Implementing a Warehouse Management System (WMS) is a fairly complex and challenging process that involves many possibilities of things going wrong. Since there are so many different risks and potential pitfalls and challenges, not all WMS implementations are a success.
At every stage in the WMS implementation process, there are various things that can go wrong resulting in delayed timelines, cost overruns, and even abandoned projects.
A WMS implementation project that isn’t executed properly can leave a trail of difficulties. Even if the WMS goes live in a warehouse, improper implementation, setup, and training could mean poor adoption, subpar productivity, technical challenges, downtimes, and poor overall customer satisfaction.
WMS implementation challenges
Here are some of the key challenges faced by warehouse operators and WMS providers in the WMS implementation process and how to avoid them.
Choosing the wrong Warehouse Management System (WMS)
Choosing the wrong WMS is the most fundamental mistake a customer can make. There are WMS’ in the market that are better suited for a use case or a particular industry.
For example, a B2B warehousing 3PL might choose a WMS product that is better suited for e-commerce fulfillment or vice versa. A 3PL business might choose a WMS that provides a more robust system to individual brands.
Alternatively, a brand primarily operating in the D2C (Direct-to-consumer) model, might end up choosing a WMS better suited for wholesale distribution and warehousing.
Choosing the wrong WMS could translate into difficulties in the implementation process and a poor post-implementation experience.
A customer could also end up choosing a WMS that doesn’t offer all the capabilities that it requires. For example, an e-commerce fulfillment company might require an intelligence and analytics-centric WMS that focuses on labor productivity, optimization, and real-time visibility. Similarly, an enterprise warehouse would require a system that enables the control of different robots and devices for advanced automation.
Lack of preparedness for WMS implementation
