On average, 55% of all the operational costs of a warehouse are dedicated to picking activities. And most of it is gone in wasted time and efforts.
Order picking may look simple but is deceivingly complex and becomes even more difficult as warehouses deal with larger volumes of goods. Choosing the right picking strategy and the right personnel are not the only things involved in setting up the picking workflow in a warehouse. Warehouse managers must look at processes holistically and deal with challenges as they arise. The major challenges that arise with picking are:
- Wastages in terms of time, distance traveled, and costs
- Congestions and traffic in the warehouse involving pickers
- Complex warehouse layouts
- Inaccurate inventory placement
- Near-zero visibility of picking operations
Hopstack understands these challenges and we have actively worked towards creating a product that can tackle these challenges. Read further to know more about how Hopstack tackles new-age picking challenges in a warehouse.
Why is warehouse order picking so complex?
Order picking is one of the simplest, most straightforward tasks in a warehouse but exponentially increases in complexity with larger volumes. The main challenges associated with picking are as follows:
- Time-consuming - Picking is a highly time-consuming activity. For orders with multiple line items, pickers often have to travel a considerable distance to pick all items in an order.
- Error-prone - Pickers could pick the wrong item or even misallocate products into the wrong tote bags and cause a logistic error that can easily carry forward to the end customer.
It is essential to ensure that the picking processes are optimized for speed and accuracy. By optimizing order picking processes and actions, businesses can avail:
- Faster order processing and fulfillment times
- Maximize resource and personnel utilization
- Save time and money
How Hopstack approaches picking
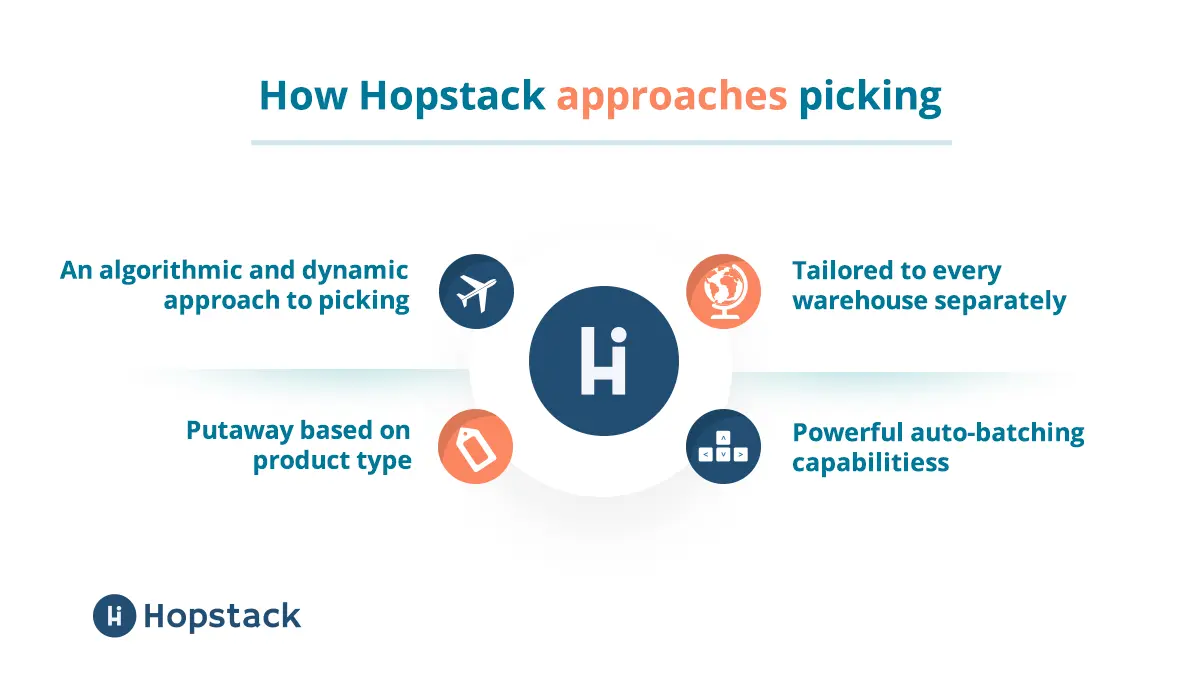
An algorithmic and dynamic approach to picking
Hopstack’s picking modules use purpose-built algorithms to maximize picking efficiency and reduce wastage associated with picking-related activities. These algorithms create picklists based on which items are nearest to the picker and accurately pinpoint the shortest path to complete picking all the line items for an order. The algorithms calculate the shortest path between items in an order and compare various permutations to figure out the shortest path that can be taken.
