In a warehouse, efficiency is everything - and small operational details can make or break that efficiency. One often overlooked but absolutely critical component is warehouse labeling. Whether you're managing a small storage area or a multi-zone fulfillment center, the way you label locations, bins, pallets, and products directly impacts inventory accuracy, picking speed, and order fulfillment rates.
Warehouse labeling isn’t just about slapping stickers on shelves - it’s a foundational system that supports inventory visibility, traceability, and automation. In this blog, we’ll break down everything you need to know about warehouse labeling: what it is, why it matters, how to do it right, and how to avoid costly mistakes.
What Is Warehouse Labeling?
Warehouse labeling is the process of assigning and applying readable labels - such as barcodes, QR codes, RFID tags, or alphanumeric identifiers - to physical locations and inventory within a warehouse. These labels serve as precise identifiers for racks, bins, shelves, pallets, and individual products, enabling warehouse staff and systems to locate, track, and manage goods with speed and accuracy.
An effective warehouse labeling system ensures that every item and storage location is easily scannable and logically organized, reducing human error and improving inventory control. Labels are typically used in combination with warehouse management systems (WMS), allowing for real-time updates and automated data capture during receiving, picking, packing, and shipping processes.
There are different types of warehouse labels:
- Barcode Labels: Barcode labels are cost-effective and can be scanned with a barcode scanner to identify a product or location. When combined with text labeling, barcode labels ensure readability for both man and machine.
- RFID Labels: Radio Frequency Identification (RFID) labels use small radio transponders to transmit information to a reader even from a distance and without line-of-sight.
- QR Code Labels: Similar to barcode labels, QR (Quick Response) codes can hold a lot of information and can be read using a smartphone camera. QR code labels are two dimensional while barcode labels are single dimensional.
- Magnetic Labels: Magnetic labels have a magnetized back, making them easy to apply, remove, and reposition on metal surfaces.
- NFC Labels: Near Field Communication (NFC) labels operate similarly to RFID labels, but require greater proximity (usually a few centimeters) to the reader.
- Holographic Labels: These are used for high-security items. They include a 3D hologram that can't be duplicated, offering protection against counterfeiting.
Depending on the business model and the types of goods, labels include purpose-driven information like:
