WMS features are crucial in defining and choosing the best warehouse management system for fulfillment and warehousing. The ever-growing complexity in the business environment and consumer preferences has forced E-commerce, 3PL, manufacturing, distribution centers, and retail companies to become heavily reliant on advanced technology.
Such technology needs to ensure smoother supply chain and logistics operations right from procurement of inbound goods to delivering them in the order fulfillment step.
To keep up with the dynamic warehousing needs, fulfillment centers today need to be equipped with best-in-class Warehouse Management System (WMS) features. A modern WMS must provide a connected experience inside a warehouse as well as between multiple warehouses. A new-age WMS must also help warehouse workers retire manual and spreadsheet-based warehouse processes and automate every day recurring processes to enhance warehouse operations.
Here is a guide to the key advanced WMS features and capabilities that should be built into a modern WMS to drive excellent warehouse execution and efficient and accurate order fulfillment.
12 Best Features of Warehouse Management System
Here's the list of 12 best and modern features of warehouse management system that will help in solving modern fulfillment and warehousing challenges. The WMS features should be kept in mind while choosing the right warehouse management system.
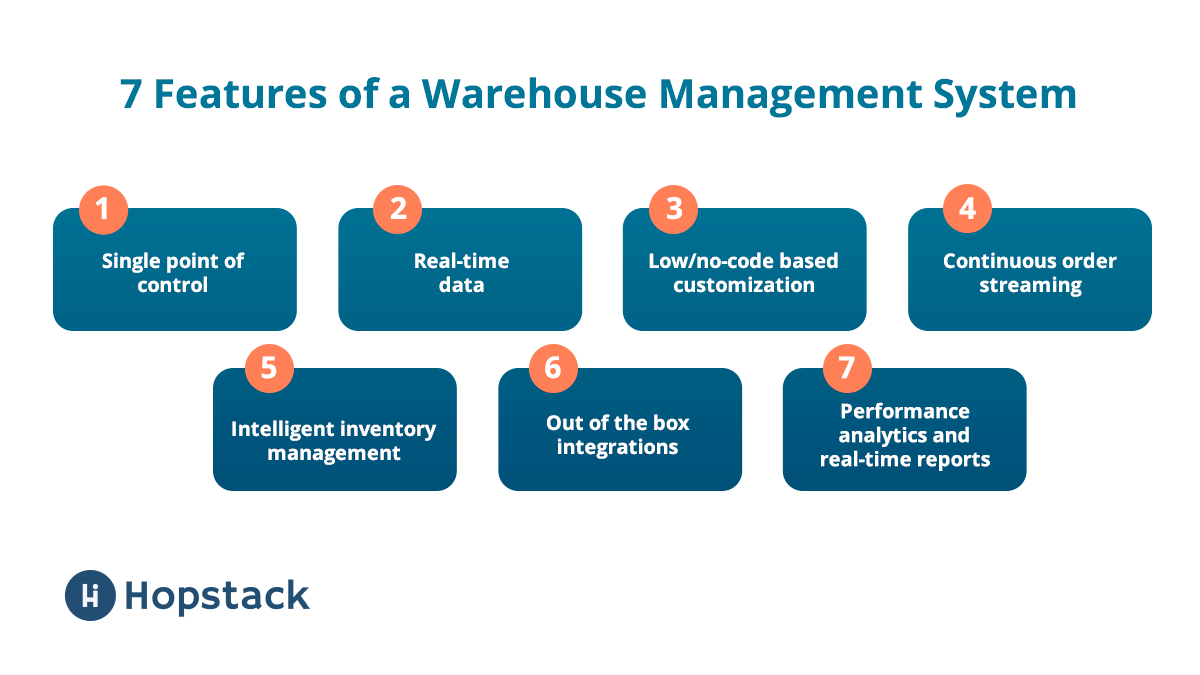
1. Real-Time Inventory Tracking
Real-Time Inventory Tracking is a critical feature of modern WMS software, offering unparalleled visibility into inventory levels and movements within a warehouse. One of the biggest challenges faced by warehouse managers is the lack of visibility in real-time. In fact, over 71% of warehouse managers surveyed deemed poor and timely visibility of activities as one of the major factors in poor decision making.
This WMS feature employs advanced technologies like RFID, barcoding, and IoT devices to track inventory at every stage - from receiving to storage, picking, packing, and shipping. By providing instant updates, it eliminates the delays inherent in manual tracking methods.
The real advantage of real-time tracking lies in its ability to drastically improve inventory accuracy and efficiency. It reduces the likelihood of stockouts and overstock situations, enabling businesses to maintain optimal inventory levels. This precision is essential in today's fast-paced market where customer expectations for quick delivery are high. Furthermore, real-time data assists in making informed decisions, enabling proactive management of inventory.
