What is Picking in Warehouse?
Warehouse picking is the first step in the fulfillment process after the customer places an order. It dictates the speed, accuracy, and overall efficiency of the order fulfillment process — effectively coordinating how fast and effortlessly the order arrives at your customers’ doorstep. Warehouse order picking is the crucial behind-the-scenes process where the floor workers identify and collect the right products from a warehouse to fulfill customer orders.
Irrespective of the size or scale of your business, everyone from ecommerce giants to local retailers needs a streamlined warehouse picking process to keep pace with customer needs.
Types of Picking in Warehouse
Warehouse managers need to identify and implement the right warehouse picking method corresponding to their business model. Several factors help determine which is the best warehouse picking type for your business — the physical size of the warehouse, the types of products you’re dealing with, the total number of warehouse workers available at any given point, and the volume of inventory your warehouse processes.
Warehouse Picking Types:
- Discrete Picking: In terms of complexity, discrete picking is one of the most straightforward warehouse picking types to implement. Pickers retrieve one order at a time, completing it entirely before moving on to the next. This strategy is especially effective for small operations with low SKU count and limited warehouse space.
- Batch Picking: For warehouse batch picking, group multiple orders that use the same SKUs — this way, pickers collect all the items they need for the batch in a single pass without traveling back and forth. Batch picking reduces travel time, improves warehouse efficiency, and boosts productivity when dealing with similar orders. However, it’s not ideal for highly-varied orders because pickers might need to backtrack through the warehouse.
- Zone Picking: For zone picking, also known as pick-and-pass, the warehouse is divided into zones, and pickers are assigned to every zone. Pickers add items from their designated area as each order passes through these zones. Zone picking is highly beneficial for large warehouses with high order volumes because pickers become familiar with their designated zones and navigate efficiently. However, warehouse managers need to proactively manage the warehouse space to prevent congestion in high-traffic zones.
- Wave Picking: Wave picking is conceptually similar to batch picking, where orders are grouped based on predetermined criteria like shipping dates, delivery times, and more. Pickers pick up products in “waves” based on priority and physical location of the items.
- Cluster Picking: Pickers collect items for multiple orders in a single pass, typically utilizing technology like hand-held scanners or pick-to-light systems to ensure accuracy. Warehouse cluster picking is ideal for high-volume e-commerce operations fulfilling orders with several SKUs because pickers can leverage batching while maintaining individual order accuracy.
- Piece Picking: Piece picking involves picking individual items from larger cartons or storage units. It’s more common in operations with a wide variety of SKUs and where orders often contain small quantities of each item. Piece picking offers flexibility but can be time-consuming, especially for frequently picked items.
- Pallet Picking: For pallet picking, the pickers move entire pallets of goods at once, typically using forklifts or pallet jacks. This is the most efficient method for bulk orders or replenishing forward-picking areas in a warehouse.
Common Warehouse Picking Challenges and Solutions
Picking is one of the most important processes in the warehouse. On average, 55% of all the operational costs of a warehouse are dedicated to picking activities. It’s important to be acquainted with some common warehouse picking challenges.
Human Errors in Picking
Warehouse picking processes rely heavily on manual labor, making them inherently susceptible to human errors. Even the best pickers can make mistakes like grabbing the wrong item, miscounting quantities, or using inefficient methods.
While it’s not possible to completely remove the possibility of errors, adopting a technology-driven approach can help reduce overall warehouse picking error rates.
Solutions to Reduce Human Errors in Picking
- Clear Labeling and Organization: Ensure items are clearly labeled and stored logically for easy identification.
- Training and Checklists: Provide pickers with comprehensive training and checklists to reinforce best practices.
- Integrate the Right Technology: Pivot from paper-based methods to digital picklists and real-time order updates.
- Barcode Scanners: Verify each item with a scan to eliminate mispicks and wrong quantities.
- Pick-to-Light Systems: Implement pick-to-light systems to guide pickers to the correct location and order quantity, minimizing errors along the way.