Apart from taking an algorithmic approach, Hopstack’s picking module also dynamically prioritizes the assignment of picking activities. This means that the pickers are assigned new orders by taking their current location into consideration. This minimizes the travel time for pickers drastically.
Both of these combined result in unparalleled efficiency increases. One of Hopstack’s clients reported a 300% increase in individual picking efficiency and increased their picking rate from 70 picks per hour to 250 picks per hour within one month of implementing Hopstack’s warehouse platform. To read more about how Hopstack streamlined the fulfillment processes and boosted key north star metrics for a third-party logistics company, here is the case study.
Tailored to every warehouse separately
Each instance of Hopstack’s platform can be customized to suit the warehouse it is being deployed in. The customizations may include:
- Workflow changes - Warehouse managers can make changes to the workflow by adding or removing one or more steps in the fulfillment workflow. These can be configured using the workflow management module as well as the rule engine.
- Integrations - The Hopstack platform possesses a wide variety of integrations for over 50 software and hardware providers. However, in the off-chance that a client’s integrations are not currently available, our deployment team will work with the client to understand their needs and create a tailored integration solution for them.
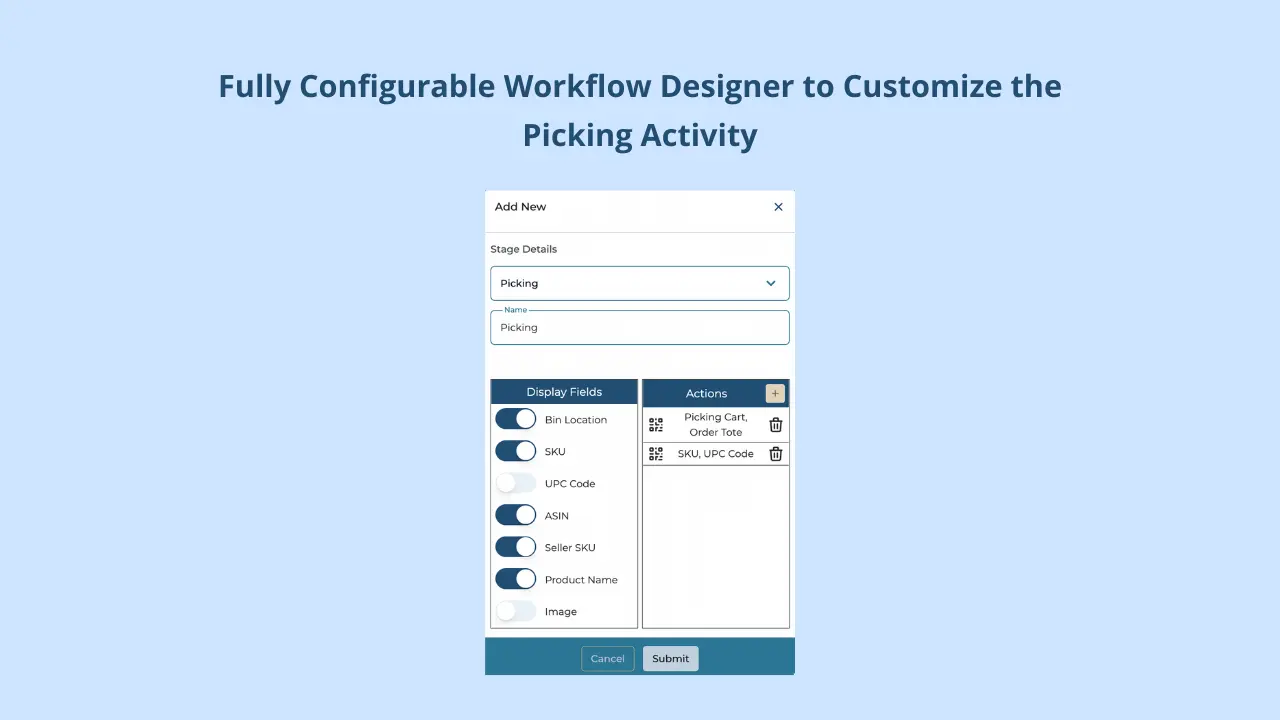
Generate smart picklists
The Hopstack picking module intelligently generates smart picklists. These lists are generated for each picker in the warehouse based on multiple criteria. These include but are not limited to:
- Details of which orders are batched
- Line items assigned to each order
- The relative distance between each line item
- The relative distance between the picker and the first item
The platform then automatically arranges the line items in the picklist in such a way that it reduces travel time and distance to the minimum. It also takes other pickers into consideration and ensures that there is no congestion or traffic in any individual’s path by using thermal scanners to scan heatmaps of the warehouse based on human traffic.
