The global pandemic and the ensuing lockdowns saw many people spending more time at home trying to carry out their normal activities from its confines. As a result, e-commerce boomed and surpassed analysts’ original expectations. It ultimately led to an additional 19% sales growth in 2020 and exceeded forecasts by 22% the following year.
While promising, the growth of ecommerce introduced new and unforeseen challenges for online retailers and the warehouses that supply their inventories. One of the problem areas that emerged was e-commerce fulfillment. Sellers and warehouses found themselves hard-pressed to meet the sudden surge in demand using their current operational capacities.
The global pandemic presents many opportunities for e-commerce but it also brought to light challenges that can prevent it from realizing its full growth potential.
In this article, we outline key challenges in ecommerce fulfillment and highlight a solution.
What Are the Main Challenges in Ecommerce Fulfillment in 2024?
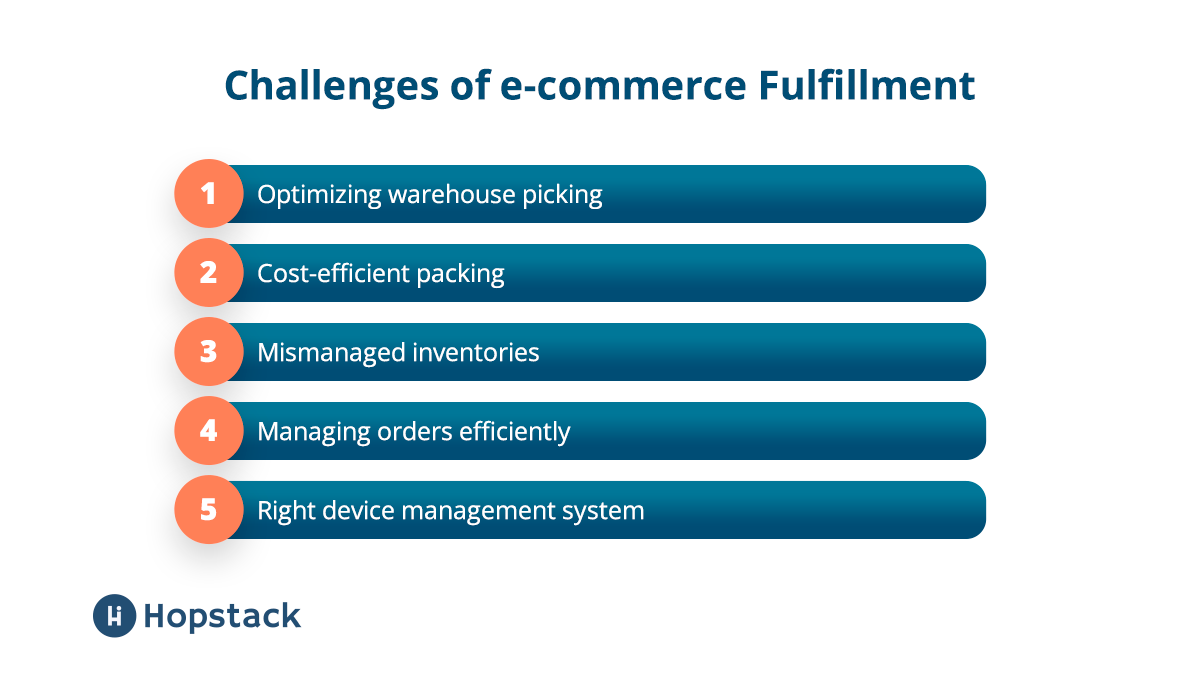
Ecommerce fulfillment greatly relies on the warehouses that process orders. With the unexpected spike in demand, many warehouse managers are re-examining their operational activities to provide faster, more accurate, and more productive results to support the volume.
According to a 2020 survey, 36% of decision-makers in warehouses and distribution centers experienced higher customer expectations around shipping while 35% agreed that there has been an increase in e-commerce transactions. Thirty-four percent feel the pressure to fulfill more orders more quickly and at lower costs.
Here are five order fulfillment challenges that they must look into and address if they are to thrive in this new business environment:
Challenge #1: Optimizing Warehouse Picking
Warehouse operations consists of many activities but one of the most essential is having effective picking operations.
Picking refers to the process of retrieving the right item/s for an online buyer after receiving their order. It’s a big part of operations that eats up a significant part of a warehouse’s budget and is labor-intensive.
Why is it important? At its worst, an inefficient picking system can lead to the wrong items being sent, delayed orders, and orders being sent back. This can be caused by:
- Warehouse associates spending too much time moving around the warehouse to pick up different items and utilizing inefficient routes
- The lack of an efficient system that allows warehouse managers to effectively keep track of operations and pinpoint issues
- Underutilization of equipment and manpower
- Outdated processes or too many manual processes
Picking is integral and indispensable to the order fulfillment process. Having the right tools and systems to support this operation affects customer satisfaction and optimizes operational costs while reducing the work and expense of dealing with returned items.
