The order fulfillment process encompasses the stages of receiving goods, processing them, and ultimately delivering them to the customer. While the order fulfillment process may seem straightforward, it holds immense significance for businesses, as it can profoundly impact their success. Case in point: 83% of customers consider convenient and accurate fulfillment pivotal in their purchasing decisions.
Furthermore, efficient order fulfillment is integral to shaping your brand's reputation and is critical in influencing your company's profitability, customer satisfaction, and retention.
In this blog, we will break down the order fulfillment process flow and show you how modern warehouses use the latest tech and advanced WMS for effective supply chain management. We will also introduce you to the best tips and strategies for streamlining and optimizing your order fulfillment process for greater efficiency and accuracy.
Order Fulfillment Process - 5 Key Steps
From receiving the order to handling order returns and managing it, here are some of the most important steps in the order fulfillment process:
Receiving Inventory
The first step in the order fulfillment process is receiving inventory, which involves acknowledging and storing incoming inventory at your warehouse or a fulfillment center. Since this step sets the tone for the rest of the process, it needs to be seamless and accurate.
Irrespective of the fulfillment type – in-house fulfillment or 3PL – the inventory undergoes a counting process and quality checks upon arrival at the loading docks. In fact, identifying errors and discrepancies early in the warehouse receiving process helps prevent more significant problems during picking, packing, or shipping inventory. Similarly, an accurate stock count can prevent inventory stockout or overstocking situations, enabling businesses to manage their inventory better.
An efficient warehouse-receiving process plays an important role across businesses. For example, in manufacturing businesses, improving the efficiency of the receiving warehouse process reduces the conversion cycles of raw materials to finished goods. In retail and e-commerce businesses, a robust warehouse receiving process enhances order lead times.
The second step in the inbound logistics process is warehouse putaway, which entails placing the right items in appropriate locations to speed up the picking process. Digitization is the key to an efficient putaway process. Modern Warehouse Management Software (WMS) comes with built-in putaway optimization algorithms that can optimize the putaway route and sequence and handle FEFO compliance.
Picking
After the customer places an order and the processing is complete, the next step in the order fulfillment process involves picking the specific items. Like all industries, automation is revolutionizing warehouse operations, and the global market for warehouse automation is set to reach $69 billion by 2025. Interestingly, businesses have started using automated warehouse picking systems such as pick-to-light, voice picking, robotic picking, vision picking, scanner-based picking, etc., to fasten the picking process, make it more accurate, reduce picking errors, and increase throughput.
However, many companies still employ human picking teams that manually review the packing slips, ensuring the accurate selection of items. The challenge or downside here is that more than 80% of an associate’s time is spent manually picking items from different parts of the warehouse to complete an order—a significant hindrance in achieving warehouse labor efficiency.
Along with efficiency, an error-prone picking process can be an expensive mistake that most businesses cannot afford. According to Honeywell, errors in the order-picking process can cost a business anywhere from $10 to $250 each, depending on the value of the products.
Packing
After picking, the next step in the order fulfillment process flow is packing. On a high level, this involves placing the right items in a box or poly mailer, which is then dispatched to the customer. In fact, the quality of packaging materials plays an important role in purchasing decisions. For 72% of American consumers, their purchase decisions were influenced by a product's packaging design, while 67% said that the packaging materials were the deciding factor.
In the packing stage, packing associates must ensure that the product is safely placed and packed. Receiving damaged or defective products is the leading reason for customer returns. A Statista report states eight out of ten U.S. online shoppers who had returned an order said they did so because the item was damaged or defective. Therefore, during the packing process, it is crucial to incorporate insulating or protective materials like bubble mailers, bubble wraps, and poly bags to prevent delicate goods from being broken or damaged during transit.
To attain high packing efficiency and accuracy, modern warehouses have started employing cutting-edge technology like packing robots, automated conveyor systems, and advanced WMS to automate the entire packing process—from choosing the right box size to sorting the boxes according to the shipping channels.
Shipping
Shipping is no longer the process of sending orders from Point A to Point B; it is all about finding the best way for your customers to enjoy a transparent and hassle-free experience. Furthermore, it is one of the most important steps in the order fulfillment process workflow since it plays a major role in customer satisfaction and business success. This step encompasses procuring shipping labels, attaching the right label to each packaged order, and dispatching them to customers using carriers such as USPS, FedEx, UPS, and DHL.