There are a plethora of prerequisites needed to successfully implement a WMS in an advanced smart warehouse. The prerequisites include:
- Having rightly defined processes
- Defined user roles
- Location codes
- SKU-bin mappings
- Hardware procurement
and more.
A lack of preparedness could lead to poor setup and configuration. The WMS provider needs to be enabled with thorough and accurate information to prepare the WMS for the customer’s needs.
The WMS customer in this case must be cognizant of all such prerequisites and must take the necessary action. It is expected from the customer to have clearly defined inbound, storage, and outbound processes, codified locations and bins, standardized SKUs for units, boxes, and pallets, and more.
Inadequate planning
Inadequate or a complete lack of planning is one of the biggest WMS implementation challenges. Often, it is assumed that planning and putting together implementation timelines is the responsibility of the WMS provider. However, that is not true and the wrong expectation to have.
The burden of planning falls equally on the WMS provider and the customer. The implementation plan must be prepared jointly after discussing mutual priorities, expectations, and capabilities.
The WMS project plan must be thorough and account for all the aspects involved in the implementation process. The plan must clearly define all the prerequisites (as discussed above), expected timelines, required resources, and risks.
Here is what a typical WMS implementation plan looks like:
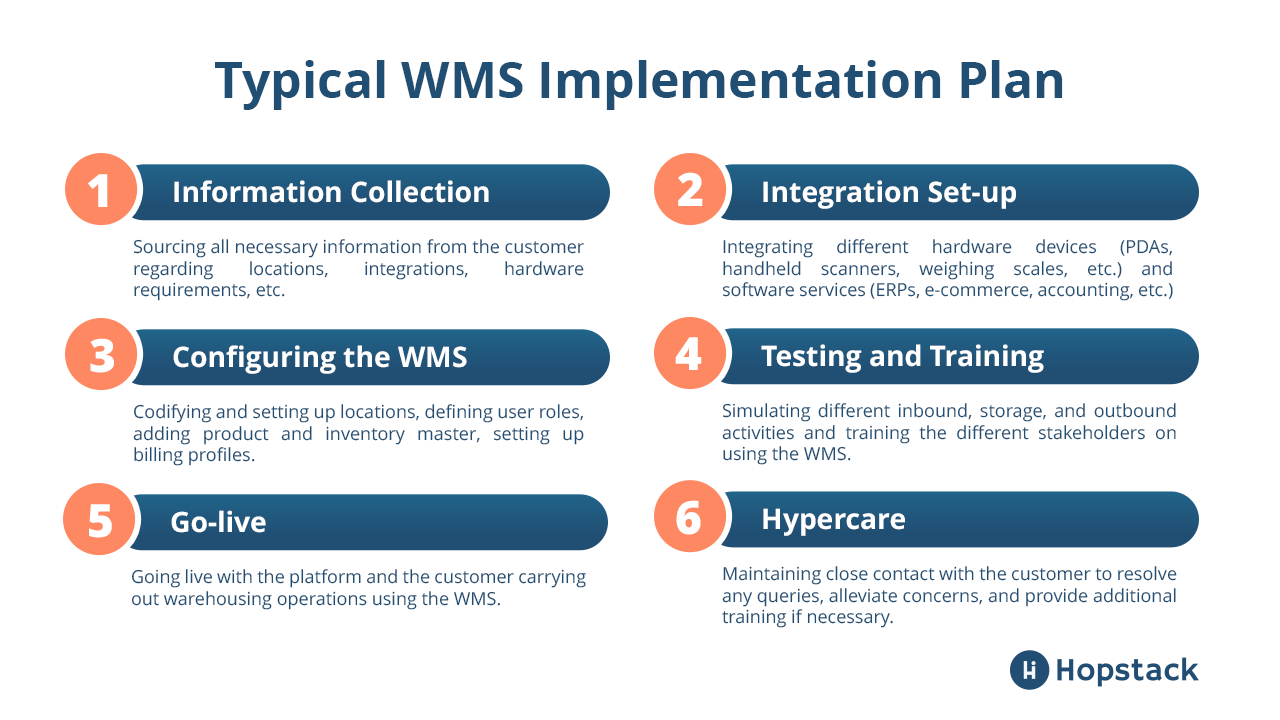
The following table explains the usual WMS implementation timelines at each level of complexity in warehousing operations:
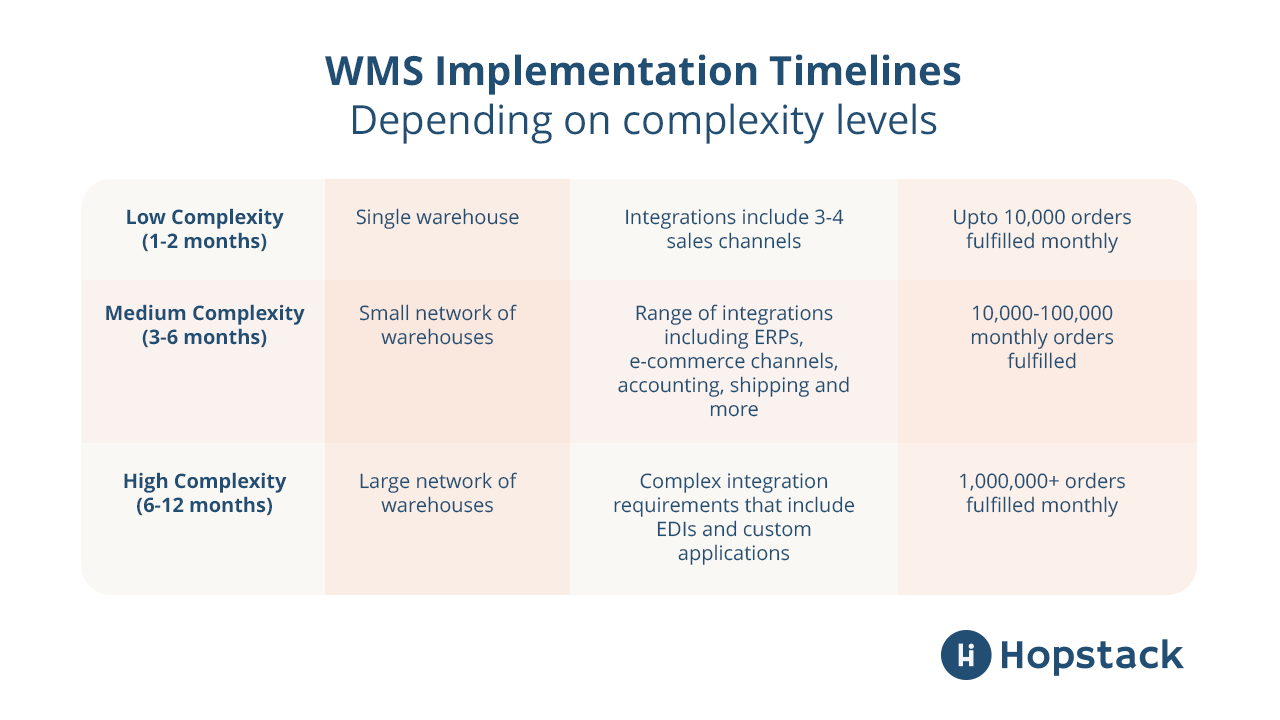
Insufficient testing of the Warehouse Management System (WMS)
The testing stage in the WMS implementation truly puts to test everything the WMS provider and the customer have done so far. Testing can further be broken down into:
- Functional testing: Does each function in the WMS work as intended without causing any technical problems?