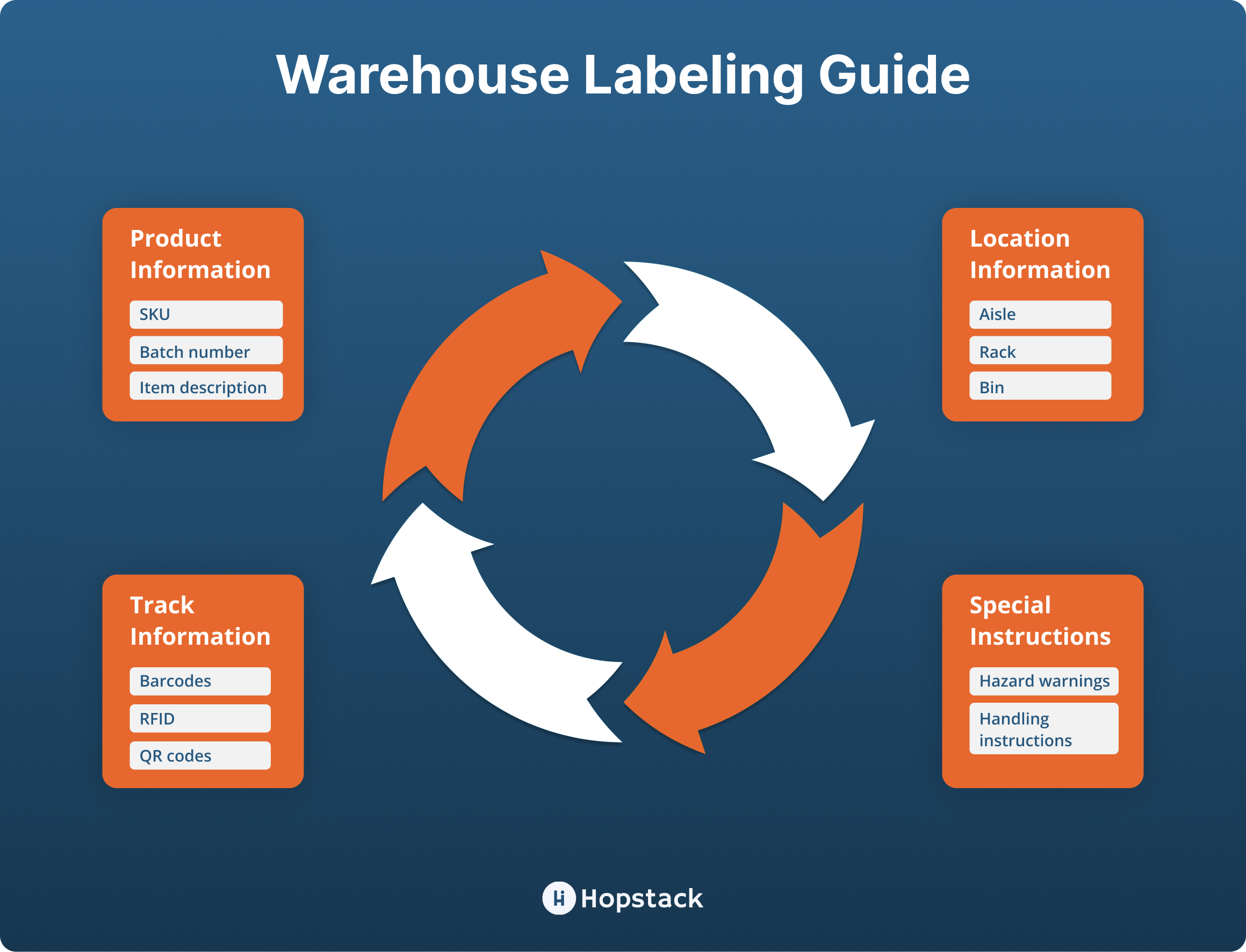
Warehouse labels, when combined with a warehouse management system, can help create a cohesive and safe warehouse layout for the workers.
What is a Warehouse Labeling System?
A warehouse labeling system is a combination of the hardware (labels, printers, scanners) and software (warehouse management system) needed to implement and operate labels within the warehouse layout. Digital warehouse labeling systems can seamlessly integrate with WMS or ERP software to automate and improve inventory tracking, space utilization, and picking and packing processes.
Based on the reliance on manual processes or advanced, automated systems, there are various types of warehouse labeling systems:
- Manual Warehouse Labeling Systems: Labels are usually created from a printer and manually applied to goods, pallets, and storage locations. Manual systems are feasible only in smaller operations that don’t handle a significant volume of orders or unique SKUs.
- Automated Warehouse Labeling Systems: Automated systems include industrial warehouse label printers that can print and apply labels without human intervention, or conveyors and robotic systems that move goods past a label applicator. With warehouse automation systems, these systems can interface directly with a WMS to automatically print labels based on incoming data about the goods.
- Digital Warehouse Labeling Systems: RFID and NFC fall under this category as they use digital technology to store and transmit information. These labels contain printed information and digital data that can be read by scanners. Digital warehouse labeling systems can integrate with a centralized management system to manage and encode digital labels.
- Integrated Warehouse Labeling Systems: These systems are fully integrated with other warehouse systems, such as the WMS, ERP, or TMS (Transportation Management System). They can automatically generate labels based on data from these systems, and the scanned data automatically feeds back into the system.
- Dynamic Warehouse Labeling Systems: These systems use technology like electronic shelf labels (ESL), which are digital, wireless display units that can be updated remotely. They are majorly used in applications where product locations change frequently, as they can be updated instantly without physical intervention.
The most appropriate labeling system for a particular warehouse depends on multiple factors — warehouse layout, size, volume and variety of goods, existing technology infrastructure, and available budget. Large warehouse operations will benefit from greater automation and integration. However, the large initial investment might not be the best option for smaller warehouse operations just starting out.
