology are called cobots, and they are intended to work alongside warehouse staff.
Cobots are easy to program, fast to set up, flexible, and safe to use within the warehouse. To prevent damage, the cobot can be taught how to grasp an object or how quickly to move something by the human operator.
2. Internet of Things (IoT)
IoT is getting increasingly popular in the smart warehouses space. Smart IoT devices range from picking devices, sensors, and robots to ASRS systems communicating operational data in real time to the central warehouse system.
Such granular real-time data becomes a valuable input source for machine learning algorithms to learn and optimize recommendations.
Whether manual or automated, the IoT system synchronizes all data in an accessible network, helping to improve labor planning, customer experience, and inventory control with a double impact if coupled with an automated inventory control platform.
3. Artificial Intelligence (AI) in Warehousing
Analyzing a large amount of data accumulated during smart warehouse operations can be vital to optimizing various processes. The AI-driven approach can assist with predicting Inventory demands, optimizing picker routes, enabling dynamic task allocation, and handshakes on the floor.
Using Artificial Intelligence will reduce labor costs for the entire warehouse compared to the traditional warehouse. AI as a smart warehouse technology can refine the inventory forecasting, optimization, and management process seamlessly.
4. Warehouse Management Systems
A modern warehouse software or warehouse management system with advanced features and futuristic innovation can act as a central operating system to manage warehouse operations and workflow in real-time endlessly.
Moreover, the automation systems can act as a bridge between the warehouse technology hardware like sensors, robots, etc. with softwares like ERPs, WMS, Inventory management system and shipping software.
Beyond these features, the warehouse management system must have advanced analytics for predictive metrics and innovative depth to make useful and valuable recommendations.
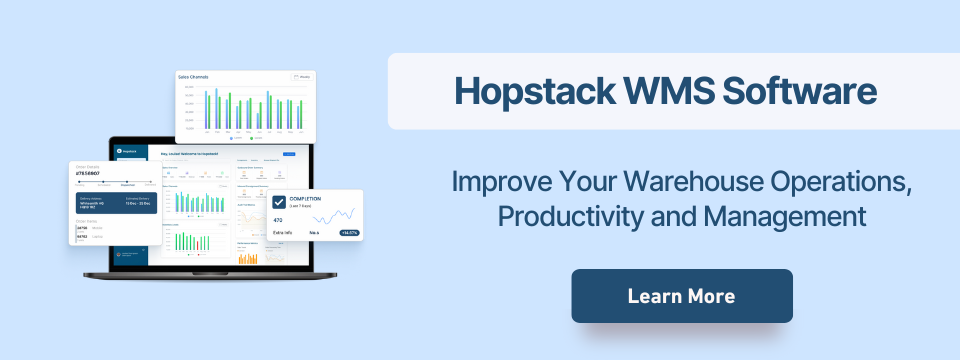
5. Automated Guided Vehicles (AGV)
AGVs can maximize warehouse space while minimizing the need for new fulfillment and distribution facilities to be built.
Some examples of automated guided vehicles (AGVs) are pallet carts and forklifts that are self-guided and follow digital paths within the warehouse as they load and unload containers, boxes and pallets.
AGVs handle hazardous circumstances more efficiently while reducing material damage and improving inventory accuracy.
6. Automated Picking Tools
Automated picking components in smart warehouse technology can help the warehouse achieve optimum picking rates. Within this grouping, there are numerous different tools (like voice automated picking and pick-to-light).
The WMS should be designed to accommodate these technologies for efficient smart warehouse operations. It enhances picking by accelerating it, optimizing labor allocation, and lowering human error.
Smart Warehouse Example: Transforming Fulfillment at a Mid-Sized 3PL
Imagine a mid-sized third-party logistics (3PL) provider that handles omnichannel fulfillment for multiple consumer brands—including electronics, skincare, and apparel. Prior to automation, their warehouse relied heavily on paper-based processes, RF scanners, and manual labor for everything from receiving to shipping. Inventory visibility was fragmented, errors were frequent, and picking speed was a constant bottleneck during sales surges.
