In the ever-growing logistics and supply chain industry, businesses often make critical decisions regarding order fulfillment. The biggest of all: should they entrust their supply chain to a third-party logistics (3PL) provider, or should they opt for an in-house fulfillment method? This article delves into the nitty-gritty of the 3PL vs in-house fulfillment, exploring the pros and cons of each method and the factors one must consider before zeroing in on the apt method for their business.
What is 3PL fulfillment?
3PL fulfillment refers to the outsourcing of order fulfillment and logistics functions to a third-party logistics (3PL) provider. In this arrangement, businesses entrust their warehousing, packing, shipping, and often other supply chain operations to an external partner, the 3PL provider. The goal is to leverage the expertise and infrastructure of the third party to streamline and optimize the process of getting products from the point of origin to the end customer.
Key components of 3PL fulfillment
- Warehousing: 3PL providers maintain warehouses or distribution centers where they store the inventory of client businesses. These facilities are strategically located to facilitate efficient distribution through 3PL WMS.
- Order Picking and Packing: When a customer places an order, the 3PL provider is responsible for picking the items from the warehouse shelves, packing them securely, and preparing the order for shipment.
- Shipping and Transportation: The 3PL providers will manage the transportation of goods from the warehouse to the end customer. This includes choosing the most cost-effective and timely shipping methods, managing carriers, and tracking shipments.
- Returns Processing: The main 3PL advantage is that in many cases, 3PL providers also handle the processing of product returns, managing the reverse logistics process and ensuring that returned items are properly restocked or disposed of.
- Technology integration: Many 3PL fulfillment providers use advanced technologies such as warehouse management systems (WMS) and order management systems (OMS) to automate and optimize their processes, providing real-time visibility into inventory levels, order status, and shipment tracking.
Pros and Cons of Using 3PL Fulfillment
Outsourcing logistics has become a key strategy for modern retailers and brands. The global 3PL market size is estimated to be 1.29 trillion USD in 2024. These numbers underline the fact that worldwide, many businesses are now turning towards 3PL for fulfillment for multiple reasons, such as flexibility to scale operations, cost efficiency, and the ability to focus on core business activities without the burden of managing complex logistics.
However, this fulfillment model also comes with its own set of cons. Here are the advantages and disadvantages of outsourcing fulfillment to a 3PL.

Advantages of outsourcing fulfillment to a 3PL
Outsourcing fulfillment to a Third-Party Logistics (3PL) provider is a strategic approach that offers businesses several advantages. Here are some of the advantages of using a 3PL for fulfillment:
Access to expertise
3PL providers often specialize in logistics and supply chain management. By outsourcing fulfillment to a 3PL, businesses can tap into the expertise of professionals who understand the intricacies of warehousing, inventory management, and comprehensive order fulfillment. This expertise can lead to more efficient processes, cost savings, and better customer experience.
In a logistics survey, 81% of respondents who utilize 3PL services stated that using third-party logistics providers significantly enhanced their ability to cater to customer needs effectively.
Reach a wider audience
3PLs often have a strategically located network of distribution centers. What’s more, these distribution centers may be spread across different regions or even globally, facilitating faster and more cost-effective shipping to customers in various locations. Additionally, the ability to access multiple fulfillment centers also helps reduce shipping costs and transit times.
No additional investment into infrastructure and labor
Outsourcing fulfillment to a 3PL eliminates the need for businesses to invest in their own warehouse facilities, equipment, and additional labor. This can result in significant cost savings, especially for smaller or growing businesses that may not have the capital to invest in a comprehensive logistics infrastructure.
Seamless connection to sales channels
3PLs often integrate with various ecommerce platforms and other sales channels. This integration streamlines the order fulfillment process by automatically syncing inventory levels, processing orders, and updating tracking information.
Focus on core competencies
By outsourcing fulfillment to 3PLs, businesses can concentrate on core competencies to enhance overall business efficiency and effectiveness. For example, businesses that are in their early stage can dedicate more time and resources to strategic planning, innovation, and market positioning and let the logistics and fulfillment be in capable hands.