For instance, it can highlight trends in product movement, facilitating better forecasting and planning. This level of insight helps in reducing holding costs, improving order fulfillment rates, and enhancing customer satisfaction. In an era where data-driven decision-making is paramount, real-time inventory tracking proves to be an invaluable tool for warehouse management.
2. Automation and Robotics Integration
Automation and Robotics Integration in WMS is transforming the landscape of warehouse operations. This WMS features integrates software systems with physical automation tools like robotic picking systems, sorters and automated mobile robots (AMRs), automated guided vehicles (AGVs), and conveyor belts. The integration streamlines various warehouse processes, from sorting and picking to packing and shipping, reducing manual intervention and the associated human error.
The primary advantage of this integration is the significant boost in operational efficiency and productivity it brings. WMS’ today should come with out-of-the-box integrations, both software and hardware. Automated systems can work tirelessly, handle repetitive tasks more quickly and accurately than human workers, and operate in environments not suitable for humans (like cold storage). This leads to faster order processing times and increased throughput, crucial in an e-commerce driven world where speed and efficiency are key competitive factors.
Additionally, automation reduces labor costs and mitigates the impact of labor shortages, a frequent challenge in the logistics sector. It also enhances safety by taking over high-risk tasks, thereby reducing workplace accidents. In summary, automation and robotics integration in WMS not only optimizes warehouse operations but also plays a strategic role in maintaining a competitive edge in the logistics industry.
3. Advanced Analytics and Reporting
Advanced Analytics and Reporting in WMS features leverages data to provide deep insights into warehouse operations. This feature of warehouse management software encompasses a range of analytics tools and techniques, from basic reporting to more complex predictive analytics and data visualization. These tools analyze vast amounts of data generated by warehouse activities to identify patterns, trends, and inefficiencies.
The advantage of advanced analytics lies in its ability to record of all activities completed and transform data into actionable insights. It enables managers to make data-driven decisions that can significantly impact the bottom line. For example, analytics can reveal bottlenecks in the supply chain, inefficiencies in picking routes, or issues with supplier reliability. Addressing these issues leads to improved operational efficiency and reduced costs.
Predictive analytics, a subset of advanced analytics, can forecast future trends based on historical data, allowing for better inventory planning and resource allocation. This foresight helps in avoiding overstocking or stockouts, leading to more efficient inventory management. Additionally, sophisticated reporting tools provide stakeholders with clear, understandable reports, facilitating transparent communication and strategic planning. In a world where data is king, advanced analytics and reporting in WMS are indispensable for optimizing warehouse operations and staying competitive.
4. Cloud-Based Technology
Cloud-Based Technology in WMS features represents a shift from traditional, on-premises systems to those hosted on cloud servers. This feature of warehouse management system means that the WMS software and its data are accessible over the internet, providing flexibility, scalability, and cost-effectiveness. Unlike traditional systems, cloud-based WMS solutions don't require extensive hardware infrastructure or maintenance, as these are managed by the service provider.
The advantage of cloud-based technology lies in its scalability and accessibility. As businesses grow, the cloud infrastructure can easily scale up to meet increased demand without the need for significant capital investment in hardware. This scalability ensures that businesses of all sizes can leverage the power of a state-of-the-art WMS. Moreover, being internet-based, it offers the advantage of accessibility from anywhere, at any time, enabling remote management of warehouse operations.
This feature is particularly crucial in today's global and mobile business environment. Additionally, cloud-based systems typically offer regular updates and improvements without the need for manual interventions, ensuring that warehouses are always running the latest software version with the most up-to-date features and security measures. This ongoing innovation and enhancement help businesses stay competitive in a rapidly evolving marketplace.
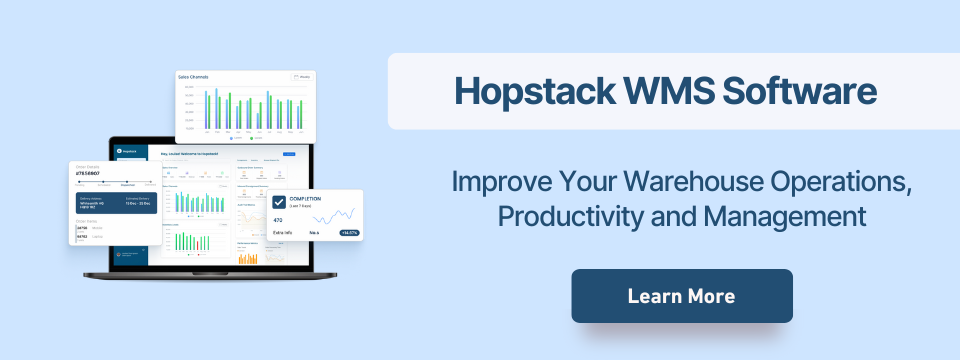
5. Internet of Things (IoT) Connectivity
Internet of Things (IoT) Connectivity in WMS involves integrating various IoT devices, such as sensors, RFID tags, and smart machinery, into the warehouse management system. These devices collect and transmit data about every aspect of the warehouse operations, from the condition of goods to the efficiency of equipment.