To stay competitive, the 3PL transformed its facility into a smart warehouse. Here's what that looked like:
- Automated Receiving: Upon arrival, shipments are scanned using RFID gates that automatically log SKUs into the warehouse management system (WMS). Sensors validate quantities against the ASN and alert the receiving team of discrepancies in real time—eliminating manual data entry and reducing check-in time by 60%.
- AI-Driven Slotting: The system continuously analyzes order patterns and SKU velocity. High-frequency items are dynamically re-slotted closer to the packing stations, while slow movers are placed in higher racks. This reduced average pick paths by 35% and helped warehouse associates fulfill orders faster with less fatigue.
- Autonomous Mobile Robots (AMRs): AMRs transport totes between picking zones and packing stations. Workers stay in fixed zones while the robots handle movement—minimizing downtime and improving pick accuracy. During peak demand, the company can lease additional robots without adding headcount, thanks to a Robotics-as-a-Service (RaaS) model.
- Predictive Maintenance: The conveyor systems and picking arms are IoT-enabled, feeding performance data into the system. Based on usage cycles and sensor feedback, the WMS triggers maintenance alerts days before a component might fail—avoiding downtime and costly delays.
- Unified Control Tower: From a single dashboard, the operations team monitors warehouse activity, order progress, labor productivity, and SLA compliance. Alerts and exception reports are prioritized, allowing managers to address issues before they escalate. For example, if a replenishment delay threatens on-time fulfillment, the system flags it and recommends rerouting high-priority orders to another zone.
The result? The 3PL increased throughput by 40%, reduced fulfillment errors by 70%, and now offers guaranteed same-day shipping windows to its clients. The smart warehouse not only enhanced operational efficiency but also became a strategic differentiator in winning new contracts.
Top 6 Smart Warehouse Benefits
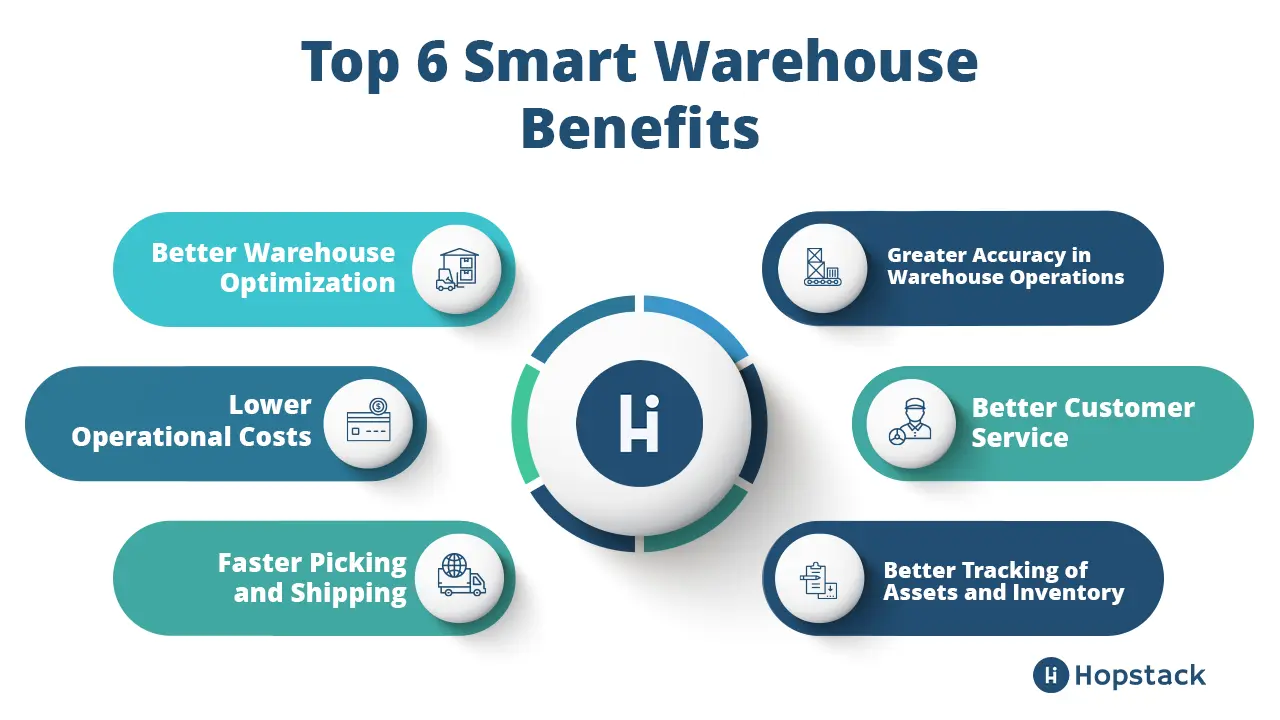
1. Dynamic labor reallocation
Smart warehouses help solve key warehouse challenges like uneven workload distribution and inefficient labor use. By analyzing task volume and equipment availability in real time, these systems automatically reassign human resources—from the receiving process in the warehouse to order fulfillment—based on current operational priorities.It reduces the need for micromanagement and allows supervisors to focus on exceptions rather than day-to-day task planning. Especially valuable in high-velocity environments where demand can shift hourly.
2. Serialized inventory tracking at multiple levels