Another significant process in shipping is the selection of shipping carriers, and this varies based on multiple factors. For example, some fulfillment providers establish preferred partnerships with specific shipping carriers that offer them discounted rates, while others compare shipping costs across various carriers, ensuring the most cost-effective pricing for each shipping option.
After the cost factor, speed is a crucial element that plays a vital role in shipping. According to Statista, 41 percent of global shoppers expect to receive their online orders within 24 hours and interestingly, 61% of consumers are willing to pay extra for this expedited shipping option, in such a competitive it’s imperative to choose a carrier, that offers the best price while also having a faster delivery speed and track record of delivering what’s promised.
Finally, the tracking information of each order must be shared with your customers once the order is shipped so they can track and get real-time updates on the orders.
Returns Processing
There will be multiple instances where customers want to return some or all items from their orders, and it is inevitable. Orders are returned for many reasons, ranging from delayed deliveries to receiving damaged or incorrect items. In fact, close to 23 percent of return orders are due to the delivery of incorrect items.
To effectively manage order returns, you must have a well-defined returns processing plan outlining how customers can return items, how you will handle restocking or disposal, and who will bear the return logistic charges. Also, to provide a hassle-free return processing experience, you must clearly communicate how you will facilitate the process, whether it is an in-store return, mail-in return, or both. Additionally, you must determine the return window and who will cover the cost of return shipping and communicate it with the customer.
In today’s competitive landscape, many businesses have already started to invest in AI and automation for decision-making processes in returns management, such as determining the best course of action for a returned item (e.g., repair, refurbishment, or disposal) and identifying customer return patterns for actionable insights.
In short, a robust returns management workflow can streamline the entire process, reduce costs, and improve customer satisfaction.
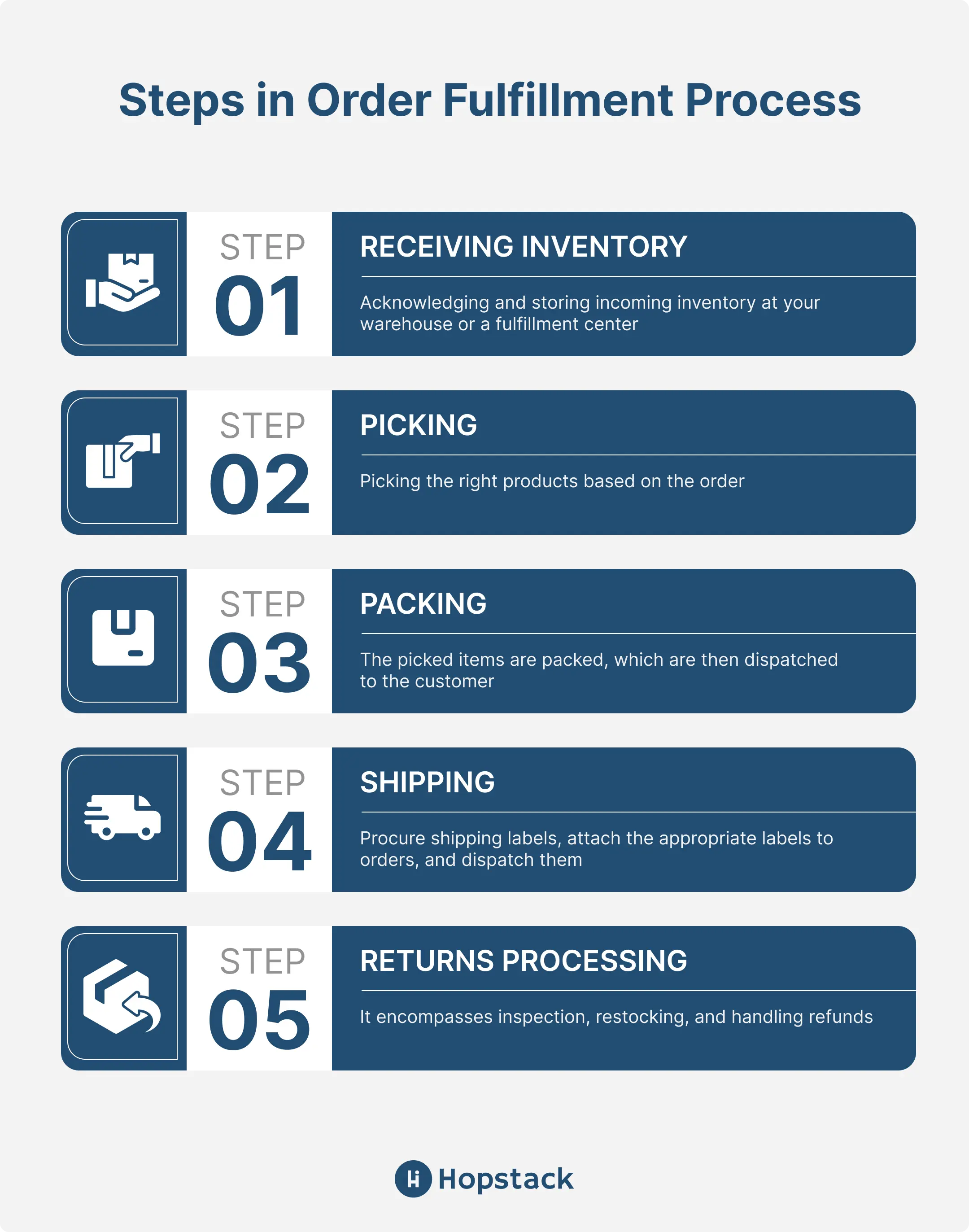
Challenges in Order Fulfillment Process
The order fulfillment process can be complex, and various challenges can arise at different stages. Some common challenges in the order fulfillment process include:
Inaccurate inventory levels
It is no secret that inventory management is a daunting task in the order management process. Manually maintaining accurate inventory levels, which involves physically counting inventory, is a time-consuming and error-prone task.