Improper Picking Path
Unoptimized picking paths in warehouses lead to an unrelenting cycle of reduced productivity — long, disorganized routes fatigue pickers, causing them to work slower and be more prone to mistakes. These mistakes then lead to order returns, cancellations, and lost sales, further reducing overall warehouse efficiency.
Solution to Optimize Picking Paths
- Strategic Item Placement: Store frequently picked items together and in easily accessible locations to minimize travel distance.
- Picking Methods: Implement zone picking, wave picking, batch picking, or a combination of these warehouse picking methods based on your order volume and warehouse layout.
- Integrate a WMS: Warehouse management systems analyze your layout, orders, and inventory locations to generate the most efficient picking routes.
- Optimized Slotting: A WMS can suggest the best item placement based on order trends, storage requirements, and available resources to minimize travel.
Poor Space Management in the Warehouse
In the warehouse, space is one of your most valuable assets. Poorly used space means pickers spend more time locating, identifying, and picking the right products, slowing down the entire fulfillment process.
Solution to Optimize Warehouse Space Utilization
- Slotting Optimization: Place high-demand items in easily accessible areas and group frequently ordered items together to shorten picking routes.
- Utilize Vertical Space: Use taller racks and shelving to maximize storage capacity within your existing footprint.
- Leverage Warehouse Picking Software: A WMS can analyze your layout, product sizes, and historical sales data to determine the most ideal placement for your products, especially fast-moving inventory.
- 3D Space Mapping: Specialized warehouse picking tools can help visualize your warehouse, pinpoint space inefficiencies, and identify areas of improvement.
Inaccurate Inventory
Warehouse managers need real-time visibility into the exact location, quantity, and type of products to ensure the right item is picked at the right time. Wrong stock data leads to pickers wasting time searching for items, mis-picks, customer order delays, stockouts, and excess obsolete inventory.
Solution to Solve Inventory Inaccuracy
- Regular Cycle Counts: Schedule frequent physical inventory checks to reconcile stock levels with your system records.
- Double-Check Picking: Implement a verification step where another worker confirms the item and quantity before proceeding.
- Implement a WMS: A WMS integrates barcode scanning or RFID to update inventory in real-time as items are received and picked.
- ERP Integration: Connect your WMS with your Enterprise Resource Planning system for a unified view of inventory movements across sales and procurement.
Poor Picking Visibility
Warehouses that rely on traditional paper-based systems often end up creating information silos. A lack of picking visibility makes it all the more difficult for your warehouse managers to track errors or report on performance metrics. Zebra Technologies estimates that 68% of warehouse operations will prioritize increasing asset visibility, real-time decision guidance, and data-driven performance by 2024.
Solution to Improving Picking Visibility
- Standardized Reporting: Implement regular reports to track picking errors and key performance indicators, even if these are manually gathered at first.
- Adopt a Software-driven Approach: A WMS offers real-time visibility into orders, inventory levels, picker performance, and other key metrics.
- Analytics and Dashboards: Utilize customizable dashboards within your WMS to visualize the most important metrics and immediately spot potential bottlenecks.