- Integration testing: Are the WMS and other services integrated to ensure seamless two-way data transfer without any lapses?
- Performance testing: Is the WMS able to keep up with a sudden surge in orders, SKUs, and consignments without disrupting the warehousing operations?
and more.
Testing involves using actual customer data to simulate different real-world scenarios in inbound, storage, and outbound activities. The results obtained in the testing phase shed light on how adeptly the WMS has been implemented.
However, the actual testing isn’t always as thorough and swift as intended. The WMS provider and the customer may not test every possible use case or process. They might also fail to include the actual end users making the entire process ineffective or leaving certain unidentified gaps in the implementation.
Subpar training
Training is the most important element in the post-implementation experience for any WMS customer. The WMS provider must train all necessary stakeholders (warehouse managers, admins, associates, etc.) on the general use of the platform as well as very specific tasks – receiving, stock transfer, warehouse picking process, and more.
If the WMS provider fails to provide adequate and appropriate training to the warehouse personnel, it could be detrimental to the actual use of the system. Certain potential hazards include poor user adoption, reduced system utilization, operational errors, and lower efficiency.
The WMS provider must also train the personnel on some of the edge cases. Edge cases could include exception handling, blind receiving, managing damages, order returns, and more.
Change management
Introducing a new warehouse management system (WMS) into warehousing management operations is one of the biggest changes an organization can bring about. Poor change management plan and execution on the part of the management can lead to resistance to new software, limited user adoption, or even complete abandonment of the WMS project.
It is critical to effectively handle the change, align all the necessary stakeholders, and manage the resources. The organization must have a change and growth-oriented mindset while undertaking the project and must acknowledge the future upsides of the new WMS.
The organization must have a change management process in place and must also involve all key stakeholders in planning the same. An effective change management campaign is one that helps the organization begin using the new WMS with minimal delay and without any negative impact on the warehousing activity.
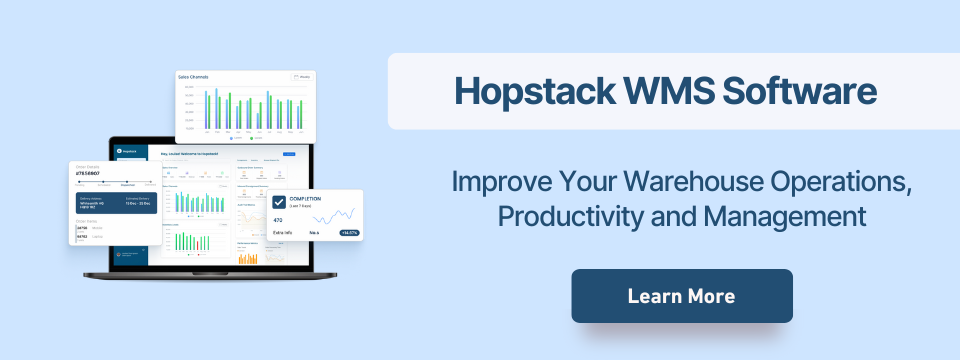
Impact of a failed WMS implementation
Companies, if unable to mitigate the above risks, often fail to implement the WMS properly. Improper implementation can cause various challenges down the road, in both the short term and the long term. The following points explain the detrimental impact on a business if the WMS implementation falls short of expectation:
Higher fulfillment costs
Poor WMS implementation often translates into poor productivity and technical issues that incur additional costs for the warehouse/fulfillment center. Loss in productivity means the warehouse would incur higher costs (labor costs, real estate costs, other resources, etc.) while operating at subpar efficiency. Similarly, a common occurrence of technical issues with the WMS would result in additional costs to resolve the same.