With no real-time data in hand, businesses often end up stocking out or overstocking. High stock-out rates can lead to a significant loss in sales and customers, while overstocking affects your profitability. Inaccurate inventory data can result in fulfillment delays and impact customer satisfaction. According to Netstock, 43% of consumers indicated they are more likely to ditch a product after experiencing two or more stockouts.
Order processing errors
Order processing errors in the order fulfillment process can pose significant challenges for businesses. A Honeywell report states that errors in the picking process can cost anywhere from $10 to $250 each. These errors can have various consequences (other than monetary loss), impacting customer satisfaction, operational efficiency, and overall business reputation.
For instance, incorrect or delayed orders can lead to customer dissatisfaction. Customers expect accurate and timely deliveries, and any errors in the order fulfillment process can result in frustration, negative reviews, and potential loss of business.
Also, order processing errors have a direct impact on order return rates, thus increasing product returns and refund requests. This not only incurs additional costs for processing returns but also affects inventory levels and may result in the loss of saleable items.
Shipping and delivery issues
Challenges related to shipping, including delayed delivery, poor shipping speed, damaged goods during transit, high cost, and lost packages, can negatively impact your brand’s reputation and customer experience. Shipping speed and costs both play a vital role in creating a seamless shipping experience. A Voxware study states that 69% of respondents are less likely to shop with a retailer in the future if an item they purchased is not delivered on the promised date.
Partnering with reputable shipping carriers with good track records and customer reviews can help you reduce such instances. Additionally, continuously monitor the quality of packaging and packaging materials to prevent damage.
Integration challenges
Issues with integrating various systems, including order management, inventory management, and shipping platforms, can lead to inefficiencies and errors in the order fulfillment process. Different systems might store data independently, creating isolated data silos, and this can result in duplicate data entry, inconsistencies, and difficulties in obtaining a holistic view of warehouse operations.
For example, if there's a delay or a lack of synchronization between the order management system and the marketplace, a product can be sold on the marketplace even if it's already out of stock. This can lead to overselling, where more units are sold than are physically available in the warehouse. Also, warehouses often need to adhere to industry regulations and standards. Without integrated systems, compliance can be challenging, leading to potential legal and regulatory risks.
Returns and reverse logistics
With the growth of e-commerce and retail over the years, returns have also grown significantly. National Retail Federation estimates that a whopping $816 billion worth of merchandise was returned in 2022.