Advanced serialization in smart warehouses enables tracking of goods not just at the item level, but also at nested levels—like pallets, cases, and individual units. This is crucial for industries dealing with high-value or regulated goods, such as medical devices, luxury goods, and electronics.
The system automatically maintains parent-child relationships between units, simplifying audits, recalls, and compliance while supporting detailed reporting for product provenance and lifecycle tracking. This enables more precise inventory management, streamlining stock audits, compliance, and replenishment across the supply chain
3. Condition-based monitoring and alerts
In smart warehouses, sensors do more than just track location—they also monitor critical environmental variables like temperature, humidity, and light exposure. This is essential for products with strict storage requirements such as vaccines, perishable goods, or fine wines.
When thresholds are breached, automated alerts are triggered so that corrective actions can be taken immediately—preventing spoilage, ensuring compliance, and reducing write-offs.
4. Predictive maintenance on automated systems
Smart warehouses use IoT-enabled devices that track operational parameters—motor vibration, temperature fluctuations, cycle counts, and energy use—across automation equipment like conveyors, lifts, and AMRs. Machine learning models then predict when components are likely to fail or degrade, allowing maintenance teams to proactively schedule service before unplanned downtime occurs. This not only reduces costly disruptions but also extends equipment lifespan and improves overall uptime.
5. Intelligent slotting and re-slotting
Smart slotting goes beyond traditional ABC analysis. By leveraging machine learning models that account for SKU velocity, historical order data, seasonality, and even order line combinations, smart warehouses continuously optimize where items are stored.
The system recommends re-slotting at regular intervals or dynamically during demand shifts—boosting pick efficiency, reducing congestion in pick zones, and accelerating fulfillment for fast-moving SKUs. Optimized slotting significantly boosts inventory management efficiency by minimizing travel distance and reducing delays during order fulfillment
6. Integrated robotics for last-touch automation
Autonomous Mobile Robots (AMRs) and collaborative robots (cobots) are increasingly used for repetitive tasks like tote transport, zone-to-zone movement, and pick-to-pack transitions. In a smart warehouse, these robots are fully integrated with the WMS and WES (Warehouse Execution System), enabling synchronized workflows that minimize hand-offs and reduce idle time. Robotics as a Service (RaaS) models also offer flexibility for scaling capacity during peak seasons without permanent CapEx investment.