The key advantage of IoT connectivity as a feature of warehouse management system is the unprecedented level of visibility and control it provides over warehouse operations. IoT devices can track the condition of goods in real time, alerting managers to issues like temperature deviations or potential damage. This level of monitoring is crucial for sensitive or perishable goods, ensuring quality and compliance with regulations.
Furthermore, IoT data can optimize warehouse operations, such as dynamically adjusting storage locations based on frequency of access or automating inventory replenishment. The real-time data collected by IoT devices also feeds into predictive analytics, enhancing the ability to make proactive decisions. For instance, predictive maintenance of equipment based on IoT data can significantly reduce downtime and extend the life of warehouse machinery. In an era where efficiency and accuracy are paramount, IoT connectivity in WMS plays a pivotal role in enhancing operational effectiveness and reducing costs.
6. Artificial Intelligence and Machine Learning Capabilities
Artificial Intelligence (AI) and Machine Learning (ML) Capabilities in WMS bring intelligent automation and decision-making to warehouse operations. These technologies enable the WMS to learn from data, predict outcomes, and make decisions with minimal human intervention. AI and ML can optimize various aspects of warehouse management, from inventory forecasting and demand planning to efficient routing for picking and automated customer service interactions.
The advantage of AI and ML lies in their ability to constantly improve operations through learning. For instance, ML algorithms can analyze historical data to predict future inventory needs, reducing the likelihood of stockouts or overstocking. This predictive capability is invaluable in optimizing inventory levels and improving customer satisfaction through reliable order fulfillment.
AI-driven automation in tasks like sorting and picking can lead to significant efficiency gains, freeing human workers for more complex tasks. Moreover, AI algorithms can identify patterns and insights that might be missed by human analysts, leading to more informed and strategic decision-making. In customer service, AI-driven chatbots and automated responses can enhance customer experience by providing quick and accurate information.
The integration of AI and ML in WMS represents a significant step towards smarter, more responsive, and efficient warehouse operations, crucial for maintaining a competitive edge in the logistics and supply chain industry.
7. Multichannel Fulfillment Support
Multichannel Fulfillment Support in WMS addresses the complex needs of managing inventory and orders across various sales channels, including online marketplaces, retail stores, and direct-to-consumer platforms. This feature integrates different sales channels into a single, cohesive system, enabling seamless management of orders, order batching, inventory, and customer information.
The advantage of multichannel fulfillment support lies in its ability to synchronize operations across diverse sales channels, providing a unified view of inventory and orders. This synchronization is crucial for maintaining accurate inventory levels and avoiding overselling, especially important in today's e-commerce driven market where consumers expect real-time product availability information. Moreover, it streamlines order processing by consolidating orders from different channels into a single platform, enhancing efficiency and reducing the risk of errors.
This integration allows for more efficient allocation of inventory and resources, ensuring that the most efficient fulfillment methods are used. Additionally, a unified system improves customer experience by providing consistent and reliable service, regardless of the sales channel. In an increasingly omnichannel retail environment, multichannel fulfillment support is vital for businesses looking to expand their reach without compromising on operational efficiency or customer satisfaction.
8. Customizable and Scalable Interface
A Customizable and Scalable Interface in WMS allows the software to be tailored to meet the specific needs of a business and to adapt as those needs change. This feature enables users to configure layouts, workflows, and reporting according to their unique operational requirements. The scalability aspect ensures that the WMS can grow with the business, accommodating increases in inventory, order volume, and complexity without the need for a complete system overhaul.
The key advantage of a customizable and scalable interface is that it offers flexibility and relevance to a wide range of businesses, from small startups to large enterprises. Customization ensures that the WMS aligns perfectly with the specific processes and practices of a business, thereby enhancing usability and efficiency.
For instance, a business can tailor the interface to highlight the most relevant data, streamline warehouse workflows, and simplify the user experience. Scalability is equally important, as it ensures that the WMS can handle growth in business size or changes in business models, such as expanding product lines or entering new markets.
This feature eliminates the need for frequent system upgrades or migrations, providing a long-term solution that evolves with the business. In a dynamic and competitive business landscape, a customizable and scalable WMS interface is essential for ensuring that warehouse operations remain efficient, responsive, and aligned with business objectives.
9. Enhanced Security and Compliance Management
Enhanced Security and Compliance Management in WMS is crucial for protecting sensitive data and ensuring adherence to regulatory requirements. This feature encompasses robust security protocols, access controls, and compliance tools to safeguard against data breaches, unauthorized access, and non-compliance with industry regulations.