Handling returns and managing the reverse logistics process can be complex. Deciding how to restock returned items, process refunds, and handle return shipping can pose challenges for businesses. Unclear return policies, extremely long return processing times, and inefficiencies in restocking returned items are some of the significant challenges that businesses face today.
Each of the above-mentioned challenges has its own repercussions on the business in the form of dissatisfied customers and lost sales. For example, long processing times and unclear return policies can frustrate and confuse the customer. Similarly, inefficiency in reverse logistics can add up costs and affect your sales cycle.
Customer communication
Keeping customers informed about their order status, tracking information and any delays is crucial for a positive customer experience. A Hubspot study mentions that 93% of customers are likely to shop again with a brand following a positive customer service experience.
Communication challenges can arise if there are delays in the fulfillment process, inventory shortages, technical glitches, or unforeseen logistical issues. When faced with these challenges, you must proactively convey the specifics of the situation, the steps being taken to address the issue, and any alternative solutions offered to customers. This level of transparency helps mitigate frustration, as customers appreciate being kept informed and involved in the resolution process.
How to Improve the Order Fulfillment Process?
Improving the order fulfillment process is crucial for enhancing customer satisfaction and operational efficiency. Here are some strategies you can consider:
Use a Warehouse Management Software (WMS)
Implement a WMS software to automate warehousing, order processing, inventory management, and shipping. In fact, 60% of industry experts recognize warehouse management systems as key automation solution for modern warehousing.
Here are several ways in which a WMS contributes to the efficiency and effectiveness of order fulfillment:
- Inventory Visibility: A WMS provides real-time visibility into inventory levels, locations, and status. This ensures that order pickers and packers can access accurate information about product availability, reducing the likelihood of errors related to stockouts or overselling.
- Order Accuracy: A WMS helps reduce the chances of picking errors by automating and organizing order-picking processes. It can also optimize pick routes, suggest the most efficient paths through the warehouse, and verify picked items, enhancing overall order accuracy.
- Optimized Order Processing: WMS systems automate and optimize order processing workflows. They facilitate the efficient picking, packing, and shipping of orders by providing clear instructions to warehouse staff, minimizing manual errors, and ensuring a smooth flow of operations.
- Dynamic Slotting: WMS systems often include dynamic slotting capabilities, allowing for intelligent storage location assignment based on factors such as product velocity, size, and order history. This helps reduce travel time during picking, enhancing overall warehouse efficiency.
- Barcode and RFID Integration: Integration with barcode scanning and RFID technology allows for more accurate and faster data capture during various warehouse operations, including receiving, picking, and shipping. This reduces the likelihood of errors and improves the speed of order fulfillment processes.
- Automated Replenishment: A WMS can automate replenishment tasks by monitoring inventory levels and triggering replenishment orders when stock falls below predefined thresholds. This ensures that products are readily available for order fulfillment, minimizing delays.
- Batch and Wave Picking: WMS systems support batch and wave-picking strategies, allowing multiple orders to be picked simultaneously. This enhances efficiency by optimizing the picking process, reducing travel time, and improving overall order fulfillment speed.
- Real-time Order Tracking: WMS provides real-time tracking of orders throughout the fulfillment process. This visibility allows for better order management, enabling businesses to proactively address issues, communicate accurate shipment information to customers, and improve overall customer satisfaction.
- Returns Management: A WMS helps manage the reverse logistics process by providing visibility into returned items, automating restocking decisions, and updating inventory levels accordingly. This ensures that returned items are efficiently reintegrated into available stock.
- Performance Analytics: WMS systems offer reporting and analytics features that provide insights into warehouse performance metrics. This allows businesses to identify areas for improvement, optimize workflows, and make informed decisions to enhance overall order fulfillment efficiency.
Real-time inventory management
According to a recent study, only 43% of small businesses in the US don’t track inventory or do so using a manual system. There are multiple benefits to tracking inventory levels in real-time. For example, it allows for more accurate demand forecasting, helping warehouses stock the right amount of inventory and avoid overstocking or stockouts.
Additionally, real-time monitoring provides a clear and instant view of current stock levels, enabling better decision-making on when to reorder, restock, or redistribute inventory. By adjusting inventory levels in real-time, warehouses can quickly adapt to changes in demand patterns and market trends. With better visibility and control over the data, warehouses can minimize holding costs by avoiding excess inventory and optimizing the overall supply chain management.