Scalability
When compared to the in-house fulfillment method, 3PLs provide businesses with the flexibility to scale operations up or down based on fluctuations in demand. The ability to scale operations quickly enables businesses to adapt to changing market conditions, respond to customer demands, and remain competitive.
Additionally, during the peak season, this agility is particularly valuable, allowing businesses to adjust resources accordingly without the fixed costs of maintaining excess capacity.
Access to the latest technology
Most 3PLs invest in state-of-the-art logistics technologies, such as Warehouse Management Systems (WMS) and transportation management systems. Businesses can leverage these technologies and increase supply chain efficiency and accuracy.
.png)
Faster delivery
Faster and reliable delivery plays a crucial role in ecommerce. According to Statista, 41% of global shoppers said they hoped to receive their orders within 24 hours. With strategically located fulfillment centers, 3PLs can offer expedited shipping options such as same-day, one-day and two-day delivery.
Disadvantages of using 3PL for fulfillment
While 3PLs can bring efficiency and cost savings to businesses, there are also potential disadvantages that companies should consider before outsourcing their fulfillment operations. Here are some of the disadvantages of using 3PLs for fulfillment:
Loss of complete control
One major drawback of relying on a 3PL is the potential loss of control over critical aspects of your supply chain. As a business owner, you might find it challenging to oversee and manage the day-to-day operations, leading to a disconnect between your brand and the fulfillment process.
Communication challenges
Effective communication is vital in any business relationship, and when outsourcing fulfillment, there's a risk of miscommunication between your company and the 3PL. This can result in errors, delays, and customer dissatisfaction, especially if expectations are not clearly communicated and understood.
Over dependency
Relying on a 3PL means your business depends on an external entity for key logistics functions. If the 3PL faces financial instability, operational problems, or leadership changes, your supply chain may be adversely affected, leading to disruptions in fulfillment services.
Pricing concerns
While outsourcing fulfillment to a 3PL can lead to cost savings, it's essential to carefully evaluate the pricing structure. Some 3PLs may have hidden fees, and costs could escalate if you require additional services or unexpected changes in your business volume.
