With the advent of e-commerce and quick shipping, it became increasingly important for businesses to increase their proximity to their customers. Suddenly, having one massive single warehouse in the middle of nowhere was not prudent anymore.
With the rise of multiple fulfillment centers and the introduction of multi-origin shipping, it became clear that multi-warehouse management is the way forward. But managing inventory across multiple warehouses comes with challenges like communication gaps, underutilized resources, unsold inventory, inventory shortage ,and lack of oversight.
The multi-warehouse order management module of the Hopstack platform aims to change just that. With a seamless experience and an optimization engine, the module ensures the maximization of savings and helps unlock hidden efficiencies in terms of costs and timelines. Read ahead to learn more about how multi-warehouse operations can be streamlined by using the Hopstack platform.
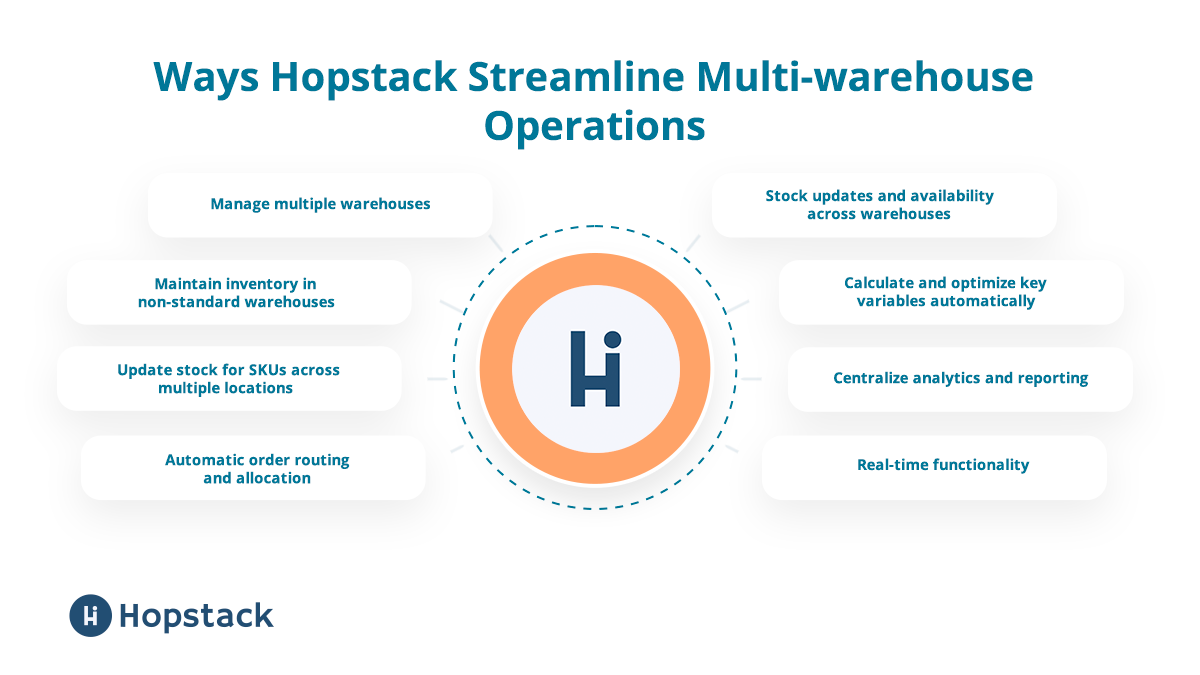
Manage multiple warehouses
The multi-warehouse order routing module allows warehouse managers and business owners to include and manage multiple warehouses from the same platform. Warehouse details and locations can be uploaded into a single Hopstack instance and treated as different locations within the same platform. This allows companies to centralize their fulfillment operations and oversee all operations from one location.
Ideal for maintaining inventory in non-standard warehouses
Most companies store stock products in more than one location and it may not necessarily be a warehouse. It may be an office store, a dark store, a distribution center, a fulfillment center, or just a simple stock room within the corporate headquarters.
The multi-warehouse order module can be modified to manage these locations as well. This is especially helpful to maintain chains of custody for goods that have been dispensed internally to employees and stakeholders.