Downtimes
Downtimes are a silent killer for any fulfillment operations. In the age of one-day deliveries, downtimes can sour the customer experience, whether it is a brand or a 3PL. Failed WMS implementation often results in service disruptions that could lead to the business losing its competitive edge and market reputation.
Poor user adoption
The primary objective of any software is to enable people to perform their tasks and responsibilities better. However, a poorly implemented WMS not only fails to deliver in that regard but can also make routine tasks a lot more difficult for warehouse associates. Functional lapses, data irregularities, and outages impact a warehouse associate’s performance and may thus cause lower adoption rates among the smart warehouse workforce.
Impact on business bottom line
With the above points it is clear that a poorly-executed WMS implementation has a direct impact on a business’ vitals. With service disruptions and productivity lapses, a business not only loses out on potential revenue but also incurs additional costs. Such problems impact a business’ profitability and put on line its long-term sustainability.
How to solve WMS implementation challenges
Implementing a Warehouse Management System (WMS) can encounter various challenges. Addressing these challenges effectively is crucial for a successful WMS implementation, ensuring improved efficiency and streamlined warehouse operations.
Comprehensive planning
Begin with a comprehensive planning phase that includes defining objectives, scope, and requirements. Engage key stakeholders to gather their input and ensure alignment with business goals.
Communicate the benefits of WMS
Clearly communicate the benefits of WMS implementation, such as improved efficiency, cost savings, and better customer service to obtain strong support from top management and trust from employees
Provide user training
Invest in thorough training programs for end-users. Ensure that employees are well-versed in the new system to minimize resistance and errors. Consider providing ongoing training and support.
Ensure data accuracy and integrity
Prioritize data cleansing and validation before implementation. Regularly audit and maintain data integrity. Implement data validation checks and controls within the WMS to catch errors early.
Seamless integration
Plan for seamless integration with existing systems (e.g., ERP, CRM). Work closely with IT teams and vendors to ensure compatibility. Use standardized data formats and communication protocols.
Customization
Balance the need for customization with the desire to keep the system manageable. Prioritize critical customizations and thoroughly test them to ensure they work as intended.
Change management
Implement a change management strategy that includes communication, training, and incentives for adopting the new system. Address concerns proactively and involve employees in the process.
In conclusion
The WMS provider and the customer are equal players in the implementation process and equally contribute to the success or failure of the project. Thus it is essential for them to align expectations, maintain regular communication, allocate the necessary resources, and have an overall synergy throughout the WMS implementation lifecycle.
FAQs
What are the most common reasons WMS implementations fail?
WMS implementations often fail due to poor process mapping, unclear requirements, and lack of stakeholder alignment. Rushing configuration or skipping proper testing leads to downstream errors. Without cross-functional ownership and training, adoption suffers and ROI drops significantly.
How important is data accuracy when migrating to a new WMS?
Clean master data is essential before migration—errors in SKU setup, locations, or units of measure can break workflows. WMS logic depends on structured data to assign bins, validate picks, and track inventory. Pre-launch audits and sandbox testing help avoid costly post-launch corrections.
Should I customize my WMS during implementation or stick with out-of-the-box features?
Over-customization early on can delay timelines and create upgrade issues later. Start by aligning workflows with standard features, and only customize where it delivers clear ROI. Modern WMS platforms offer strong configurability, reducing the need for code-heavy changes.
What kind of training should warehouse staff receive before go-live?
Hands-on, role-specific training is key—pickers, receivers, and supervisors should all understand their interface and exceptions. Simulated walkthroughs and live UAT sessions help users build confidence. Post-launch support should also include rapid response for daily workflow issues.
How do you plan for disruptions during a WMS go-live?
Build a fallback process for each critical workflow—such as manual picking or printed labels—in case of system hiccups. Allocate go-live support teams across shifts and establish escalation paths. Avoid going live during peak season to reduce pressure on the operation.
How long does it typically take to stabilize operations after WMS implementation?
It usually takes 2–4 weeks to reach baseline performance, and 2–3 months to optimize workflows. Early pain points often involve inventory mismatches, incorrect task assignments, or user errors. Regular review of issue logs helps accelerate stabilization and performance tuning.
How can I validate that my WMS configuration matches real warehouse workflows?
Run end-to-end process simulations using real SKU data and order profiles before go-live. This includes receiving, putaway, picking, packing, and returns. Involve team leads to identify mismatches between system logic and floor reality.