What is in-house fulfillment?
In-house fulfillment refers to managing and executing order fulfillment processes within a company's facilities and resources, as opposed to outsourcing these tasks to a third-party logistics (3PL) provider. In this model, the company retains direct control over various aspects of the supply chain, including inventory management, order picking and packing, and shipping.
Pros and cons of in-house fulfillment
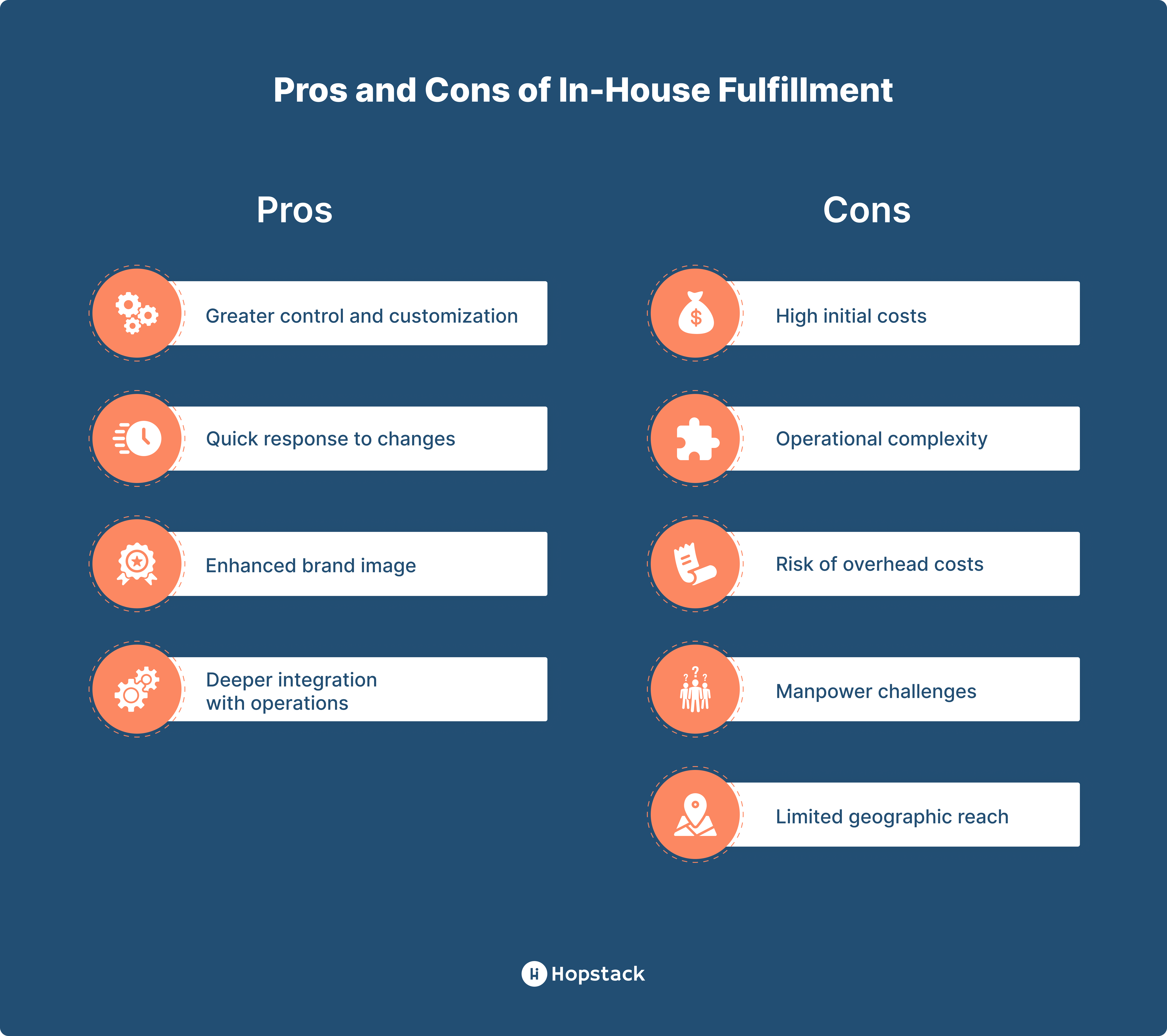
According to a Capital One study, 40% of retailers use their own in-house fulfillment process to fulfill orders. Like 3PL fulfillment, the in-house fulfillment model has its fair share of advantages and disadvantages. Let's now look at them:
Advantages of In-house Fulfillment
In-house fulfillment, where a company manages its own order fulfillment processes internally, provides businesses with a hands-on approach to their supply chain operations. While it requires substantial investments in infrastructure and resources, this model comes with distinct advantages that cater to specific business needs and objectives. Here are some of the advantages of in-house fulfillment:
Greater control and customization
One of the primary advantages of in-house fulfillment is the level of control businesses maintain over their supply chain processes. Companies can customize their fulfillment operations to align precisely with their unique requirements, ensuring a tailored approach that reflects the brand's values and customer expectations.
Quick response to changes
Businesses with in-house fulfillment capabilities can swiftly adapt to changes in market conditions, customer preferences, or unexpected disruptions. The agility provided by internal management allows for rapid adjustments to inventory levels, order processing workflows, and shipping methods without relying on external partners.
Enhanced brand image
Managing fulfillment in-house enables companies to maintain a consistent brand image throughout the entire order fulfillment journey. From the warehouse to the customer's doorstep, businesses can ensure that each touchpoint reflects their brand values, leading to a more cohesive and positive customer experience.
Deeper integration with operations
In-house fulfillment fosters a seamless integration with other aspects of a company's operations, such as manufacturing, marketing, and customer service. This alignment can result in improved communication and collaboration between different departments, leading to greater overall efficiency and a unified business strategy.