Update stock for SKUs across multiple locations
The module allows warehouse managers to update inventory levels for SKUs across multiple warehouse locations. Through the Stock Adjustment Module, managers can update pieces of inventory for SKUs in the case of a stock transfer, gift distribution, damage to infrastructure, or any other situation which results in an inability to update from the host location. This ensures that company-wide operations are not affected by a fulfillment gap at any single location.
If you run a small service business like a repair shop, you will benefit from managing your spare parts inventory directly in the CRM system. This way, you can write off products from digital warehouses to work orders for accurate record-keeping and performance analytics.
Automatic order routing and allocation based on multiple factors
The multi-warehouse order module automatically splits each order by line item and evaluates the best possible fulfillment flow for those items. The module prioritizes the fulfillment of items through the following factors:
- Maximizing the proximity to the customer
- Maximizing the availability of line items from the same order in the same warehouse
- Minimizing the fulfillment cost of the individual line items
- Prioritizing perishable items or near-expiry items for dilution over others (FIFO)
Apart from these factors, the module also looks at workflows and priorities set by the warehouse management through the rule engine to ensure that the priorities set by the user are also being fulfilled for each order. And if not, managers always have the option to manually change parameters in the fulfillment flow based on business needs.
Stock updates and detailed availability across warehouses
The module automatically updates inventory counts across multiple locations within the platform after every order is fulfilled. It also allows warehouse managers and authorized personnel to view stock levels across different fulfillment centers and warehouses to make decision-making easier. Visibility of real-time data has always been a priority for the Hopstack platform and the multi-warehouse order routing module is no less.
Calculate and optimize key variables automatically
The multi-warehouse order routing module automatically calculates certain key variables for every order processed by it. These variables are crucial in determining the best possible way to fulfill an order. They include:
- Estimated distance: This variable measures the distance between the customer’s location and the warehouse.
- Fulfillment time: This variable measures the amount of time it would take for a line item from an order to be picked, packed, and shipped until it reaches the customer.
- Fulfillment costs: This variable includes all the costs associated with fulfilling an order.
- Shipping costs: This variable outlines the cost of shipping the package with the specified dimensions via different shipping methods and carriers.
These variables are calculated for multiple different conditions and then run through proprietary algorithms to calculate their optimum values. This ensures that warehouse managers are not bogged down by calculating the nitty-gritty of every order and can instead focus on running operations and looking at the bigger picture.
Centralize analytics and reporting
The Hopstack platform focuses on ensuring the best possible visibility of data and analytics so that business owners can make data-driven decisions. The multi-warehouse order routing module comes with a centralized analytics dashboard that contains key metrics about all multi-warehouse operations.
Moreover, it also contains details about how much money and time has been saved through the optimizations implemented by the module. These analytics are accessible to all warehouse managers and authorized personnel as designated across the organization.
Real-time functionality
The module, like all other modules in the Hopstack platform, updates information and data across the entire platform in real time. This ensures that the real-time data received by the rest of the modules is as accurate as it can be.
The functionality also extends to all the platforms and marketplaces that have been integrated with the Hopstack platform. Key information and metrics like inventory items and SKU details are updated in real-time and seamlessly through the Hopstack platform in real-time without external intervention.
The full power of the Hopstack platform
The multi-warehouse order routing module is one of many modules and features that augment the Hopstack platform. Warehouse managers can still take the advantage of hallmark features such as automated workflows, assignment of order and fulfillment priorities, access control, optimized inventory management, picking and packing automation, powerful analytics, and a whole lot more.
All of these functionalities are integrated seamlessly into the module to give warehouse managers and business owners the power to seamlessly manage all warehouse operations through one unified experience.
The multi-warehouse order routing module allows businesses to manage multiple fulfillment locations with unlimited geographic distances with ease. It also provides optimization features that silently work in the background to minimize costs and timelines while maximizing the utility and efficiency of all the resources working towards fulfilling orders.
Learn more about how Hopstack's multi-warehouse order routing can help in optimizing multi-site operations. To get in touch with a product expert, please fill out the form below.