Key Areas That Require Labeling
1. Racks and Shelves
Each rack and shelf should have a unique identifier, often using alphanumeric codes or barcodes. These labels guide warehouse workers and WMS software to the exact location of stored items. Proper shelf labeling reduces search time and picking errors significantly.
2. Bins and Totes
Bins are commonly used for storing smaller items or broken-case inventory. Labeling each bin with scannable codes ensures quick identification and reduces the risk of SKU misplacement. Durable labels are key, especially in high-turnover or high-touch areas.
3. Pallets
Pallet labels often include SSCC codes or serialized barcodes for tracking large quantities or grouped items. These labels link physical inventory to digital records in your WMS or ERP system. They’re essential for managing bulk stock and ensuring traceability during shipping.
4. Product Packaging / SKUs
Each individual product or case should have a SKU label with a barcode or QR code. This enables fast picking, cycle counting, and product-level traceability. It's especially critical in industries requiring compliance or lot-level control.
5. Aisles and Floor Locations
Labeling aisles and floor locations with overhead signs or ground markings helps streamline navigation. These labels guide pickers and forklift operators, reducing travel time across large facilities. Consistent naming conventions help prevent misroutes and congestion.
6. Shipping and Receiving Zones
These areas should have clear visual identifiers such as dock numbers, staging area labels, or bay signs. Proper labeling reduces loading errors and supports smooth inbound/outbound workflows. It also facilitates real-time updates to inventory during check-in/check-out.
Types of Warehouse Labels
1. Barcode Labels
The most common type, barcode labels come in 1D and 2D formats for shelves, bins, products, and more. They offer high-speed, accurate data capture with simple scanning hardware. Proper placement and print quality are essential for reliable scans.
2. RFID Tags
RFID tags use radio waves to transmit data, allowing multiple items to be scanned simultaneously without direct line-of-sight. They're ideal for high-value or serialized inventory that requires fast, hands-free tracking. Though more costly, RFID enhances automation and visibility.
3. Color-Coded Labels
These visually categorize inventory by priority, zone, category, or handling requirements. Colors make it easier for workers to distinguish products or locations at a glance. When paired with barcodes, they combine visual speed with scan accuracy.
4. Floor Labels and Signage
Made from tough, industrial-grade materials, these labels mark zones, walkways, and staging areas. They help prevent confusion in busy environments and direct traffic flow. Floor signage is especially useful in large or multi-zone warehouses.
5. Magnetic and Removable Labels
Magnetic or repositionable labels allow for flexible reconfiguration of shelving and racks. They're perfect for dynamic warehouses that frequently change inventory layouts. These labels are easy to update without damaging surfaces or requiring reprints.
6. Hazard and Regulatory Labels
These include warnings, handling instructions, or compliance data for hazardous or sensitive goods. They ensure the warehouse meets OSHA, GHS, or industry-specific safety regulations. Proper placement helps prevent accidents and supports audits.
Why Effective Labeling in Warehouse is Important?
Accurate labeling is crucial to efficiency, reliability, and productivity in warehouse operations. With warehouses moving increasing volumes of orders, warehouse labels offer an easy way to minimize errors and facilitate product traceability at all points. The benefits of warehouse labeling include:
Precise Inventory Tracking Across Warehouse Locations
According to research by Cushman and Wakefield, warehouse development is trending toward units ranging from 50,000 to 200,000 sq ft in size. The massive expanse of the warehouse layout makes it almost impossible to navigate without a guidance system.
A proper warehouse labeling system enables accurate inventory tracking of every item, making it possible to narrow down the exact location. It helps reduce misplaced or lost inventory, thus minimizing the chance of stockouts or overstocking. Greater SKU visibility for warehouse managers, pickers, and packers translates to improved productivity and better business intelligence (BI) reports.
Enhanced Labor Productivity
Correctly labeled products and storage locations help warehouse workers locate items and identify picking and putaway routes. Compared to manual processes, warehouse labeling systems allow for significantly smarter picking, packing, and replenishment workflows. If a warehouse uses scanning technology, such as barcode scanners or RFID, workers can simply scan labels instead of needing to write down or manually enter information.