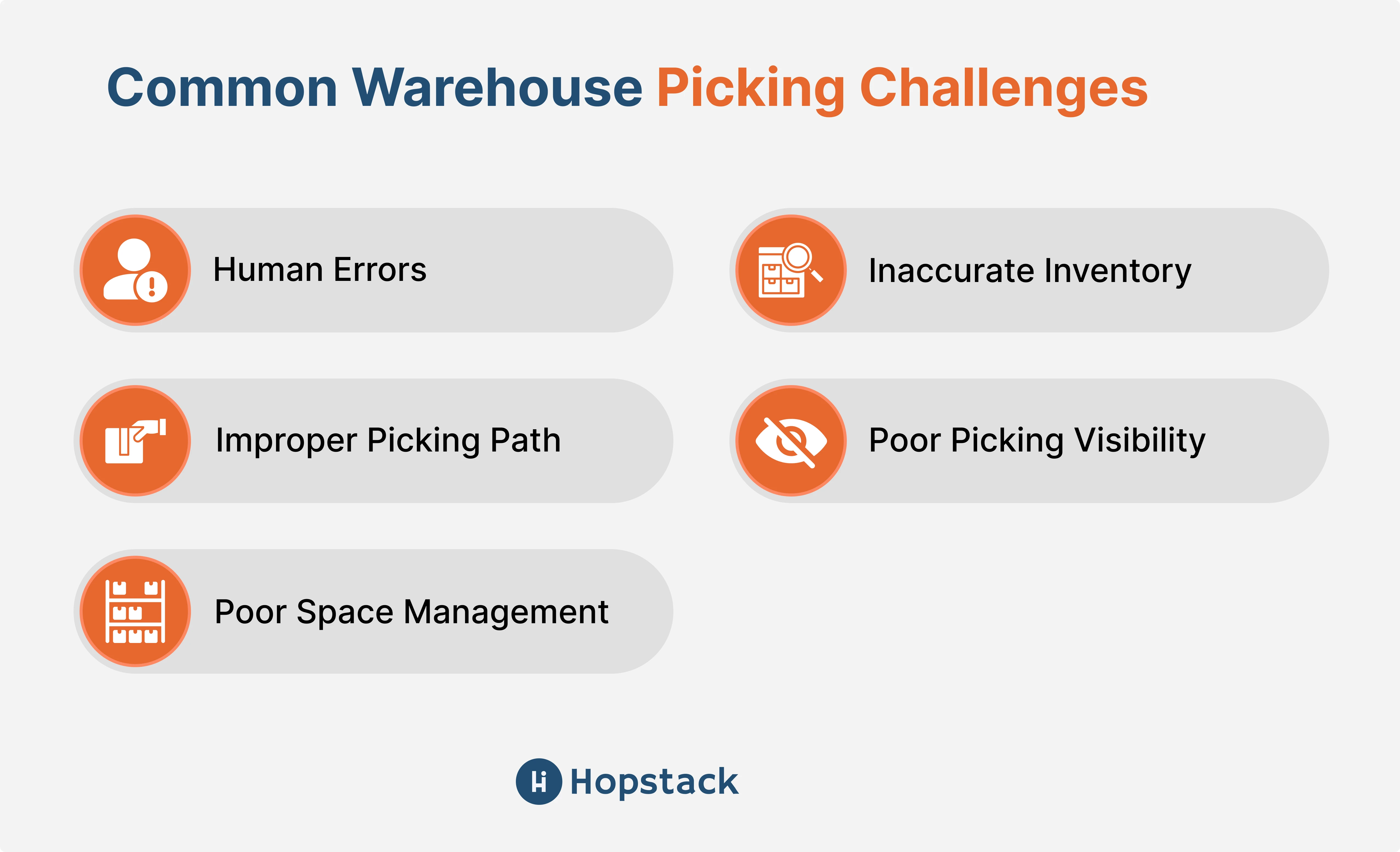
5 Reasons to Automate the Warehouse Picking Process
Automation has become an essential component of a high-functioning warehouse. Using the right technology to augment existing warehouse picking processes can holistically improve overall productivity, efficiency, and resource utilization.
Boosted Accuracy and Efficiency
Automation dramatically reduces picking errors with smart picklists and optimized routing. Warehouse robots and picking systems can verify items with barcodes or RFID tags, ensuring that the right items are selected every time.
Automated picking systems are meant to work in tandem with the pickers on the floor. Smart warehouse picking tools provide an additional layer of verification to the warehouse picking process. Faster picking with fewer errors translates to more orders processed per day and higher customer satisfaction.
Improved Labor Utilization
Automation can handle repetitive, time-consuming tasks like moving pallets, retrieving items from shelves, and transporting goods to packing stations. This frees up your human workforce for more complex or value-added activities, such as quality control, kitting, and customer service.
Additionally, automation can help reduce the strain on your workforce by minimizing physically demanding tasks, improving overall worker satisfaction, and potentially reducing injuries.