Disadvantages of In-house Fulfillment
Although in-house fulfillment has several advantages, it also poses several challenges and disadvantages. Here are some of the disadvantages that businesses will face when choosing in-house fulfillment:
High initial costs
Establishing in-house fulfillment operations involves significant upfront costs. Companies need to invest in warehouse facilities, technology, inventory management systems, and a skilled workforce. For small and growing businesses, these initial expenses can strain financial resources.
Operational complexity
Managing fulfillment in-house can be operationally complex. Businesses need to handle various tasks, including inventory management, order processing, packing, and ecommerce shipping. The complexity of these operations can lead to challenges in maintaining efficiency and meeting customer expectations, especially during peak periods.
Risk of overhead costs
Maintaining and operating an in-house fulfillment center comes with ongoing overhead costs, such as facility maintenance, utilities, and labor expenses. If order volumes fluctuate or decline, businesses may struggle to absorb these fixed costs, impacting overall profitability.
Manpower challenges
Recruiting, training, and retaining a skilled workforce for in-house fulfillment can be a constant challenge. High turnover rates, seasonal fluctuations, and the need for specialized skills in logistics and warehouse management can contribute to staffing issues, affecting the overall efficiency of operations.
Limited geographic reach
In-house fulfillment may limit a company's ability to efficiently serve customers in different geographic locations. On the other hand, establishing multiple fulfillment centers to cover diverse markets can be costly and logistically challenging compared to leveraging the broader network offered by some third-party logistics providers.
Factors to consider when deciding between 3PL vs In-house fulfillment
Choosing between 3PL and in-house fulfillment is a crucial decision for any business, especially those growing in the ecommerce space. Both options have their advantages and disadvantages, so it's important to weigh various factors before making a choice. Here are some key aspects to consider:
Business volume and growth
If you're a startup or if you deal with low order volumes, in-house fulfillment might be the best option. However, as your business grows, the number of orders and SKUs you must fulfill will also grow. In that case, it makes sense to outsource the fulfillment to a 3PL with a lot of experience.
Order complexity and packaging
For products with straightforward packaging in the warehouse and uncomplicated handling, in-house fulfillment is an ideal choice. This approach provides you with complete control over the entire process, enabling customization of packaging to align with your preferences. This level of control proves invaluable, particularly if your brand places emphasis on a specific unboxing experience or if you have unique packaging requirements.
On the other hand, 3PLs are well-suited for complex situations that require diverse packaging needs. For example, if the products your business deals with need special packaging requirements like kitting or storage requirements like cold storage, outsourcing to a 3PL offering specialized expertise and infrastructure for your products is the right choice.
Expertise and Technology
Investing in advanced fulfillment technology for in-house operations can be expensive if you are a growing business. To leverage the benefits of the latest logistics technology, choosing a tech-enabled 3PL is the smartest choice.
Control and visibility
With in-house fulfillment, you have direct control over the entire process, including staffing, inventory management, order processing, and shipping. Additionally, you can customize processes, packaging, and the overall customer experience according to your
brand's specific requirements.
Outsourcing fulfillment to a 3PL may limit the business's control due to standardized processes, restricting the ability to fully customize every aspect of the fulfillment process.
Cost and investment
In-house fulfillment demands substantial upfront investment in various areas, such as warehouse space, equipment, software, and labor. Setting up and maintaining these resources can be capital-intensive, and not many businesses can afford this kind of money.
On the other hand, 3PLs leverage existing infrastructure, distributing the costs across multiple clients. This shared resource model can benefit businesses seeking to avoid large initial expenditures.
3PL vs In House Fulfillment - The Conclusion
In conclusion, the decision between 3PL and in-house fulfillment is a critical one that requires a thorough understanding of your business needs, goals, and resources. Both options come with their own set of advantages and challenges, and there is no one-size-fits-all solution.
Choosing a 3PL provider can offer scalability, expertise, and cost savings, allowing businesses to focus on their core competencies. On the other hand, in-house fulfillment provides greater control, customization, and the potential for higher margins.
Ultimately, the choice should align with your company's specific requirements and long-term strategy. It's essential to conduct a detailed analysis of your supply chain, consider future growth projections, and carefully evaluate the associated costs and benefits.