Optimize warehouse layout
An optimized warehouse layout plays a critical role in the speed and accuracy of your warehouse. A recent study states that the layout of your warehouse has a direct effect on work productivity. A well-designed warehouse layout minimizes the distance employees and automated systems need to travel to pick, pack, and ship orders. This reduction in travel time increases overall productivity and ensures that orders are processed more quickly.
Optimize your warehouse layout for efficient picking and packing by grouping similar products together and arranging them based on order frequency. By placing fast-moving items closer to packing stations, you can minimize unnecessary movements and increase order processing speed.
Additionally, the layout should facilitate a logical flow of products from receiving to storage, picking, packing, and shipping. This ensures that items move seamlessly through the various stages of order fulfillment, reducing bottlenecks and delays.
Employee training
Provide regular training for warehouse staff to improve their picking, packing, and shipping efficiency. Provide hands-on training to employees. Allow them to practice each step of the order fulfillment process under supervision to ensure they understand the practical aspects.
If your order fulfillment process involves specific software or technology, ensure that employees are well-trained in using these tools. This could include training on order management systems, inventory management software, and any other relevant platforms. Also, cross-train employees so they can handle multiple tasks, reducing dependency on specific individuals.
Finally, performance monitoring systems should be implemented to track employee progress and identify areas where additional training may be needed.
Track and improve performance metrics
Tracking order fulfillment KPIs helps businesses to measure the customer experience and identify areas for improvement. By tracking key metrics like on-time delivery, order accuracy, and customer satisfaction, companies can ensure that their customers are happy with the order fulfillment process.
Additionally, performance metrics help identify bottlenecks and inefficiencies in the order fulfillment process. By tracking key indicators, businesses can pinpoint areas that need improvement and implement strategies to enhance overall efficiency.
Invest in the latest technology
Explore emerging technologies like artificial intelligence and machine learning to optimize routing, demand forecasting, and other aspects of order fulfillment. Leverage WMS's advanced analytics feature to gain insights into customer behavior and optimize inventory levels. Here are some of the latest tech innovations in warehousing that businesses can explore:
Automated Storage and Retrieval Systems (ASRS)
ASRS are computerized systems designed to efficiently manage and handle inventory within a warehouse or distribution center. These systems utilize a combination of automated machinery, robotics, and software to store products in designated locations and retrieve them as needed.
3D bin packing
3D bin packing is an optimization algorithm used in logistics and inventory management to efficiently pack objects of varying sizes into three-dimensional containers or bins, minimizing wasted space.
Augmented Reality (AR)
AR is used for order picking and packing processes. It provides visual cues and information to warehouse workers through smart glasses or other AR-enabled devices, improving accuracy and efficiency.
Automated Guided Vehicles (AGV)
Automated Guided Vehicles (AGVs) are robotic vehicles equipped with navigation systems that autonomously transport goods within warehouses. These vehicles enhance efficiency by automating material handling tasks, such as goods transportation and order picking.
Hopstack for an accurate and efficient order fulfillment process?
Hopstack's advanced WMS helps boost the order fulfillment process with intelligent and guided pick, pack, and ship operations. Here's how Hopstack can help improve the efficiency of the order fulfillment process for you:
Picking
Hopstack creates intelligent picklists to optimize pick rates and reduce the distance each picker covers. Furthermore, it can help enhance picker productivity and ensure pick accuracy through guided picking workflows.
Additionally, it seamlessly integrates with handheld scanners, pick-to-light systems, voice-picking, and automated picking robots to facilitate precise picking processes.
Packing
Use Hopstack's optimized packing feature to streamline packing operations, which helps significantly decrease packing time and minimize the consumption of packing materials.
With Hopstack, you can auto-generate and print box and pallet labels, inserts, and shipping documents and reduce packing and labeling time by 50%. Also, its seamless integration with weighing scales and dimensioning robots ensures weight and dimension compliance, further enhancing efficiency in the packing process.
Shipping
Hopstack instantly gets you pricing and delivery information from all major shipping carriers. You can then evaluate delivery time and other necessary variables and choose the right shipping carrier for every order. Also, Hopstack lets you combine orders based on business rules to minimize packing and shipping costs.
Ready to make your order fulfillment process efficient and accurate? Contact us now to schedule a demo and see Hopstack in action.