Elimination of Errors in Inbound and Outbound Processes
Research by Datalogic states that a typical warehouse has an annual inventory error value of $195,000. Warehouse labeling adds another additional layer of protection against errors in inbound and outbound processes. Accurate labeling ensures the correct items are received from suppliers, put away in the appropriate storage locations, picked for orders, and shipped to the right customers. The additional oversight significantly reduces the chance of errors in both inbound and outbound processes, leading to improved order accuracy and customer satisfaction.
Elimination of Manual Data Entry
With comprehensive labeling and scanning technology, you can automatically enter product information into a WMS, eliminating the need for manual data entry. This speeds up data collection, reduces errors, and ensures more accurate record-keeping.
Improved Safety for Warehouse Personnel
Proper labeling can contribute to a safer warehouse environment for floor workers. For example, you can use labels to mark hazard zones, indicate the correct handling procedures for certain goods, or show the maximum load capacity of racks. Automation and warehouse labeling systems can work in tandem to prevent accidents and improve worker safety.
Facilitated Quality Control
Labels contribute to the quality control process by enabling the tracking of batches or lots, indicating the date of production or expiration, or showing whether an item has passed inspection. The written record helps warehouse managers quickly identify and isolate any quality issues.
Better Forecasting and Planning
With accurate inventory tracking through labeling, businesses can gather data that aids in demand forecasting and planning for future needs. Knowing which product is at what stage of the fulfillment pipeline is the foundation for efficient purchasing and production decisions.
Different Labels Required for Warehousing Activity
Depending on the type, warehouse labels facilitate various activities across the floor. Below we have singled out a few of the important functions of warehouse labels.
Most warehouses will use a combination of these warehouse labels to guide the flow of goods and information. Together, they act as a real-time guide to navigating and accessing the warehouse layout.
Implementing a Warehouse Labeling System: Step-by-Step
Rolling out a warehouse labeling system may seem daunting, but with the right process, it becomes a high-ROI investment in operational efficiency. Whether you're setting up a new facility or upgrading an outdated system, follow these structured steps to get it right:
Step 1: Assess Your Warehouse Layout and Inventory Flow
Before implementing a labeling system in warehouse, it's crucial to fully understand your warehouse layout. This includes not only the physical structure and arrangement of the space but also the flow of goods and activities. Consider factors like the types of goods stored, the size and weight of items, the methods used for picking, the storage equipment used, and so on. This will help you decide where labels should be placed and what information they should include.
Step 2: Choose the Right Labels for Your Environment
The labels used should be suitable for the environment and the specific application. For example, labels for outdoor storage areas should be weather-resistant, while labels for freezer storage should be able to withstand low temperatures. The labels should also be compatible with your scanning equipment if you use barcode scanners or RFID technology. In terms of size and color, the labels should be visible and easy to read from a reasonable distance.
Step 3: Define a Standardized Labeling Convention
The labeling system should be logical and consistent to make it easy for workers to understand and use. This includes using a consistent format for the information on labels and a logical scheme for assigning location labels. For example, you might label aisles, racks, shelves, and bins with a combination of numbers and letters that indicate their position within the warehouse.
Also, consider how the labels will be sequenced - for instance, whether you want to sequence your locations in a way that optimizes the pick path. It’s always logical to number shelves from the ground up; it leaves more room for vertical expansion.
Step 4: Print and Apply Labels Carefully
Use industrial-grade label printers and proper adhesives to ensure durability and readability. Place labels at consistent heights and angles to allow quick scanning, whether by handheld devices or automated systems. Avoid placing labels where they may be obscured by products or damaged by handling.
Step 5: Integrate Labels into Your Warehouse Management System (WMS)
Your labeling system should be fully integrated with your WMS software. This allows for real-time tracking of inventory and locations, automatic printing of labels based on incoming or outgoing goods, and other advantages.
To begin with, define the data fields that need to be captured on the labels and ensure these are compatible with your WMS. This may include data such as SKU numbers, product descriptions, lot numbers, location identifiers, and so on. Once you’re done, set up data mapping to ensure data flows correctly between systems, configure label printers to work with the WMS, and set up any necessary hardware like barcode scanners or RFID readers.
It might take a minute to test, monitor and make the necessary adjustments, but it’s essential to the success of mid to large-sized warehouse operations.