The advantage of enhanced security and compliance management is twofold: protecting the business from cybersecurity threats and ensuring regulatory compliance. Strong security measures, such as encryption, secure user authentication, and regular security audits, are essential in protecting sensitive information like customer data and business intelligence.
This protection is not only critical for maintaining trust and credibility but also for preventing financial and legal repercussions associated with data breaches. Compliance management is equally important, especially in industries with stringent regulatory requirements, like pharmaceuticals and food and beverage. A WMS with robust compliance tools ensures that operations adhere to industry standards and regulations, such as those related to product handling, storage conditions, and reporting. This adherence mitigates the risk of costly fines and legal issues.
Additionally, it helps maintain high standards of quality and safety, which are paramount in retaining customer trust and loyalty. In summary, enhanced security and compliance management in WMS is vital for protecting the business from internal and external threats while ensuring operational integrity and regulatory adherence.
10. Voice-Directed Picking and Task Management
Voice-Directed Picking and Task Management in WMS uses voice recognition technology to guide warehouse workers through their picking and task assignments. This WMS feature involves using a headset and microphone through which workers receive verbal instructions for locating and picking items. The workers confirm their actions verbally, which the system records and processes in real time.
The advantage of voice-directed systems as a feature of warehouse management system is their ability to significantly increase efficiency and accuracy in picking processes. By keeping hands and eyes free, workers can focus more on the task at hand, reducing the likelihood of errors and increasing picking speed. This method also improves safety in the warehouse, as workers are less distracted by handheld devices or paper lists.
Furthermore, voice-directed systems can be easily learned, reducing training time for new employees and increasing overall workforce flexibility. The real-time interaction with the WMS ensures immediate update and verification of tasks, enhancing inventory accuracy and order fulfillment rates. This technology is particularly beneficial in high-volume, fast-paced warehouse environments where efficiency and accuracy are paramount. The integration of voice technology in WMS represents a significant step towards a more interactive, efficient, and error-resistant warehouse operation.
11. Predictive Maintenance for Warehouse Equipment
Predictive Maintenance for Warehouse Equipment in WMS leverages data analysis and predictive algorithms to forecast when warehouse equipment will require maintenance. This proactive approach uses sensors and IoT technology to monitor the condition and performance of equipment such as forklifts, conveyors, and automated picking systems.
The primary advantage of predictive maintenance as warehouse management software feature is the reduction in equipment downtime and associated costs. By predicting maintenance needs before a breakdown occurs, warehouses can schedule repairs during non-peak times, minimizing disruption to operations. This foresight extends the life of equipment by preventing minor issues from developing into major failures.
Additionally, predictive maintenance can lead to significant cost savings, as preventative repairs are often less expensive than emergency fixes. This approach also improves safety in the warehouse by reducing the likelihood of accidents related to equipment failure. In an operational context where equipment reliability and efficiency are crucial, predictive maintenance ensures continuous, smooth operation of warehouse activities, contributing to overall operational excellence and cost-effectiveness.
12. Mobile Accessibility and Responsive Design
Mobile Accessibility and Responsive Design in WMS refers to the capability of the system to be accessed and used effectively on various mobile devices, such as smartphones and tablets. This warehouse management system feature ensures that the WMS interface adapts to different screen sizes and orientations, providing an optimal user experience on any device.
The advantage of mobile accessibility lies in the increased flexibility and real-time connectivity it offers. Warehouse managers and staff can access the WMS from anywhere in the warehouse or even off-site, enabling them to make timely decisions and respond quickly to changing situations. This mobility is particularly beneficial for large warehouses where being tied to a stationary terminal is impractical.
Responsive design enhances user experience by ensuring that the system is easy to navigate and use, regardless of the device. This adaptability is crucial in today’s mobile-centric world, where users expect seamless functionality across all their devices. Furthermore, mobile accessibility allows for greater collaboration and communication among team members, as information can be easily shared and accessed on the go. In an industry where speed and efficiency are critical, mobile accessibility and responsive design in WMS are key warehouse management system features for enabling a more dynamic, responsive, and efficient warehouse management approach.
.png)
Hopstack WMS with Advanced Features For Fulfillment Solutions
Hopstack offers an advanced suite of warehouse order management, inventory management, workforce management, and IoT in warehouse intelligence modules. Hopstack's WMS features align with all the aforementioned modern warehouse management software features to provide seamless fulfillment and warehousing solutions across all warehouse processes be it picking, packing, shipping, receiving, or additional services like kitting and more.
Schedule a demo today to understand how Hopstack’s AI-driven WMS features can help you supercharge your warehousing operations and can help eliminate any choke points in your warehousing process.