7. Unified control tower visibility
A smart warehouse serves as a central nervous system by consolidating data from the WMS, automation stack, labor systems, and transportation management systems (TMS) into a single, actionable dashboard.
This control tower view allows managers to spot bottlenecks, monitor service-level commitments, and make rapid decisions across functions. It’s especially valuable for enterprises managing multiple facilities or 3PLs operating distributed networks.
8. Exception-based decision-making
Rather than flooding supervisors with operational noise, smart systems flag only the anomalies—missed picks, blocked zones, delayed replenishments, or low inventory alerts—so humans can focus on what matters. This shift from reactive firefighting to proactive management improves decision speed and quality while reducing stress on the warehouse floor.
Exception handling workflows can also be automated or semi-automated based on past resolutions, further speeding up issue resolution. This approach helps eliminate warehouse challenges like bottlenecks, missed picks, and delays—empowering staff to focus on resolving only what requires human judgment.
9. Integration with upstream and downstream systems
Modern smart warehouse platforms offer robust integration capabilities through APIs, EDI, and prebuilt connectors. This allows real-time synchronization with ERPs, supplier systems, eCommerce platforms, and even last-mile carriers. The result is tighter coordination across the supply chain—from faster ASN processing and replenishment triggers to automated order updates and delivery notifications.
It creates a frictionless data flow that supports better planning, forecasting, and execution across the business. For example, integration with supplier systems improves the receiving process in the warehouse by automating ASN matching, flagging damaged goods, and triggering real-time inventory updates that improve downstream order fulfillment speed.
Conclusion
Building smart warehouses is essential to stay competitive with the rapidly evolving consumer expectation and the disruptions caused by the current pandemic.
Forward-thinking businesses are catching up with the idea of smart warehousing, slowly but surely.
Several enterprises are substituting spreadsheets, legacy systems, and other rudimentary processes with some of the mentioned smart warehousing components.
Eager to know how you can make your warehouse smarter? Get in touch with us today!
FAQs
How does AI-driven inventory optimization work in a smart warehouse, and what impact does it have on operational costs?
AI analyzes data and demand patterns to optimize stock levels and storage. This reduces stockouts, minimizes space wastage, and lowers labor costs by automating restocking, improving overall warehouse efficiency and reducing operational expenses.
What are the most impactful technologies in a smart warehouse setup?
Core technologies include IoT sensors for real-time tracking, autonomous mobile robots (AMRs) for transport, AI-driven WMS for decision-making, and vision systems for quality checks. These systems work together to streamline operations and increase throughput.
How does predictive maintenance in a smart warehouse improve the lifespan and efficiency of robotic systems and automated equipment?
IoT sensors track robotic and equipment health, predicting failures before they happen. This proactive maintenance reduces downtime, extends equipment life, and ensures continuous, efficient warehouse operations.
How do machine learning models optimize slotting strategies in a dynamic warehouse environment?
Machine learning continuously analyzes sales, demand, and order data to adjust SKU placement. This reduces picking time, improves accuracy, and adapts in real time to evolving demand, optimizing warehouse layout and throughput
How does a smart warehouse handle exceptions like inventory mismatches or delays?
With real-time visibility, smart warehouses detect anomalies—like inventory discrepancies or stuck orders—immediately. Alerts, automated task reassignment, and workflow re-routing ensure minimal disruption, often resolving issues before they escalate.
Is it possible to implement smart warehouse capabilities in legacy buildings?
Yes, many smart tools can be added without rebuilding infrastructure. Mobile AMRs, cloud-based WMS platforms, and modular IoT systems can retrofit into existing layouts. The key is interoperability between systems and scalable architecture.
What cybersecurity risks should be considered in a smart warehouse?
Smart systems are connected and data-rich, making them vulnerable to breaches. Use secure cloud platforms, role-based access control, regular firmware updates, and network segmentation to reduce risks. Backup and recovery protocols are also essential.