Optimized Space Utilization
Automated systems like AS/RS (automated storage and retrieval systems) make the most of your warehouse footprint by utilizing vertical space and denser storage configurations. This allows you to hold more inventory without expanding your physical facility.
Furthermore, automated systems can efficiently store and retrieve goods from high shelves or even create additional storage space by maximizing the use of overhead areas. With warehouse space costs on the upward trend, optimized space utilization directly translates to cost savings — you can potentially avoid the need to lease or purchase additional warehouse space to accommodate your growing inventory.
Enhanced Scalability
Instead of scrambling to hire and train temporary workers, you can leverage automation to handle increased order volume without disrupting your core staff.
For example, every holiday season, the United States witnesses a massive surge in online commerce. The U.S. Postal Service processed an estimated 12 billion packages for the entire holiday season of 2022. Having a tried-and-tested picking system in place is crucial to scale with seasonal demand peaks or sudden growth in your business.
Scalable automation solutions can adapt to your changing needs, allowing you to add or remove picking robots or other automated equipment as your order volume fluctuates. Automation in warehouse picking solutions ensures that you can efficiently meet customer demand without compromising on fulfillment speed or accuracy.
Data-Driven Insights
Automated systems continuously gather valuable data about your warehouse operation. Take a warehouse management system (WMS), for example — it acts as your central nervous system for picking operations gathering granular data on picker performance. This includes metrics like pick times per item, individual picker accuracy rates, and identification of specific bottlenecks that slow down pickers, such as congestion at packing stations or waiting for forklifts.
By continuously collecting and analyzing this data in real-time, a WMS provides valuable insights to drive warehouse optimization. This data enables your warehouse managers to identify areas for improvement, like adjusting picking routes to minimize travel distances, or optimizing inventory placement based on popularity and picking frequency, ultimately boosting efficiency and throughput. A proactive analysis of picking data within the WMS allows you to anticipate potential issues, such as low stock levels or inefficient workflows, before they disrupt fulfillment.
Top Automated Warehouse Picking Strategies
Automated warehouse picking equipment offers an obvious advantage through improvements in efficiency and accuracy. However, these changes will be more tangible for larger operations, compared to smaller warehouses. Businesses should consider possible use cases for warehouse picking optimization and automation to understand when and what technology to implement.
1. Pick-to-Light Systems
Pick-to-light systems use lights and displays at storage locations to guide pickers. The system illuminates the exact location and quantity of the item to be picked. It’s ideal for high-volume, fast-paced picking of individual items (piece picking). The picker can simply follow the light cues, increasing picking speed and accuracy, often with minimal training required.
You should consider implementing pick-to-light systems if you have a steady flow of similar or smaller-sized items. It's less suited for large/bulky items, very low-volume picks, or warehouses with frequently changing inventory layouts.
2. Voice-Directed Picking
Pickers use a headset and microphone to receive audio instructions and confirm picks verbally. Voice-directed picking is a hands-free, eyes-free system that keeps the worker's focus on the task without compromising productivity. The hands-free approach also promotes safety and ease of movement. According to Honeywell, voice-directed picking can reduce the number of errors by 50-90% compared to paper-based operations.
Voice-directed picking is effective for high-SKU environments where pickers travel long distances between locations. It’s less than ideal for noisy environments or when dealing with complex kitting requirements.
3. Robotic Picking Systems
Autonomous mobile robots (AMRs) navigate the warehouse to retrieve items from shelves and bring them to picking stations or transport them to other locations. They can handle large cases or heavy pallets as well.