Step 6: Staff Training for Use of Warehouse Labels
Comprehensive staff training is essential to understand and correctly use the new labeling system. This should include not only how to read and apply labels, but also how to use any new technology or software involved, such as scanners or label printers.
Keep in mind that staff training should not be a one-time event. Regular refresher courses can help ensure that staff members retain their knowledge and stay up-to-date with any changes or updates to the system.
Step 7: Test the System Before Going Live
Before full rollout, conduct a pilot in a single zone or with a small team. Test scanning accuracy, label durability, and WMS syncing. Make adjustments based on feedback — for instance, repositioning hard-to-scan labels or refining location codes.
While the exact practices will differ based on industry and product specifications, these are more along the lines of a guideline for proper implementation. With the right design, intent, and execution, you can considerably improve efficiency and streamline warehouse processes at all points of the fulfillment journey.
Next Steps in Warehouse Labels
Running a high-functioning warehouse is a lot of work, especially for mid to large-sized operations. Managers have to continuously keep tabs on a lot of moving elements while pickers and packers have to effectively navigate the warehouse layout. A warehouse labeling system simplifies inventory model tracking and improves productivity through real-time guidance across warehouse locations.
While printing and implementing warehouse labels from scratch can be a major task, the improvement in warehouse efficiency makes it worth the effort. A warehouse labeling system can integrate with the existing WMS to significantly extend visibility across inbound and outbound operations, leading to reduced errors and greater customer satisfaction.
How do I handle labeling in a multi-level racking system?
Use vertical position indicators (e.g., Level 1, Level 2) as part of your labeling convention. Color-coding levels or using vertical signage helps workers quickly identify pick faces. Ensure labels are placed at eye level where possible to reduce scanning friction.
Is color coding a best practice for warehouse labeling?
Color coding is highly effective for visual management — especially in large, fast-paced environments. You can assign colors by zone, product category, priority, or handling requirement. Just make sure it’s standardized and documented in training materials.
How does labeling support compliance in regulated industries?
Proper labeling ensures traceability, batch tracking, and audit readiness — especially in industries like food, pharma, and electronics. Compliance labels (e.g., GHS, FDA, ISO) must meet specific formatting, content, and placement requirements to pass inspections.
FAQs
What should be labeled in a warehouse?
Key items to label include racks, shelves, bins, pallets, SKUs, floor locations, and shipping/receiving areas. Every location where inventory is stored or moved should have a clear, scannable label. This enables accurate tracking and minimizes fulfillment mistakes.
What type of labels are best for cold storage or freezer environments?
Use freezer-grade or cryogenic labels with strong adhesives and moisture resistance for cold environments. These labels are designed to withstand condensation and temperature fluctuations without peeling or smudging. Thermal transfer labels with protective coatings are often preferred.
How do I create a warehouse location labeling system?
Start by mapping your warehouse zones (aisles, racks, bins). Then, create a structured naming convention — for example, Aisle 01, Rack A, Shelf 02 = A01-RA-S02. Ensure consistency and match these codes in your WMS or inventory system for real-time synchronization.
How often should warehouse labels be replaced or updated?
Labels should be checked regularly — at least quarterly — for wear, damage, or fading. Update labels when inventory layouts change or if scanning issues occur. A proactive labeling audit process can prevent disruptions and maintain data integrity.
How can I make my warehouse labels scannable from a distance?
Use larger font sizes, high-contrast colors, and retroreflective materials for long-range scanning. Position labels at consistent heights and angles, especially on high racks. Long-range barcode scanners or cameras can also help improve read accuracy.
What is the difference between static and dynamic labeling in warehouses?
Static labeling refers to permanent labels for fixed storage locations (like shelves or aisles). Dynamic labeling is used for inventory that changes location frequently, such as pallets in a staging area. Many modern WMS platforms support both to accommodate flexible operations.
Can I use QR codes instead of barcodes in my warehouse?
Yes. QR codes offer more data capacity and can store additional info like batch numbers, expiry dates, or product details. However, they require compatible scanners and might be overkill for simple item/location tracking unless you need that extra data.