Powerful auto-batching capabilities
The Hopstack platform can automatically batch similar orders together based on historical data. The batching algorithm will parse through past order data and evaluate which orders may need similar treatment (in terms of packing, handling, preparatory steps, etc.). The batches created in this step will be evaluated by the platform’s optimization models and provide optimal batches to the picker. This action can also be simulated first by the warehouse manager to evaluate the compliance of the created batches with warehouse practices. To know more about how rule-based smart batching works in the Hopstack platform, check out this article.
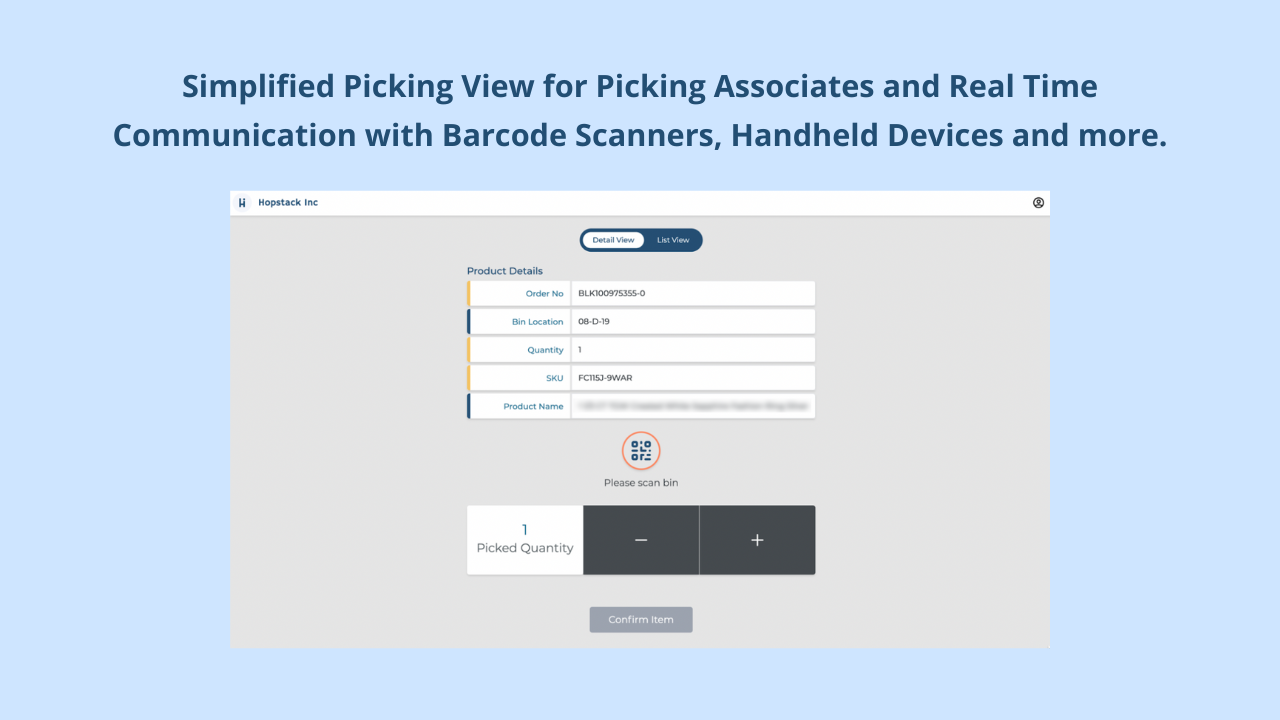
Hopstack recommended best practices for managing order picking
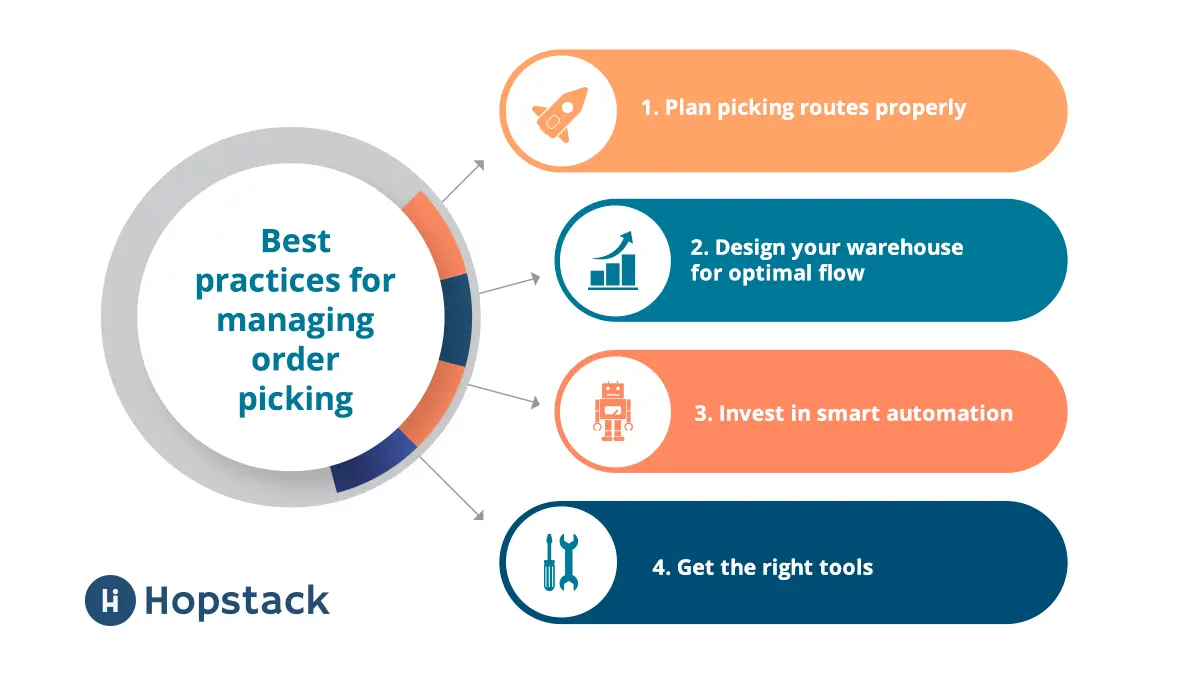
Plan picking routes properly
Pickers' routes while performing their day-to-day activities should be carefully planned out to avoid backtracking. They should also be revised periodically to address any bottlenecks that arise as the organization scales. Warehouse management systems like Hopstack intelligently plan the arrangement in which the line items of an order should be picked to avoid bottlenecks and traffic in the warehouse.
Design your warehouse for optimal flow
Each area in the warehouse should be logically placed such that it follows the prevalent workflow in the warehouse. For example, if the warehouse follows a traditional workflow (Receiving > Storage > Picking > Sorting > Packing > Shipping) then the warehouse areas should ideally be located in the same order to allow for an assembly-line style flow of orders.
However, if the warehouse follows a non-traditional workflow, then the warehouse management systems must be able to understand the custom workflow and implement it. Hopstack allows warehouse managers to customize workflows for the entire warehouse or even for specific SKUs or bundles based on rules set by the organization.
.png)
Invest in smart automation