Challenge #2: Packing the Right Items in a Cost-efficient and Careful Manner
After picking out the correct items, warehouse associates need to pack items in a cost-efficient and careful manner before shipping them. This is an important step because it’s the last chance to correct any picking errors. It’s also a tricky stage because items must be packed in such a way that each package holds as many items as possible without damaging them or exceeding weight limits. At the same time, items must have the right packing material and sufficient shipping and delivery instructions.
Warehouses that are challenged to meet the increase in ecommerce activity can end up employing packing practices that lead to various ecommerce delivery problems like the wrong item being sent, unnecessary shipping costs, and the receipt of damaged items.
Order delivery problems ultimately lower customer confidence and satisfaction and can incur avoidable reverse logistics expenses.
Challenge #3: Mismanaged Inventories
Few things are as frustrating for ecommerce customers as finding out that an ordered item is out of stock and will take longer to ship. Such experiences lower customer satisfaction, encourage buyers to look at competition, and negatively affect a brand’s reputation.
When items are in high demand, inventory turnover is faster. Warehouses have trouble keeping up when their inventory reports are inaccurate, stocking up on slow-moving products is prioritized while in-demand items are in short supply, products are hard to locate, and restocking is manually done.
Challenge #4: Managing Orders Efficiently
Order management encompasses receiving orders up until they’re received and fulfilled by warehouses. While it may sound straightforward to the customer, there are a lot of behind-the-scenes steps where order management can go wrong, especially where higher volumes are involved.
From ensuring that reported inventories are accurate, placing orders, confirming them with customers, picking, and packing to shipping, there are a lot of moving parts that warehouses must stay on top of.
Having multiple systems and reports, an order management system that isn’t integrated with the rest of operations, disorganized order batches, and a lack of relevant performance analytics only exacerbate the problem.
Challenge #5: Having the Right Device Management System in Place
Companies with inventories spread across multiple locations must rely heavily on their device management systems. These systems help warehouse managers keep track of each piece of hardware in the warehouse like scanners, cameras, material handling equipment, and the like.
More than ever, device management systems are important for efficient warehouse operations. It lets managers stay on top of what’s happening inside and allows them to keep a close eye on the performance of the different equipment that feeds the system information. A good device management system is an important part of operations because it allows managers to:
- Identify when equipment needs to be repaired or replaced
- Reduce operational costs and increase efficiency by having a single centralized system across locations instead of different systems for each warehouse
- Reduce the need for onsite repairs
- Access the system on a mobile device instead of having different access points running on different operating systems
- Lets managers and IT configure hardware adjustments remotely
With the increase in demand and competition in ecommerce, warehouses need to ramp up their activities as efficiently and with as little downtime as possible. This can be realized with the right device management system.
Meeting the Challenge With Efficient E-commerce Fulfillment
E-commerce is growing at an unprecedented rate but industry players can only take advantage of it if they can address the challenges that come with the additional demand.
The inability to do so may lead to:
- Poor customer reviews
- Lost sales
- Unnecessarily high fulfillment costs
- Expensive and time-consuming errors
- Losing customers to competition
- Damage to brand reputation
The Key To Efficient E-commerce Fulfillment: Having the Right Ecommerce Fulfillment Technology
Since these opportunities and challenges of ecommerce warehousing arose due to technology, it only makes sense that the solution also lies in its efficient and effective implementation. Many distribution centers today are scaling up by introducing technological innovations such as fulfillment automation, feature-rich applications, and centralized end-to-end systems.
Such advancements offer:
- Relevant and practical applications that let users tweak and make adjustments quickly and easily
- Greater visibility on warehouse operations, allowing managers to more quickly and accurately track performance and pinpoint potential issues
- Access to data analytics from millions of data points
- Predictive capabilities to adjust to fluctuating demands as well as to anticipate and meet expectations
- Optimization algorithms that help increase productivity at every step of fulfillment
Hopstack: An End-to-end Warehouse Operating System
In this article, we outlined five challenges that many fulfillment facilities are facing due to increased demand and the higher volume of transactions. Because Hopstack offers an end-to-end solution, warehouses can easily address all five issues with its digital warehouse platform.
With Hopstack, warehouse managers can expect to optimize their processes and gain more visibility than before into the entire fulfillment process. Hopstack uses proprietary algorithms to boost efficiency in picking, packing, shipping, and other activities so companies can stay ahead of competition while keeping customers happy.
Its comprehensive and feature-rich platform can ultimately help increase customer satisfaction while boosting brand loyalty.
Hopstack is a California-based company with global talent. The company combines the best minds in logistics, data science and engineering to bring efficient and simplified solutions to complex supply chain issues.