Robotic picking systems reduce picker travel time and strain, especially in large warehouses. Robots can work continuously and consistently, boosting overall picking capacity. According to Robotics 24/7, the top three factors motivating organizations to implement robotics are:
- To increase flow/throughput
- Address labor availability constraints
- Improve labor productivity
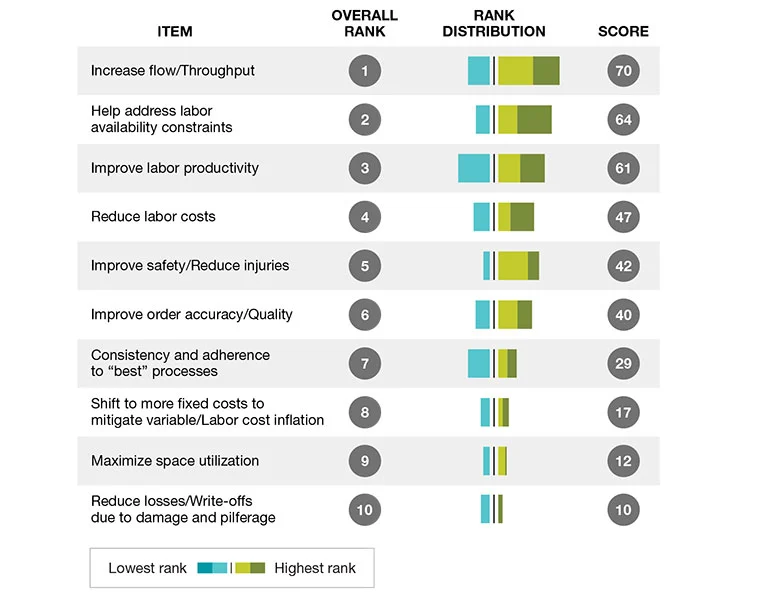
Caption: Biggest factors motiving organizations to pursue robotics for warehouses and distribution centers (Source: Robotics 24/7, Peerless Research Group)
AMRs are excellent for large facilities with high-volume, repetitive picking tasks. However, keep in mind that your warehouse will require adequate space for the robots to navigate and an upfront investment in infrastructure.
4. Vision Picking
Vision picking uses cameras and image recognition software to identify and locate items for picking. You can implement vision picking to augment warehouse pickers or in conjunction with mobile picking robots.
Automated image-guided technology is extremely flexible and offers high levels of warehouse picking efficiency and accuracy. It’s well-suited for mixed-SKU orders and irregularly shaped items, which could be harder for other automated systems to handle.
Consider implementing vision-picking technology if your order profiles involve a wide variety of items that often change.
5. Smart Weight Scales
Smart scales are integrated into picking stations, and weight measurements are used to verify picked quantities. They flag any discrepancies before the order moves further down the line. It adds an extra layer of QC to detect picking errors in real-time, increasing accuracy and reducing order fulfillment costs.
Smart weight scales are best for businesses with high-value items or frequent mis-picks that require an additional quality control layer.
General Considerations for Implementation
As a rule of thumb, ask yourself these questions before investing in any warehouse automation technology.
- Order volume and type: Assess current volume and predict future needs to determine if the potential ROI of automation makes sense. Consider if your orders are standardized or highly variable.
- Warehouse layout: Is your space suitable for fixed systems like pick-to-light, or does it require a more flexible solution like mobile robots?
- Budget: Automation involves upfront costs, so calculate the potential ROI based on labor savings, accuracy improvement, and increased throughput.
- IT Integration: Automated systems need to 'talk' to your WMS and other systems for optimal warehouse picking efficiency. So if you don’t have a WMS yet, that should be your starting point..
How Hopstack Solves Warehouse Picking Challenges
Hopstack tackles picking challenges for a new generation of warehouses with an algorithmic approach that optimizes picking paths and dynamically assigns orders based on picker location. Our platform customizes solutions for each warehouse, generates intelligent picklists, and offers powerful auto-batching to boost efficiency. Hopstack has helped warehouses achieve:
- Increase picking efficiency by up to 99%
- Increase picking rates to up to 250 picks per hour
- Reduce average picking time and distance
- Reduce picking activity wastage
Hopstack's seamless integrations with various picking devices and automation tools future-proof your warehouse, ensuring scalability and adaptability as your operation grows. Contact us today to schedule a demo and discover how Hopstack can transform your warehouse picking processes.