Smart warehouses are increasingly becoming prominent due to their high standards of efficiency, safety, and high throughput. Investing in automation should not solely be a C-suite endeavor, rather it should include the managers and supervisors on the floor so that their needs are acknowledged and fulfilled. Moreover, it is necessary to ensure that these automation systems can integrate well with the warehouse management system to use their full potential. Hopstack has an integration library of 50+ software and hardware OEMs, most of which can be set up instantly. This means that Hopstack-enabled warehouses are smarter, right from day 1.
Get the right tools
Even if the warehouse has the best staff which has been trained to the highest standards, the lack of correct, purpose-built equipment is always a major bottleneck. Warehouses can choose to integrate and get a wide variety of tools to increase picker productivity. These may include simple devices like barcode scanners all the way up to conveyor belt systems and mobile robots.
Warehouses may also choose to implement a goods-to-person strategy and invest in carousel belt systems, AS/RS systems, and so on. This helps reduce the potential for human error and reduces picker fatigue while improving picking efficiency exponentially. Hopstack seamlessly integrates with multiple picking device OEMs like ProGlove, Zebra Robotics, Handplus Robotics, and Honeywell, among others.
Key Benefits
The Hopstack picking module with its platform-wide integrations results in multiple benefits such as:
- Increase picking efficiency by up to 99%
- Increase picking rates to up to 250 picks per hour
- Reduce average picking time and distance
- Reduce picking activity wastage
The Hopstack warehouse picking module eliminates redundancies and increases warehouse picking efficiency in the warehouse. It also tackles traditional picking challenges using a digital, new-age approach to ensure that your warehouse is keeping up with the latest practices. The platform also helps warehouse managers to keep their options open for future expansion through features like the powerful integrations library. Finally, the high scalability of the platform ensures that the platform grows at the same pace as your organization, always.
To learn more about how Hopstack can help improve your current picking processes and activities, get in touch with us by filling out the form.